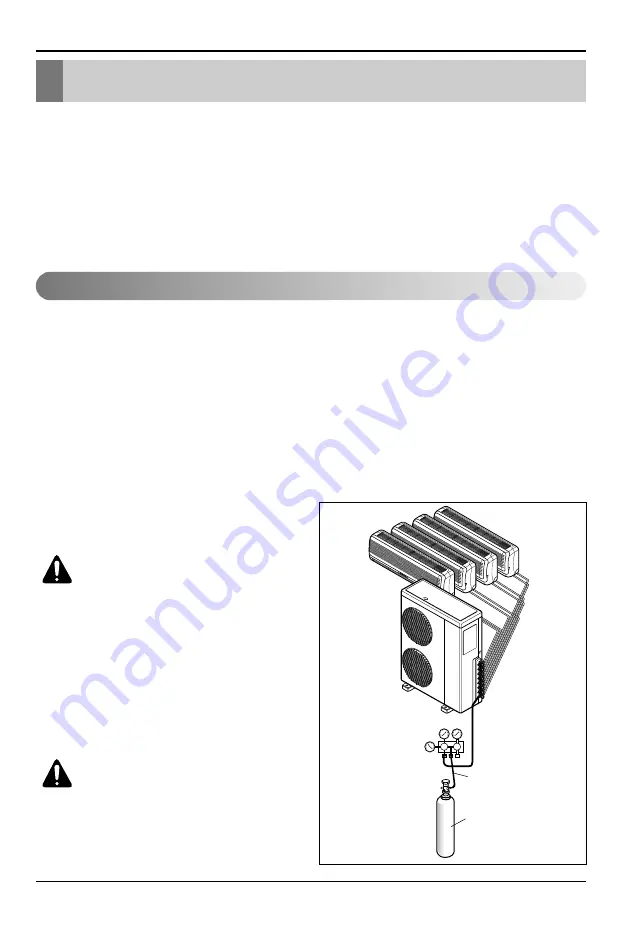
Installation Manual 19
Air Purging and Evacuation
Air Purging and Evacuation
Air and moisture remaining in the refrigerant system have undesirable effects as indicated below.
1. Pressure in the system rises.
2. Operating current rises.
3. Cooling(or heating) efficiency drops.
4. Moisture in the refrigerant circuit may freeze and block capillary tubing.
5. Water may lead to corrosion of parts in the refrigeration system.
Therefore, the indoor/outdoor unit and connecting tube must be checked for leak tight, and
vacuumed to remove incondensible gas and moisture in the system.
Preparation
• Check that each tube(both liquid and gas side
tubes) between the indoor and outdoor units have
been properly connected and all wiring for the test
run has been completed. Remove the service
valve caps from both the gas and the liquid side
on the outdoor unit. Check that both the liquid and
the gas side service valves on the outdoor unit
are kept closed at this stage.
Leakage test
• Connect the manifold valve(with pressure gauges)
and dry nitrogen gas cylinder to this service port
with charge hoses.
CAUTION: Be sure to use a
manifold valve for leakage test.
If it is not available, use a stop valve for
this purpose. The "Hi" knob of the
manifold valve must always be kept
close.
• Pressurize the system to no more than 150
P.S.I.G. with dry nitrogen gas and close the
cylinder valve when the gauge reading
reached 150 P.S.I.G. Next, test for leaks with
liquid soap.
CAUTION: To avoid nitrogen
entering the refrigerant system in a
liquid state, the top of the cylinder must be
higher than its bottom when you pressurize
the system. Usually, the cylinder is used in
a vertical standing position.
1. Do a leakage test of all joints of the
tubing(both indoor and outdoor) and both gas
and liquid side service valves.
Bubbles indicate a leak. Be sure to wipe off
the soap with a clean cloth.
2. After the system is found to be free of leaks,
relieve the nitrogen pressure by loosening the
charge hose connector at the nitrogen
cylinder. When the system pressure is
reduced to normal, disconnect the hose from
the cylinder.
Checking method
Charge hose
Nitrogen gas
cylinder(in vertical
standing position)
Indoor unit
Outdoor unit
Lo
Hi
Manifold valve
Pressure
gauge
Summary of Contents for L4UC488FA0
Page 22: ...P No 3828A21026A ...