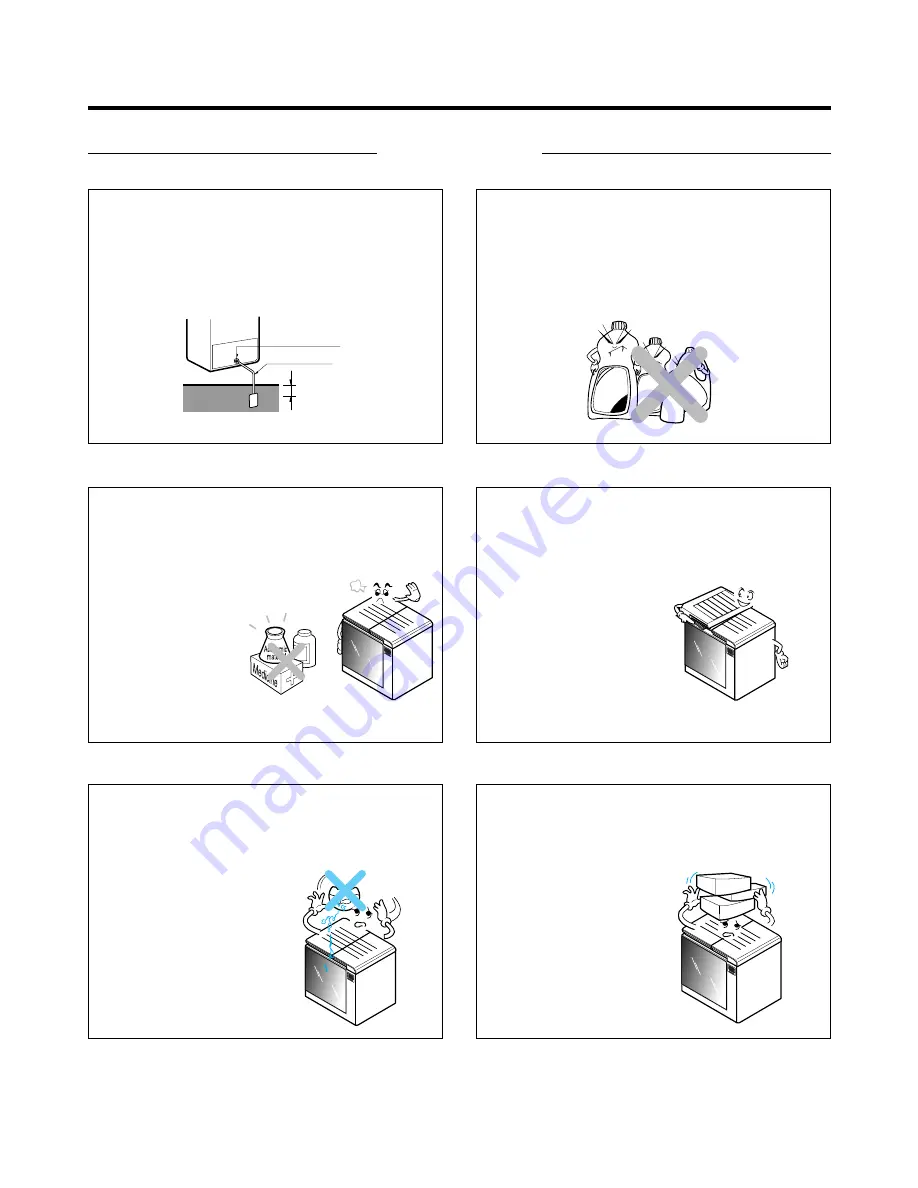
Safety warnings and cautions
- 4 -
This product should always be
grounded, when needed.
If you think that there is a possibility of electricity
leakage by water or moisture, always ground the unit.
More than 7
Grounding screw
Grounding line
Copper plate
Do not store flammable liquid or gas in
the refrigerator such as ether, benzene,
alcohol, medicine, LP gas etc.
It can cause an explosion or a fire.
LP
gas
Ether
Ben
zene
Do not store medicine or academic
material etc. in the refrigerator.
Store an object that
requires precise
temperature control
can cause deterioration
in quality or
unexpected reaction to
cause a dangerous
situation.
Do not set items, particularly flower
vase, cup, cosmetic or medicine on top
of the refrigerator.
It can cause fire and
electric shock or cause an
injury from dropping.
Do not stack items or carelessly store
food on the refrigerator.
Items stored on the
refrigerator could fall
and cause injury.
When disposing the refrigerator,
remove the rubber packing on the door
and do not leave it where children play.
A child can be
dangerously entrapped in
the refrigerator.
w
Warning