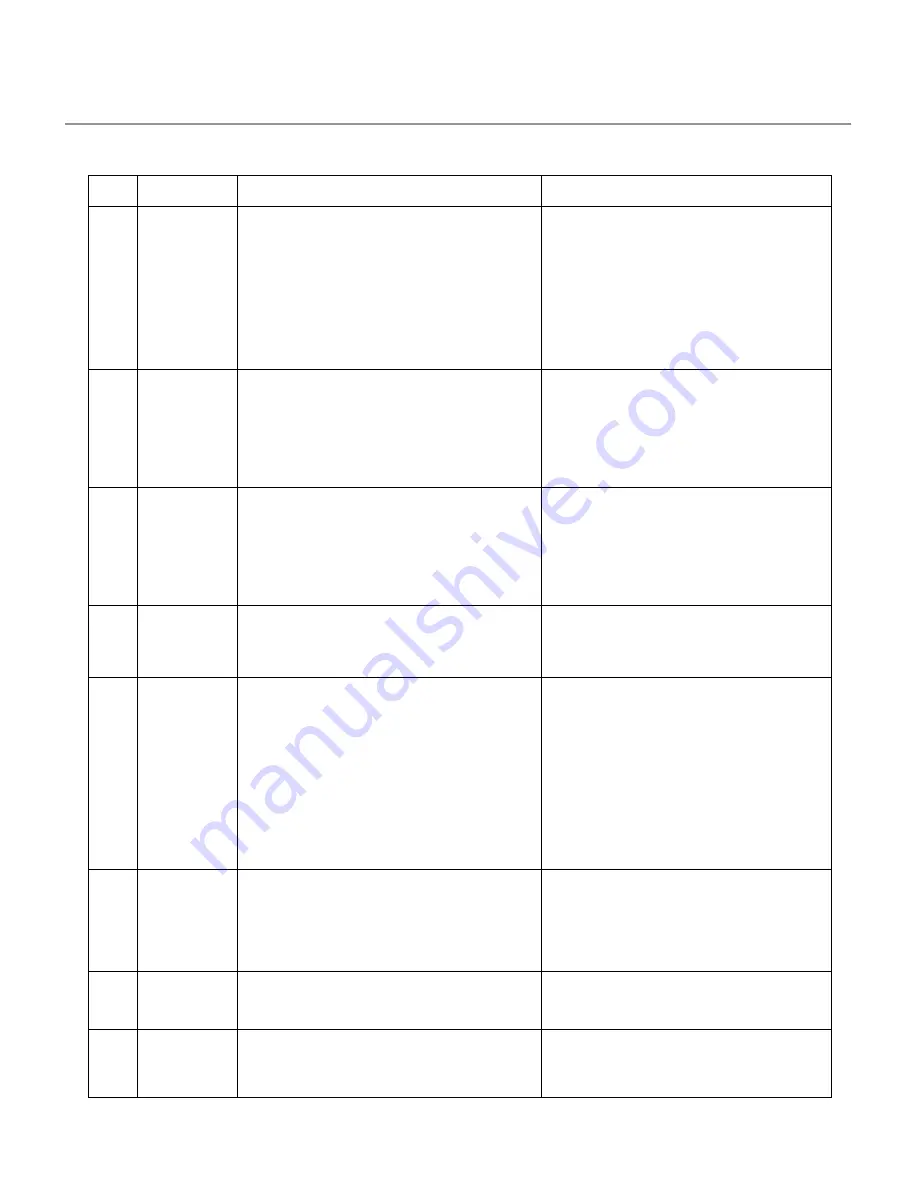
-13-
NO.
ITEMS
CONTENTS AND SPECIFICATIONS
REMARKS
WELDING
(1) H 30
ROD
(1)
• Chemical Ingredients
• Recommend H34 containing 34% Ag in the
(1) •
Ag: 30%, Cu: 27%, Zn: 23%, Cd: 20%
•
Service Center.
(1)
• Brazing Temperature: 710~840°C
(2) Bcup-2
(1)
• Chemical Ingredients
(1) •
Cu: About 93%
(1) •
P: 6.8~7.5%
(1) •
The rest: within 0.2%
(1)
• Brazing Temperature: 735~840°C
FLUX
(1)
• Ingredients and how to make
• Make amount for only day.
(1)
(1) ••
Borax 30%
•
Holding period: 1 day
(1) ••
Borax 35%
• Close the cover of container to prevent dust
(1) •
Fluoridation kalium: 35%
•
putting in the FLUX.
(1) •
Water: 4%
• Keep it in a stainless steel container.
(1) •
Mix the above ingredients and boil until
(1) •
they are transformed into liquid.
LOKRING
(1) Both of the tube is inserted up to the stop.
• For a hermetically sealed metal/metal
(Figure 15, 16) (2) Both of the LOKRING is pushed up to the stop
connection, the tube ends have to be clean.
(3) The bending point is not too close to the
• LOKPREP is distributed all of out-surface of
joint ending.
•
the tube ends.
(4) During the assembly it is important that
both ends remain completely within the
joint.
DRIER
(1) Assemble the drier within 30min.
• Don't keep the drier in a outdoors because
ASM
(1)
after unpacking.
•
humidity damages to it.
(2) Keep the unpacked drier at the temperature
of 80~100°C.
VACUUM
(1) When measuring with pirant Vacuum
• Apply M/C Vacuum Gauge without fail.
(1 )
gauge the charging M/C, vacuum
• Perform vacuum operation until a proper
(1 )
degree is within 1 Torr.
•
vacuum degree is built up.
(2) If the vacuum degree of the cycle inside is
• If a proper vacuum degree isn't built up,
•
(2)
10 Torr. below for low pressure and 20 Torr.
•
check the leakage from
(2)
for high pressure, it says no vacuum
•
the Cycle Pipe line part and
(2)
leakage state.
•
Quick Coupler Connecting part.
(3) Vacuum degree of vacuum pump must be
(3)
0.05 Torr. below after 5 min.
(4) Vacuum degree must be same to the
value described item (2) above for more than
20 min.
(1) The pressure of dry air must be more
han 12~16kg/cm
2
(2) Temperature must be more than
-20~-70°C.
(3) Keep the pressure at 12~6kg/cm
2
also
when substituting dry air for Nitrogen Gas.
NIPPLE
(1) Check if gas leaks with soapy water.
• Check if gas leaks from joint of the
AND
(2) Replace Quick Coupler in case of leakage.
•
Coupler.
COUPLER
PIPE
(1)
• Put all Joint Pipes in a clean box and
(1)•
cover tightly with the lid so that dust or
(1)•
humidity is not inserted.
1
2
3
4
5
6
7
8
DRY AND
AIR
NITROGEN
GAS
▼
General Control of Refrigerating Cycle