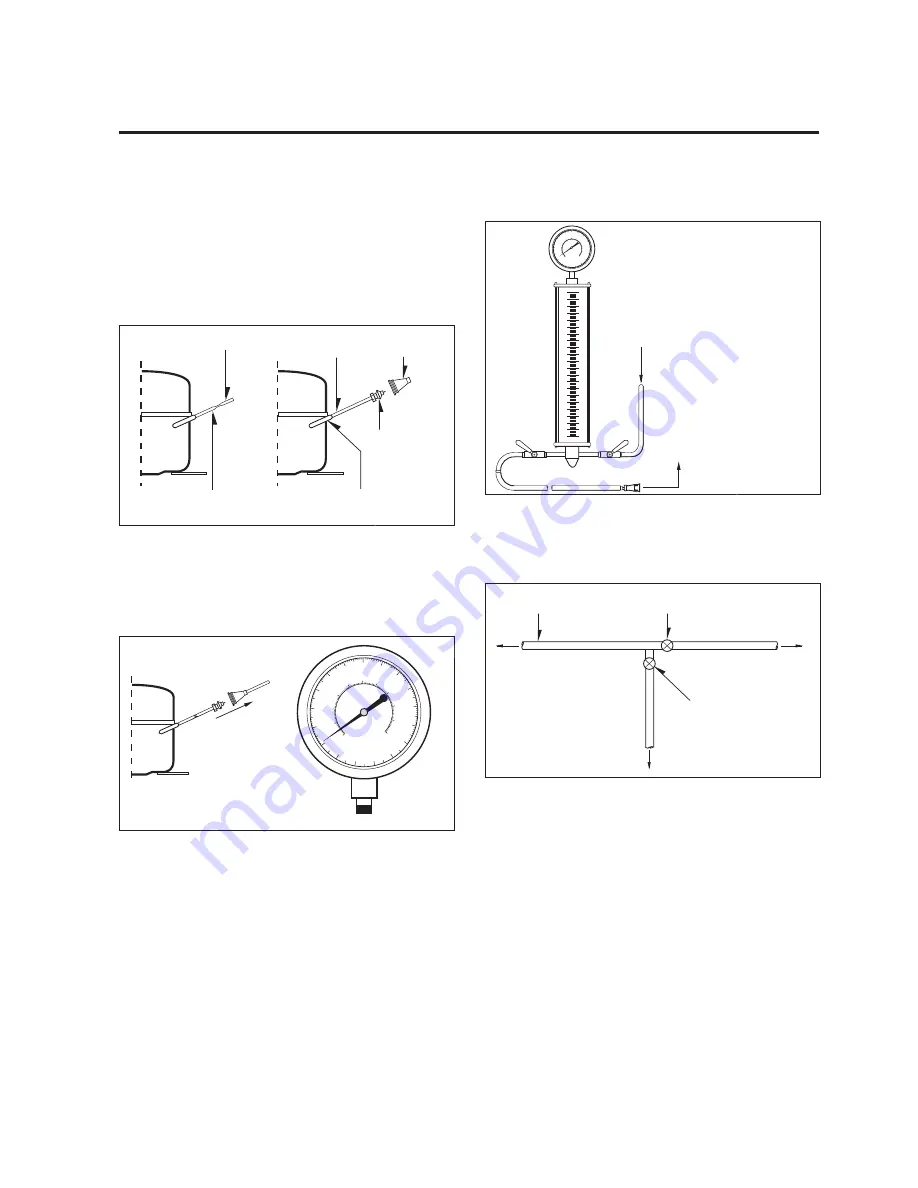
AIR RECHARGING IN COMPRESSOR
Test the refrigeration system connecting it electrically before
refilling operation. It is necessary to ascertain the function
of the motor-compressor and identify the defects
immediately. If defects have been found, empty the old
system of possible R-134a residue by breaking off the end
of the extension piece at its narrow point. (Figure 1)
Replace the filter and any damaged components. Unsolder
and pull off the piece remaining inside the service tube and
then attach an complete extension with male Hansen and
at last, solder it to the same tube again. (Figure 2)
It is necessary to execute the soldering operation with
valve open so that the fumes caused by oil residue can
come out freely without blowholes between two tubes
during the heating the of the point to be soldered.
The extension fitted with the male Hansen is connected to
the female fitting of the vacuum pump tube. (Figure 3)
Air evacuating from the system begins as soon as the
pump starts. The refrigeration system must be kept under
vacuum until the reading on the low-pressure gauge
indicates vacuum (0 absolute, -1 atm., -760 mm hg) in any
case it is advisable to keep the pump running for about 30
minutes. (Figure 3)
In case that a considerable leakage occurs it will be
necessary to stop the vacuum pump and to add asmall
quantity of Freon to the system, if vacuum should not be
obtained (pressure gauge can't fall to 1 atmosphere), start
the refrigeration unit and find the leakage with the special
leak-finder. When the defective soldering point is visible,
re-do it after opening the extension tube valve and
reestablishing the normal outside pressure inside the
group.
Because the melted alloy is sucked into the tubes and
block them, the pressure must be rebalanced when
vacuum is in the system in soldering. As soon as the
vacuum operation is over, add the quantity in grams of
R-134ato the refrigeration system. Remember that every
system has an exact quantity of R-134awith a tolerance of
Before performing this operation (if the vacuum pump and
refilling cylinder are connected), make sure that the valve
placed between the vacuum pump and the refilling tube are
closed in order to keep the Freon for addition to the system.
(Figure 5)
In addition, check the graduated scale on the cylinder for
the quantity of R-134ato be added, for example, if we
have 750 grams of Freon in the cylinder and must add 140
grams to the group, this amount will be reached when
R-134ahas dropped to 610 grams, remembering that the
indicator shows a lower limit of meniscus. Do this after
choosing the scale corresponding to the gas pressure
different scales reported as the same gas pressure
indicated by the pressure gauge on the top of the column.
To make R-134aflow into the system, open the valve
placed at the base of the cylinder and connected to the
filling tube. The amount of Freon cannot be added to the
system all at once because it may cause a blocking of motor-
compressor.Therefore, proceed by adding the original
quantity of about 20-30 grams and close the valve
immediately.
The pressure rises and the motor compressor must start
sucking the gas and lowering the pressure again. Regulate
the valve again, maintaining the same manner until
reaching to the quantity of R-134aestablished for the
system being charged. When the system is running, the
suction pressure must be stabilized between 0.30 to
0.6(0.10 to 0.4) atmosphere.
SERVICING PRECAUTIONS
- 3-
POINT TO BE BROKEN
SERVICE TUBE EXTENSION
CHARGE TUBE
EXTENSION
FEMALE
HANSEN
MALE HANSEN
SOLDERING POINT
Figure 1
Figure 2
TO THE
VACUUM
PUMP
PRESSURE
GAUGE
Figure 3
TO THE R-134a CYLINDER
TO THE REFRIGERATION
SYSTEM
Figure 4
FILLING OR
VALVE TO BE OPENED
CHARGE TUBE
WHEN REFILLING
TO THE REFRIGERATION
TO THE CHARGE
SYSTEM
CYLINDER
VALVE TO BE CLOSED
AFTER VACUUM
TO THE
VACUUM
PUMP
Figure 5
5 grams that can be added. (Figure 4)
Summary of Contents for GN-U192SL
Page 13: ......
Page 20: ...P No 3828JP8007D ...