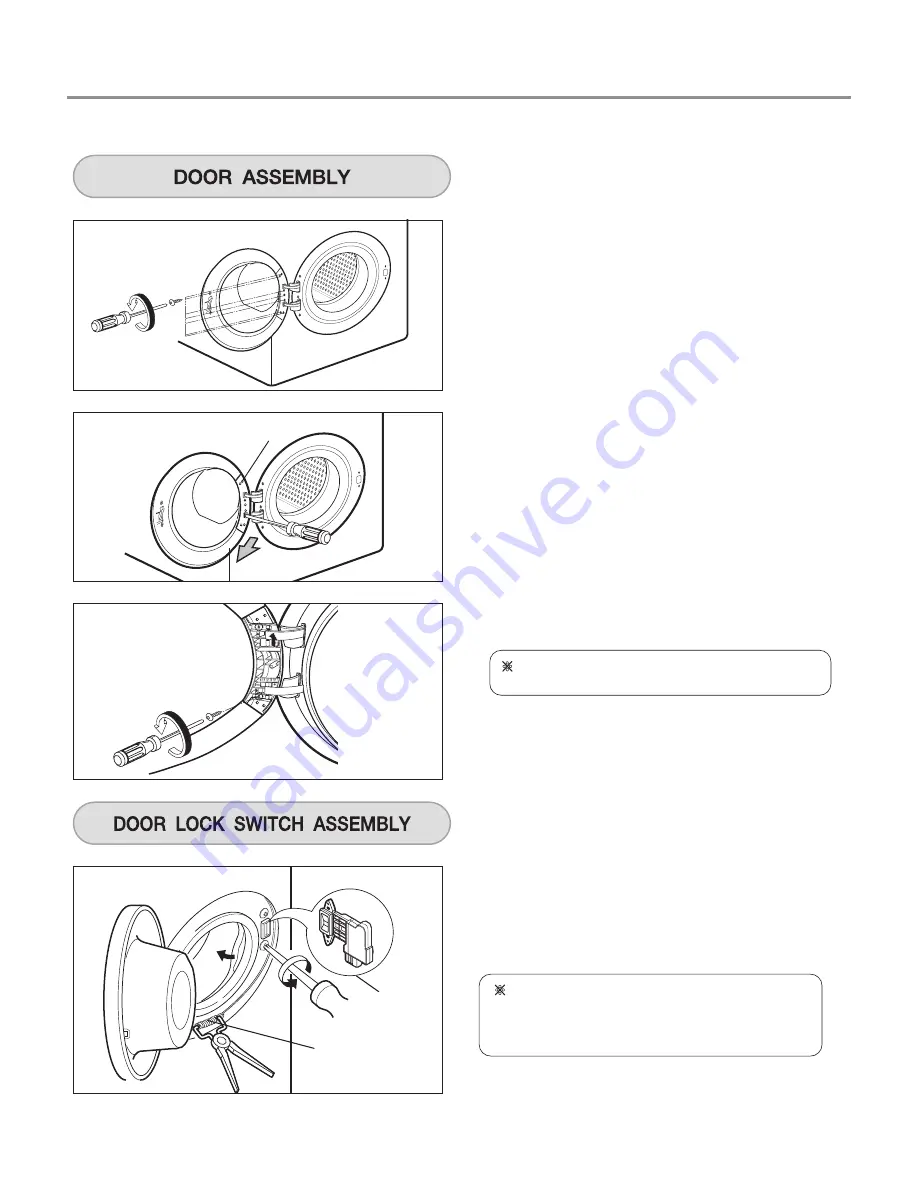
43
1. Open the DOOR.
2. Unscrew the 7 screws from the HINGE COVER.
3. Put a flat ( - ) screwdriver into the openng of the hinge, and
pull out the HINGE COVER.
4. Unscrew a screw from the lower side of DOOR.
5. Lift door and remove.
HINGE COVER
1. Open the DOOR and disassemble the CLAMP
ASSEMBLY.
2. Unscrew the 2 screws.
3. Remove connector from DOOR S/W ASSEMBLY.
DOOR SWITCH
ASSEMBLY
CLAMP
ASSEMBLY
Be careful!
The door is heavy.
NOTE
Reconnect the connector after replacing the
DOOR SWITCH ASSEMBLY.
Summary of Contents for GCWF1069CD1
Page 6: ...6 ...
Page 26: ...26 AC 120V 60Hz 20 ...
Page 30: ...30 ...
Page 32: ...32 dE1 dE2 dE1 dE2 ...
Page 34: ...34 ...
Page 50: ...MFL68921819 ...