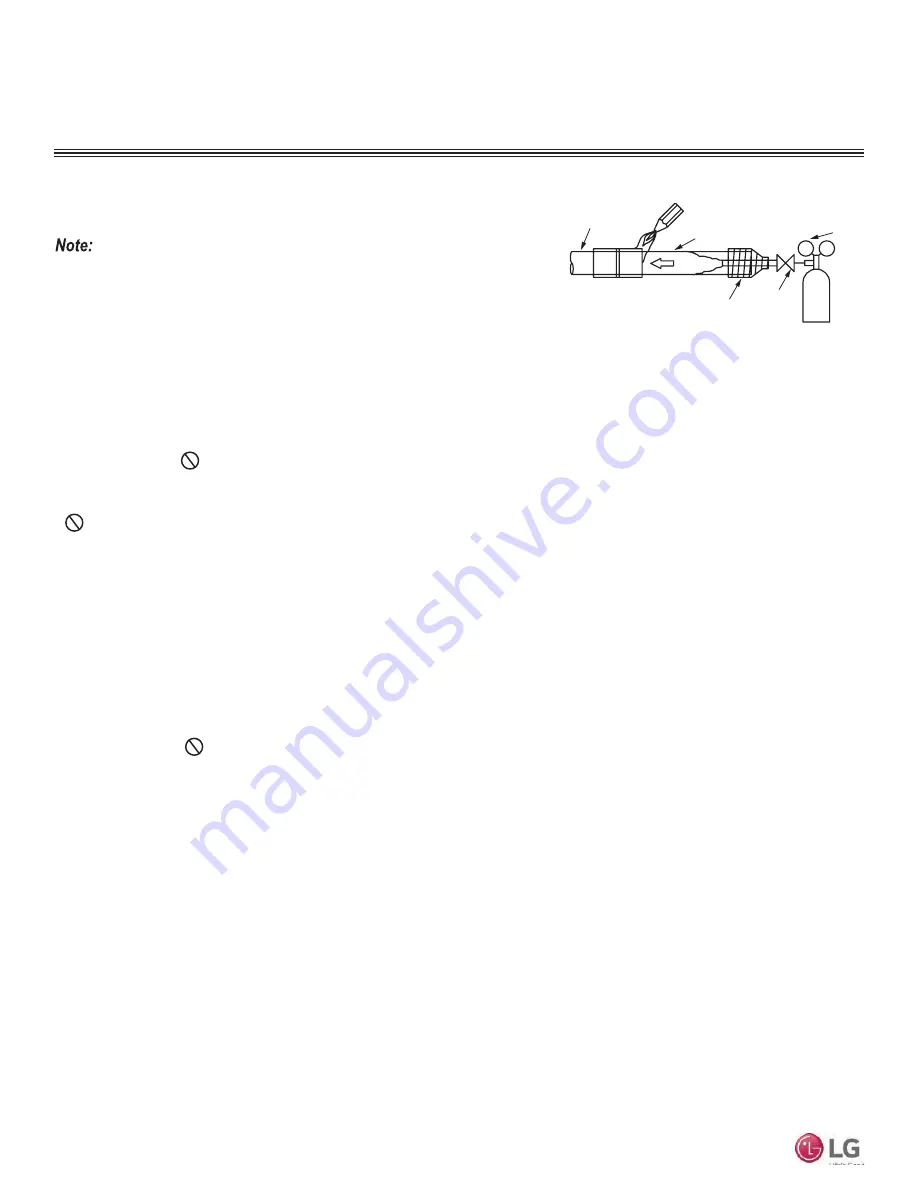
22
Single Zone
Art Cool Premier W
all Mounted Installation Manual
Due to our policy of continuous product innovation, some specifications may change without notification.
©LG Electronics U.S.A., Inc., Englewood Cliffs, NJ. All rights reserved. “LG” is a registered trademark of LG Corp.
GENERAL INSTALLATION GUIDELINES
Figure 20: Refrigerant Pipe Brazing
Pressure-reducing
Valve
Valve
Taping
Nitrogen
Pipe to
be brazed
Refrigerant
Piping
It is imperative to keep the piping system free of contaminants and debris such
as copper burrs, slag, or carbon dust during installation. Contaminants can
result in mechanical failure of the system.
Brazing Practices
Piping Materials and Handling
All joints are brazed in the field. Duct Free System Single Zone Inverter refrigeration system components contain very small capillary tubes,
small orifices, electronic expansion valves, oil separators, and heat exchangers that can easily become blocked. Proper system operation
depends on the installer using best practices and utmost care while assembling the piping system.
• While brazing, use a dry nitrogen purge operating at a minimum pressure of three (3) psig and maintain a steady flow.
• Blow clean all pipe sections with dry nitrogen prior to assembly.
• Use a tubing cutter. Do not use a saw to cut pipe. De-burr and clean all cuts before assembly.
• Store pipe stock in a dry place. Keep pipe capped and clean.
• Use adapters to assemble different sizes of pipe.
• Do not use flux, soft solder, or anti-oxidant agents.
• Use a 15% silver phosphorous copper brazing alloy to avoid overheating and produce good flow.
• Protect isolation valves, electronic expansion valves, and other heat-sensitive control components from excessive heat with a wet rag or a
heat barrier spray product.
Refrigerant Piping System Insulation
All refrigerant piping, field-provided isolation ball valves, service valves, and elbows shall be completely insulated using closed cell pipe
insulation. The liquid and vapor lines must be insulated separately.
To prevent heat loss/heat gain through the refrigerant piping, all refrigerant piping including liquid lines and vapor lines shall be insulated sep-
arately. Insulation shall be a minimum 1/2″ thick, and thickness may need to be increased based on ambient conditions and local codes.
All insulation joints shall be glued with no air gaps. Insulation material shall fit snugly against the refrigeration pipe with no air space be-
tween it and the pipe. Do not allow insulation passing through pipe hangers, inside conduit, and/or sleeves to be compressed. Protect
insulation inside hangers and supports with a second layer. All pipe insulation exposed to the sun and outdoor elements shall be properly
protected with PVC, aluminum vapor barrier, or alternatively placed in a weather-resistant enclosure such as a pipe rack with a top cover and
meet local codes.
The design engineer should perform calculations to determine if the factory-supplied insulation jackets are sufficient to meet local codes and
avoid sweating. Add additional insulation if necessary. Mark all pipes at the point where the insulation jacket ends. Remove the jacket. Install
field provided insulation on the run-out and main trunk pipes first. Peel the adhesive glue protector slip from the insulation jacket and install
the clam-shell jacket over the fitting.
For specific insulation procedures, see
Refrigerant Piping Connections
section in this installation manual.