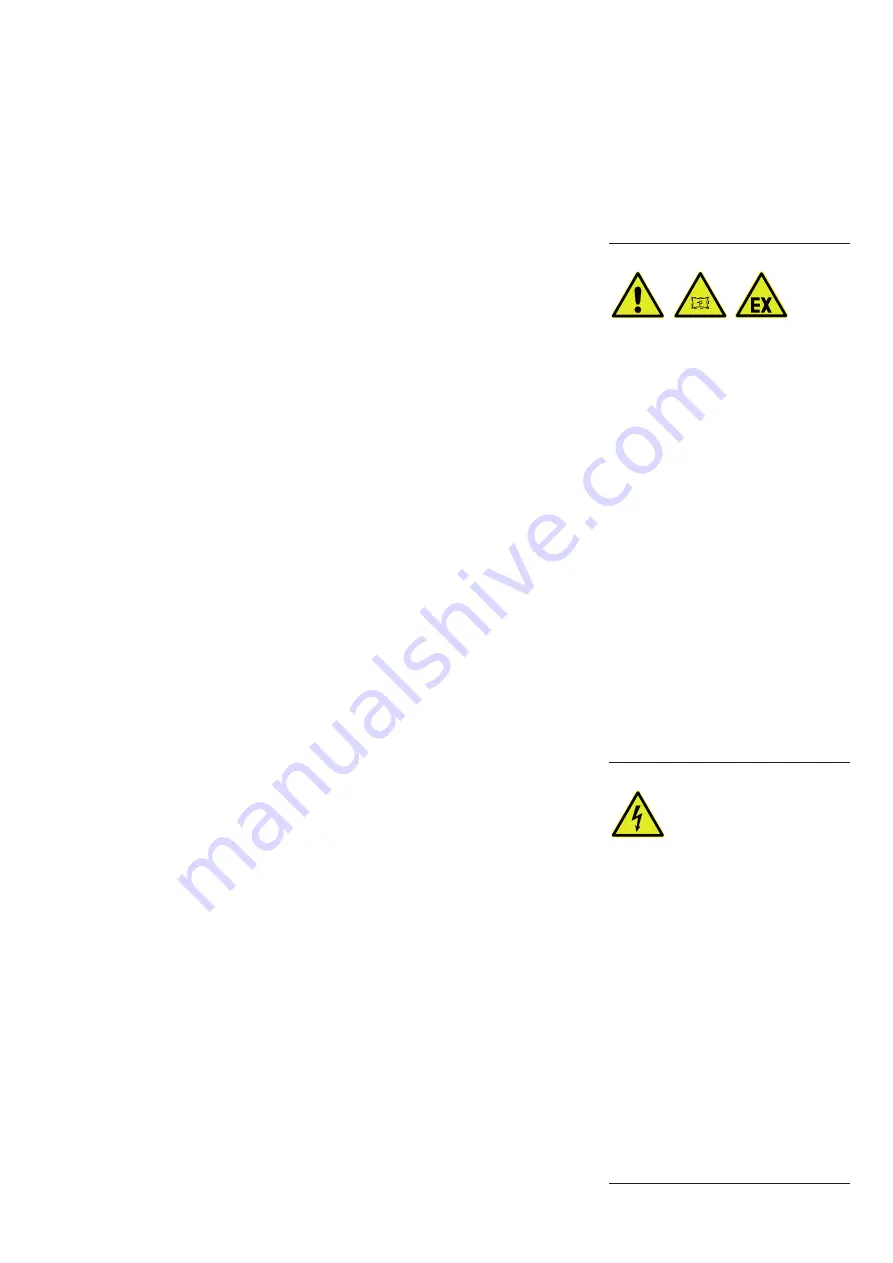
Safety Information
5
GA01212_002_C1 - 04/2017 - © Leybold
0
Important Safety Information
0.1 Mechanical hazards
1
Avoid exposing any part of the human body to the vacuum.
2
Never operate the pump without a connected intake line or without fit-
ting a blank flange.
3
Do not operate the pump with any of the covers removed.
Serious injury may result.
4
The location at which the TRIVAC B (including its accessories) is being
operated should be such that angles over 10° from the vertical are
avoided. Select the operating place so that all controls are easily
accessible.
5
The pump when filled with oil must only be moved in its vertical posi-
tion. Spilled oil involves the risk of falling.
6
Make sure that the gas flow from the exhaust port is not blocked or
restricted in any way.
7
If exhaust gases must be collected or contained, do not allow the
exhaust line to become pressurised. The pressure in the oil box must
not exceed 0.5 bar relative to the atmospheric pressure. An exhaust
line which is too small in diameter or which is blocked can result in the
formation of overpressures within the pump. Possible consequences
can be a damaged or even burst open pump. Thus the exhaust line
must be checked from time to time to ensure that there are no
obstructions.
8
When moving the TRIVAC B always use the allowed means.
0.2 Electrical hazards
1
The electrical connection must only be provided by a trained person.
Please observe the national regulations in the country of use like EN
50110-1 for Europe, for example.
2
Lethal voltages are present at the mains connections. Before starting
with any maintenance and service work, de-energise (lockout/tagout)
the product first.
3
Lay connecting lines so that they cannot be damaged. Protect the
lines against humidity and contact with water. Avoid any heat stress on
the line due to unfavourable laying conditions.
4
Suitably support the connecting lines so that the pumps are not
exposed to any major mechanical stress.
5
After a mains power failure the pump will run up automatically again.
This also applies in the case of an emergency shutdown. In order to
prevent the pump from running up automatically again, the pump must
be inte grated within a control arrangement such that it can only be
switched on manually again after the mains power has returned.
6
Provide an adequate ground connection for the pump so as to avoid
any electrostatic charging.
WARNING
WARNING