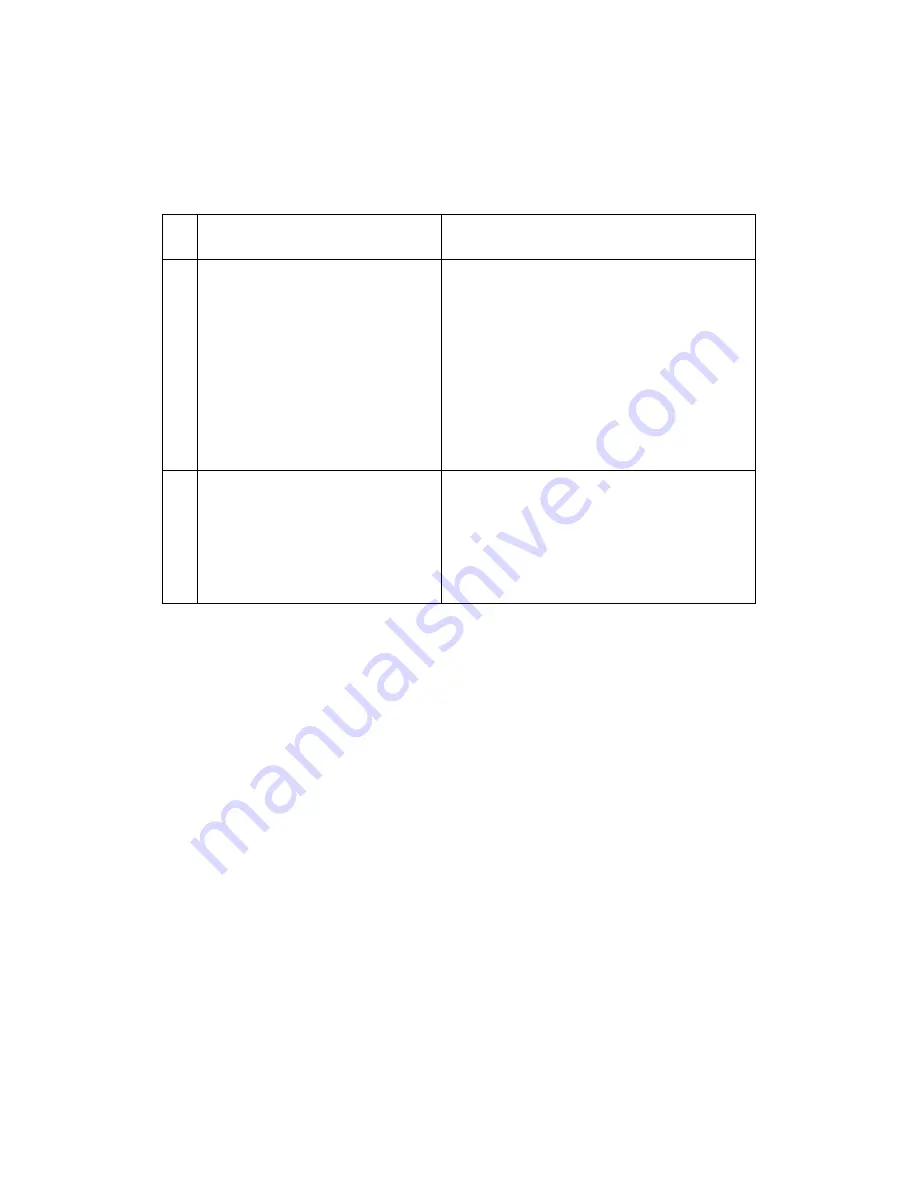
Diagnostic Information
2-88
4059-XXX
Double Feeding Paper
Note: If double feeding paper occurs mostly from the bottom of the
stack, check for missing or damaged restraint pads in the tray.
Multipurpose Tray
Paper fails to feed from the multipurpose tray.
The pick roll should make one complete revolution and stop with the
flat side down. If the pick roll turns but does not pick paper, check the
roll for signs of wear, oil or grease on the surface of the pick roll or
slick spots. If you find a problem, replace the pick roll assembly.
Check to ensure the media that is being fed through the
multipurpose tray assembly meets recommended paper
specifications.
FRU
Action
1
Paper
Paper is usually the primary cause of
a double feeding paper problem.
Flex the paper before placing the
paper in the tray. Edge welded paper
is the most common cause of double
feeding. Loading the paper in the
tray in different locations and
directions and using rough paper
and short grain paper also causes
double feeding.
2
Autocompensator
Make sure the counterbalance
spring is not missing, loose or
broken at the top of the
autocompensator arm assembly. If
you find a problem, replace the
autocompensator assembly.
Summary of Contents for Optra S 4059 Series
Page 15: ...Notices and Safety Information xvi 4059 XXX Japanese Laser Notice Chinese Laser Notice...
Page 227: ...Connector Locations 5 2 4059 XXX...
Page 234: ...5 9 4059 Service Manual 4059 XXX Level 1 Engine Board...
Page 235: ...Connector Locations 5 10 4059 XXX Level 2 Engine Board...
Page 238: ...5 13 4059 Service Manual 4059 XXX...
Page 243: ...Connector Locations 5 18 4059 XXX...
Page 254: ...7 2 4059 Service Manual 4059 XXX Assembly 1 Covers...
Page 256: ...7 4 4059 Service Manual 4059 XXX Assembly 1 Covers continued...
Page 258: ...7 6 4059 Service Manual 4059 XXX Assembly 2 Frame...
Page 260: ...7 8 4059 Service Manual 4059 XXX Assembly 2 Frame continued...
Page 262: ...7 10 4059 Service Manual 4059 XXX Assembly 3 Printhead...
Page 264: ...7 12 4059 Service Manual 4059 XXX Assembly 4 Paper Feed Autocompensator...
Page 266: ...7 14 4059 Service Manual 4059 XXX Assembly 5 Paper Feed Multipurpose Unit...
Page 268: ...7 16 4059 Service Manual 4059 XXX Assembly 6 Paper Feed Alignment...
Page 270: ...7 18 4059 Service Manual 4059 XXX Assembly 7 Paper Feed Output...
Page 272: ...7 20 4059 Service Manual 4059 XXX Assembly 8 Integrated Paper Tray 250 Sheet...
Page 274: ...7 22 4059 Service Manual 4059 XXX Assembly 9 Main Drive...
Page 276: ...7 24 4059 Service Manual 4059 XXX Assembly 10 Developer Drive...
Page 278: ...7 26 4059 Service Manual 4059 XXX Assembly 11 Fuser...
Page 280: ...7 28 4059 Service Manual 4059 XXX Assembly 11 Fuser continued...
Page 282: ...7 30 4059 Service Manual 4059 XXX Assembly 11 Fuser continued...
Page 284: ...7 32 4059 Service Manual 4059 XXX Assembly 12 Transfer...
Page 286: ...7 34 4059 Service Manual 4059 XXX Assembly 13 Charging...
Page 288: ...7 36 4059 Service Manual 4059 XXX Assembly 14 Electronics...
Page 290: ...7 38 4059 Service Manual 4059 XXX Assembly 14 Electronics continued...
Page 292: ...7 40 4059 Service Manual 4059 XXX Assembly 14 Electronics continued...
Page 294: ...7 42 4059 Service Manual 4059 XXX Assembly 14 Electronics continued...
Page 296: ...7 44 4059 Service Manual 4059 XXX Assembly 14 Electronics continued...
Page 298: ...7 46 4059 Service Manual 4059 XXX Assembly 14 Electronics continued...
Page 300: ...7 48 4059 Service Manual 4059 XXX Assembly 15 250 Sheet Tray...
Page 302: ...7 50 4059 Service Manual 4059 XXX Assembly 15 250 Sheet Tray continued...
Page 304: ...7 52 4059 Service Manual 4059 XXX Assembly 16 500 Sheet Tray...
Page 306: ...7 54 4059 Service Manual 4059 XXX Assembly 16 500 Sheet Tray continued...
Page 308: ...7 56 4059 Service Manual 4059 XXX Assembly 17 500 500 Dual Tray...
Page 310: ...7 58 4059 Service Manual 4059 XXX Assembly 17 500 500 Dual Tray continued...
Page 312: ...7 60 4059 Service Manual 4059 XXX Assembly 18 Duplex...
Page 314: ...7 62 4059 Service Manual 4059 XXX Assembly 18 Duplex continued...
Page 316: ...7 64 4059 Service Manual 4059 XXX Assembly 18 Duplex continued...
Page 318: ...7 66 4059 Service Manual 4059 XXX Assembly 19 Output Expander...
Page 320: ...7 68 4059 Service Manual 4059 XXX Assembly 19 Output Expander continued...
Page 322: ...7 70 4059 Service Manual 4059 XXX Assembly 20 Envelope Feeder...
Page 324: ...7 72 4059 Service Manual 4059 XXX Assembly 20 Envelope Feeder continued...
Page 326: ...7 74 4059 Service Manual 4059 XXX Assembly 21 High Capacity Feeder...
Page 328: ...7 76 4059 Service Manual 4059 XXX Assembly 21 High Capacity Feeder continued...
Page 330: ...7 78 4059 Service Manual 4059 XXX Assembly 21 High Capacity Feeder continued...
Page 332: ...7 80 4059 Service Manual 4059 XXX Assembly 21 High Capacity Feeder continued...
Page 334: ...7 82 4059 Service Manual 4059 XXX Assembly 21 High Capacity Feeder continued...
Page 336: ...7 84 4059 Service Manual 4059 XXX Assembly 22 Kiosk Vertical Paper Adapter...
Page 338: ...7 86 4059 Service Manual 4059 XXX Assembly 23 Kiosk Horizontal Paper Adapter...