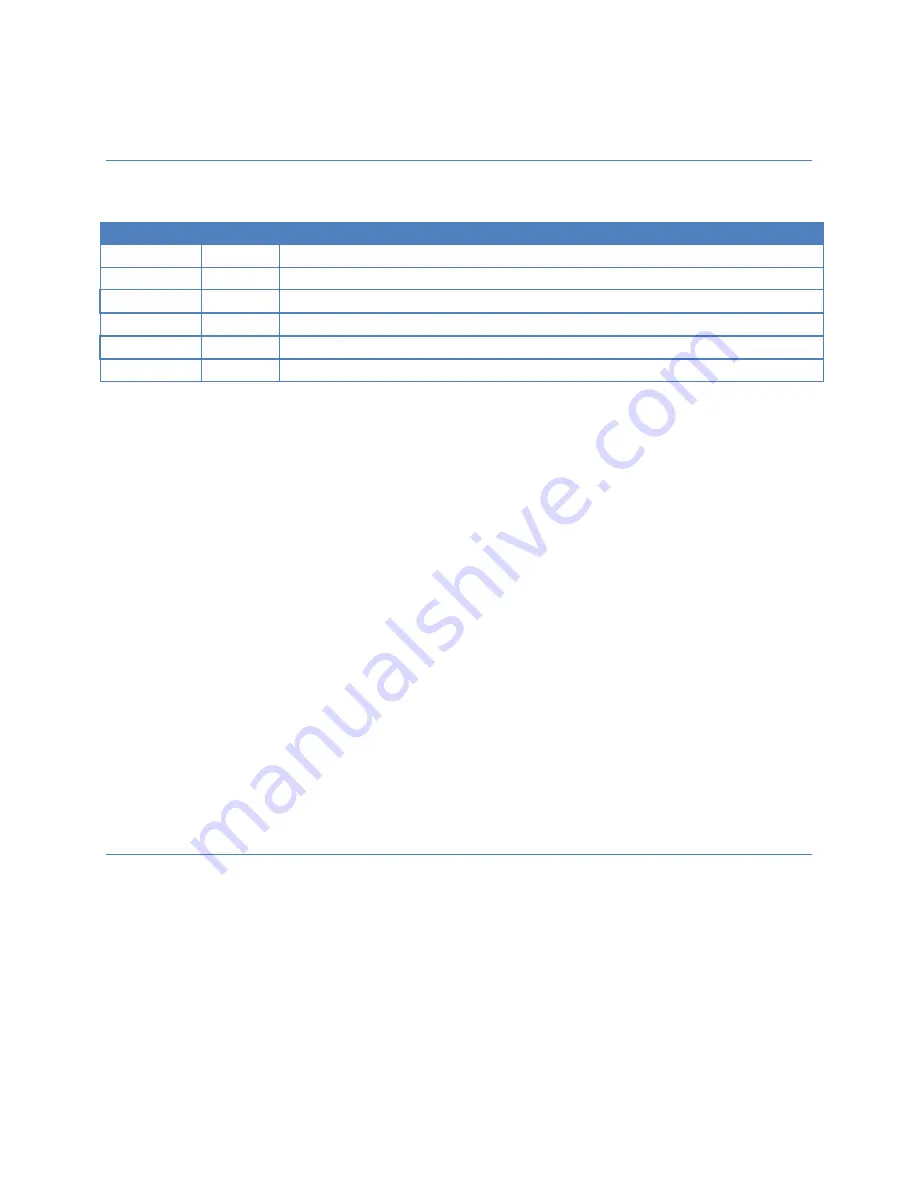
v
Revision Record
DATE
Rev No.
Description
2015-11-19
01
First Release
2015-11-20
02
Updated Spare Parts Numbers
2016-04-29
03
Complete update
2016-06-27
04
Drawing updates; text revisions; addition of sections 7 & 8
2016-08-30
05
Revised Figs 5 & 7, all section 9. Changed title. Text updates.
2016-12-13
06
Revised to included multiple VFD types; extended to include new models
Warranty
This product is guaranteed to be free of defects in materials or workmanship for a period of one (1) year
from date of delivery. Lev-co undertakes to repair and/or replace any such defect within the warranty
period at no cost to the client. Any action by the client involving attempted repair and/or replacement
either by himself or a third party voids this and all warranties.
If such exists, Lev-co extends the warranty of the manufacturer(s) for components used in this product
under the terms stipulated in said warranty(ies). No other warranty is either express or implied.
Summary of Contents for 13-12
Page 35: ......
Page 36: ......
Page 37: ......
Page 38: ......
Page 39: ......
Page 41: ......
Page 42: ......
Page 43: ......
Page 44: ......
Page 45: ......
Page 46: ......
Page 47: ......
Page 48: ......
Page 49: ......
Page 50: ......
Page 51: ......
Page 52: ......
Page 53: ......
Page 54: ......
Page 55: ......
Page 56: ......
Page 57: ......
Page 58: ......
Page 59: ......
Page 60: ......
Page 61: ......
Page 62: ......
Page 63: ......
Page 64: ......
Page 65: ......
Page 66: ......
Page 67: ......
Page 68: ......
Page 69: ......
Page 70: ......
Page 71: ......
Page 72: ......
Page 73: ......
Page 74: ......
Page 75: ......
Page 76: ......
Page 77: ......
Page 78: ......
Page 79: ......
Page 80: ......
Page 81: ......
Page 82: ......
Page 83: ......
Page 84: ......
Page 85: ......
Page 86: ......
Page 87: ......
Page 88: ......
Page 89: ......
Page 90: ......
Page 91: ......
Page 92: ......
Page 93: ......
Page 94: ......
Page 95: ......
Page 96: ......
Page 97: ......
Page 98: ......
Page 99: ......
Page 100: ......
Page 101: ......
Page 102: ......
Page 103: ......
Page 104: ......
Page 105: ......
Page 106: ......