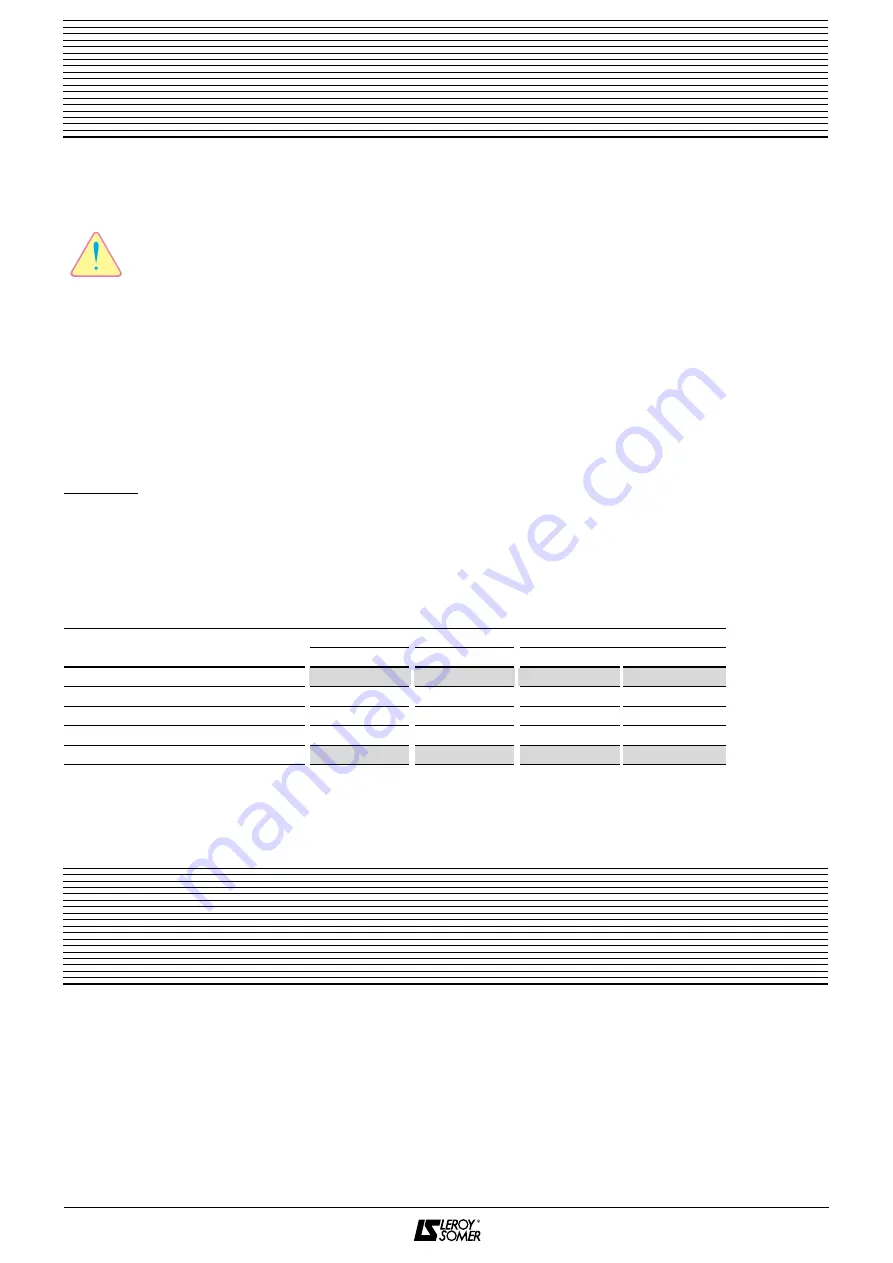
5. - SERVICING
5.1 - First operation
Check that electrical machinery is properly
grounded before carrying out the first
operation to protect the staff from electric
shock.
Run the machine and check the following points :
- abnormal noise,
- vibrations,
- action of switch contacts,
- all fixings and electrical connections are fully tightened,
- the state of the bearings,
- abnormal running,
- that the blower motor (when installed) is rotating in the
correct direction.
- Check also the currrent and the voltage on the machine
when it is running with rated load.
Important:
never run the machine without the blower
switched on.
5.2 - Maintenance
During service visits, for an optimized life expectancy of
the machine, proceed with the following operations.
5
X2- X3 - AC Gearless
Servicing
5.2.1 - Every month
-
Check for loose bolts, nuts or electrical connections.
-
Check for abnormal noise, vibration or abnormal
running.
- Remove grease traces (if any) on the sheave and
brake drum 28.
5.2.2 - After one month, then every six months
-
Check the brake springs are properly adjusted. If they
are not, the springs must be readjusted (see section
4.4.2).
- Check the plunger stroke is properly adjusted. If it is
not, the plunger stroke must be readjusted (see section
4.4.3).
5.2.3 - Every five years
- Secondary sheave bearing maintenance
Unscrew the two plugs. Replace them by a grease nip-
ple. Grease with 70 to 75 g of the original grease (speci-
fied on Name plate).
Periodicity
Parts
1 month
6 months
1 year
5 years
Inspection and adjustments
Bolts and nuts tightening
●
Noise & vibration inspection
●
Brake spring and stroke inspections
●
Greasing
secondary sheave
6. - ORDERING SPARE PARTS
To ensure efficient after-sales service, each order for
spare parts should specify the following elements :
- motor type and serial n
°
and for each part :
- part description and (or) identification n
°
,
- quantity ordered
.
For instant identification, please give the reference of the
document used for ordering (plan or manual n
°
). Details
of the type and serial n
°
appear on the motor identifica-
tion plate.
X2 - X3 - AC Gearless
Ordering spare parts