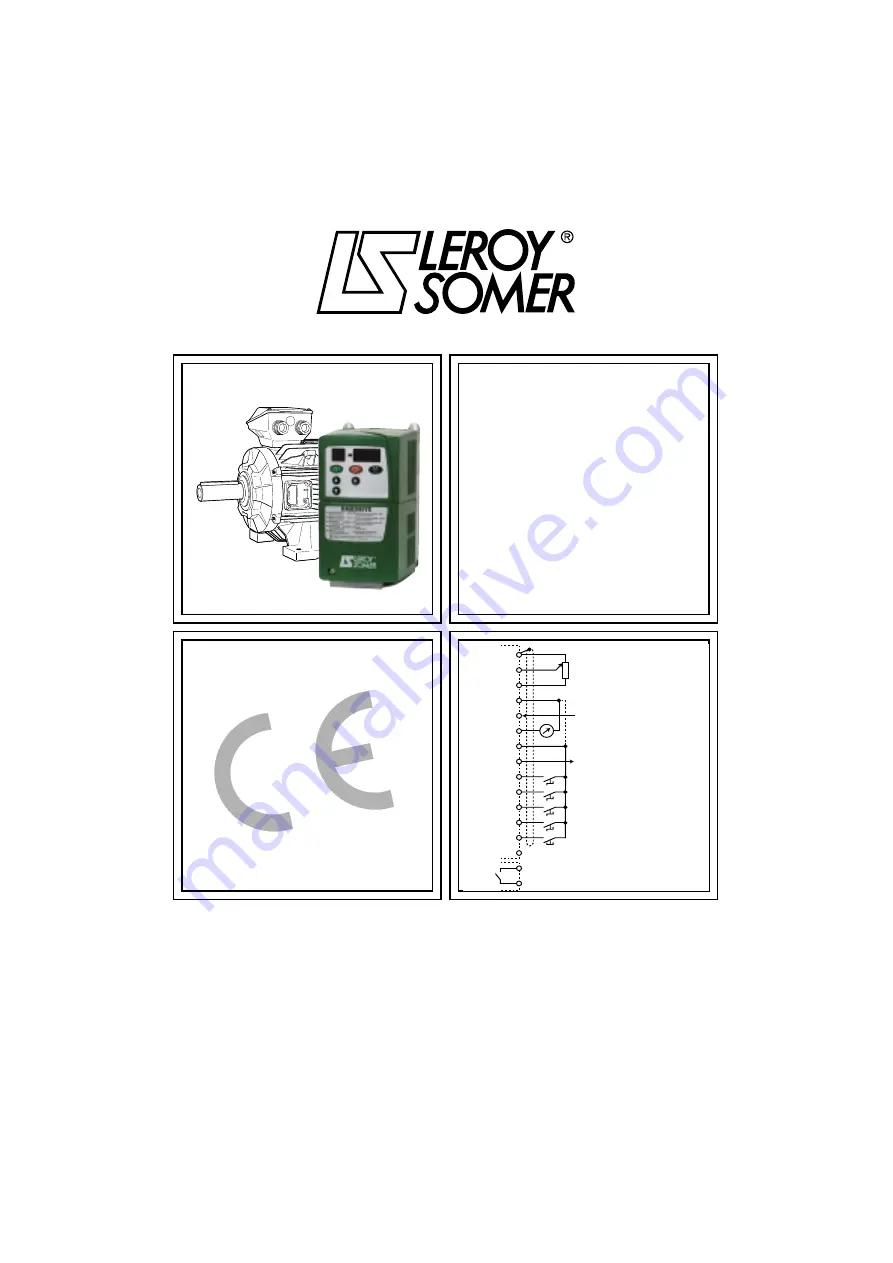
This manual is to be given to
the end user
1
0V
RP
Reference A1
(analogue voltage input)
+10V
0V (negative logic)
Reference A2
(analogue current input)
Analogue output (motor frequency)
+24V (positive logic)
Logic output (zero frequency)
Unlock
Run forward/Stop
Run reverse/Stop
A1/A2 reference selection
Jog
(see
15
in section 4.8)
Fault relay
2
3
4
5
6
7
PL1
PL2
8
9
10
11
12
13
14
15
16
DIGIDRIVE
Variable speed drive
Installation and commissioning
Réf. 3218 GB - 4.33 / d - 02.02