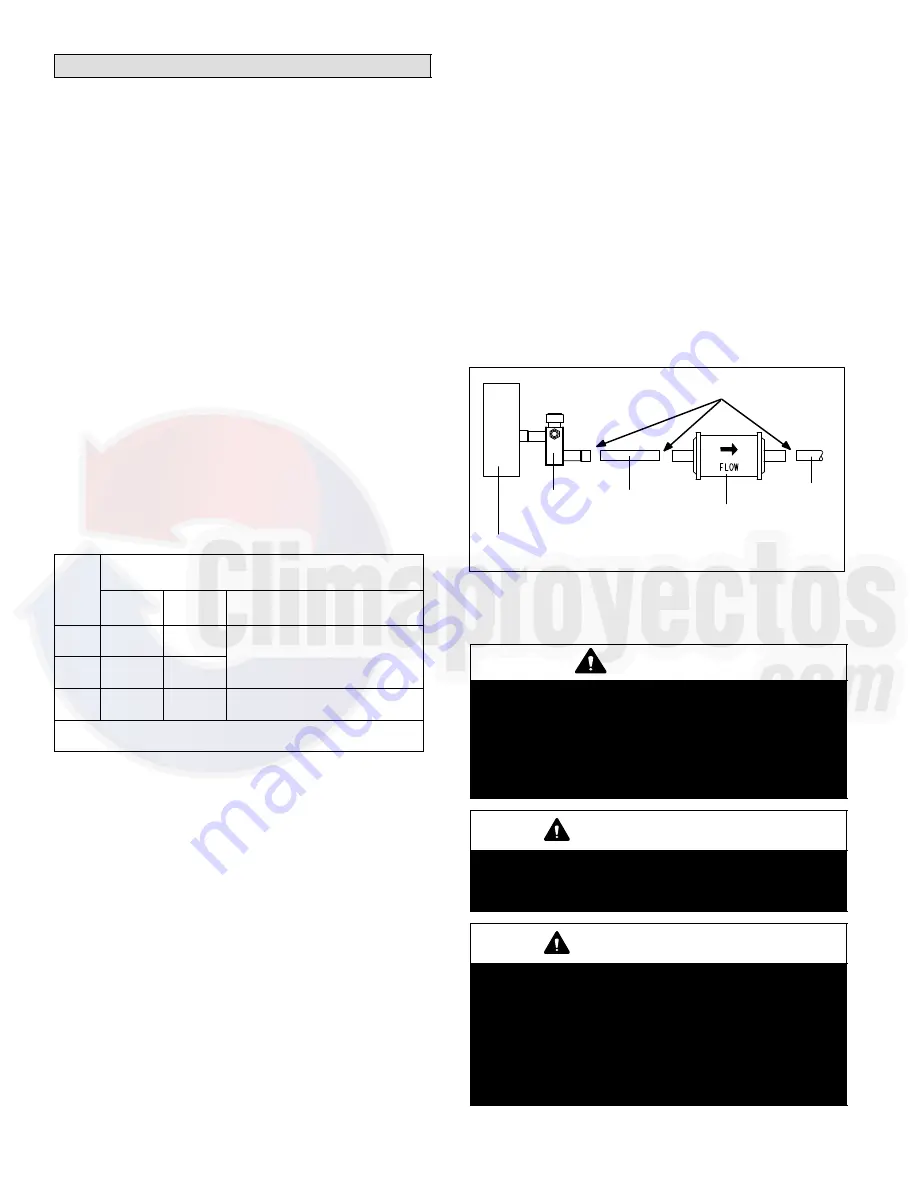
Page 12
New or Replacement Line Set
This section provides information on new installation or
replacement of existing line set. If a new or replacement
line set is not required, then proceed to
Brazing
Connections
If refrigerant lines are routed through a wall, seal and
isolate the opening so vibration is not transmitted to the
building. Pay close attention to line set isolation during
installation of any HVAC system. When properly isolated
from building structures (walls, ceilings. floors), the
refrigerant lines will not create unnecessary vibration and
subsequent sounds.
Also, consider the following when placing and installing a
high−efficiency air conditioner:
REFRIGERANT LINE SET
Field refrigerant piping consists of liquid and suction lines
from the outdoor unit (braze connections) to the indoor unit
coil (flare or braze connections). Use Lennox L15 (braze,
non−flare) series line set, or use field−fabricated refrigerant
lines as listed in Table 2.
Table 2. XP Refrigerant Connections and Line Set
Requirements
Model
Valve Field Connections and Recommended
Line Set
Liquid
Line
Suction
Line
L15 Line Set
−024
−030
3/8 in.
(10 mm)
3/4 in.
(19 mm)
L15 line set sizes are dependent
on unit matchup. See Engineering
Handbook to determine correct line
set sizes.
−036
−048
3/8 in.
(10 mm)
7/8 in.
(22 mm)
−060
3/8 in.
(10 mm)
1−1/8 in.
(29 mm)
Field Fabricated
NOTE Some applications may required a field provided 7/8" to
1−1/8" adapter
NOTE − When installing refrigerant lines longer than 50
feet, contact Lennox Technical Support Product
Applications for assistance or Lennox piping manual. To
obtain the correct information from Lennox, be sure to
communicate the following points:
Model (XP) and size of unit (e.g. −060).
Line set diameters for the unit being installed as listed
in Table 2 and total length of installation.
Number of elbows and if there is a rise or drop of the
piping.
MATCHING WITH NEW OR EXISTING INDOOR COIL
AND LINE SET
The RFC1−metering line consisted of a small bore copper
line that ran from condenser to evaporator coil. Refrigerant
was metered into the evaporator by utilizing
temperature/pressure evaporation effects on refrigerant in
the small RFC line. The length and bore of the RFC line
corresponded to the size of cooling unit.
If the XP is being used with either a new or existing indoor
coil which is equipped with a liquid line which served as a
metering device (RFCI), the liquid line must be replaced
prior to the installation of the XP unit. Typically a liquid line
used to meter flow is 1/4" in diameter and copper.
LIQUID LINE FILTER DRIER INSTALLATION OR
REPLACEMENT
The filter drier (one is shipped with each XP unit) must be
field installed in the liquid line between the outdoor unit’s
liquid line service valve and the indoor coil’s metering
device (fixed orifice or TXV) as illustrated in Figure 12. This
filter drier must be installed to ensure a clean,
moisture−free system. Failure to install the filter drier will
void the warranty. A replacement filter drier is available
from Lennox. See
Brazing Connections
on Page 14 for
special procedures on brazing filter drier connections to
the liquid line.
OUTDOOR
UNIT
LIQUID LINE
SERVICE VALVE
LIQUID LINE
FILTER DRIER
LINE
LIQUID
LINE
BRAZE CONNECTION POINTS
Figure 12. Typical Liquid Line Filter Drier
Installation
LINE SET ISOLATION
CAUTION
Brazing alloys and flux contain materials which are hazardous to your
health.
Avoid breathing vapors or fumes from brazing operations. Perform
operations only in well ventilated areas.
Wear gloves and protective goggles or face shield to protect against
burns.
Wash hands with soap and water after handling brazing alloys and flux.
IMPORTANT
The Environmental Protection Agency (EPA) prohibits the intentional
venting of HFC refrigerants during maintenance, service, repair and
disposal of appliance. Approved methods of recovery, recycling or
reclaiming must be followed.
IMPORTANT
If this unit is being matched with an approved line set or indoor unit
coil which was previously charged with mineral oil, or if it is being
matched with a coil which was manufactured before January of 1999,
the coil and line set must be flushed prior to installation. Take care to
empty all existing traps. Polyol ester (POE) oils are used in Lennox
units charged with HFC−410A refrigerant. Residual mineral oil can act
as an insulator, preventing proper heat transfer. It can also clog the
expansion device, and reduce the system performance and capacity.
Failure to properly flush the system per the instructions below will
void the warranty.