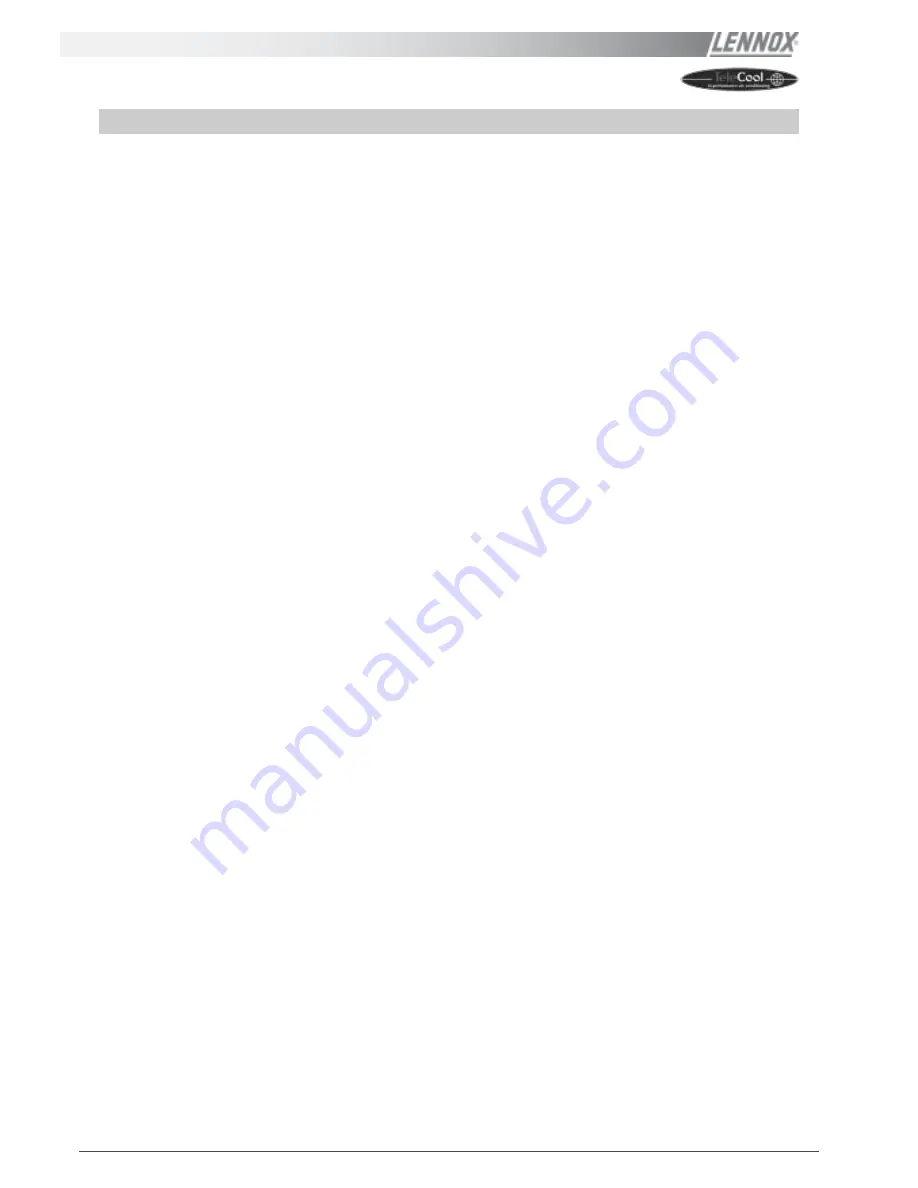
Page 24 - IOM / TELECOOL THN - 0104 - E
TROUBLESHOOTING
FAULT
Presence of abnormally high
pressure
Low condensation pressure
Low evaporation pressure
The compressor does not start
Possible causes
Unit overcharged, as revealed by an
Sub-cooling of more than 8 °C
Thermostatic valve and/or filter
obstructed. These symptoms may also
occur in the presence of an abnormally
low pressure
Transducer fault
Malfunctioning of thermostatic valve
Filter dryer clogged
Low condensation T
Low level of refrigerant
The internal thermal protection device
has tripped
The circuit breakers or line fuses have
been tripped by a short circuit
One of the high or low pressure switches
has tripped
The phases have been inverted in the
distribution compartment
Corrective actions
Drain the circuit
Check the temperatures upstream and
downstream from the valve and filter and
replace them if necessary.
Check the efficiency of the condensation
control device [optional]
Warming the bulb with your hand, check
whether the valve opens and adjust it if
necessary. If it does not respond,
replace it.
Pressure drops upstream and
downstream from the filter should not
exceed 2°C. If they do, replace the filter.
Check the efficiency of the condensation
control device [where present]
Check the refrigerant level by measuring
the degree of Sub-cooling; if it is below
2°C replenish the charge
In the case of compressors equipped
with a protection module, check the
thermal contact. Identify the causes after
restarting.
Pinpoint the cause by measuring the
resistance of the individual windings and
the insulation from the casing before
restoring power.
Check on the microprocessor, eliminate
the causes.
Check the phase sequence relay.