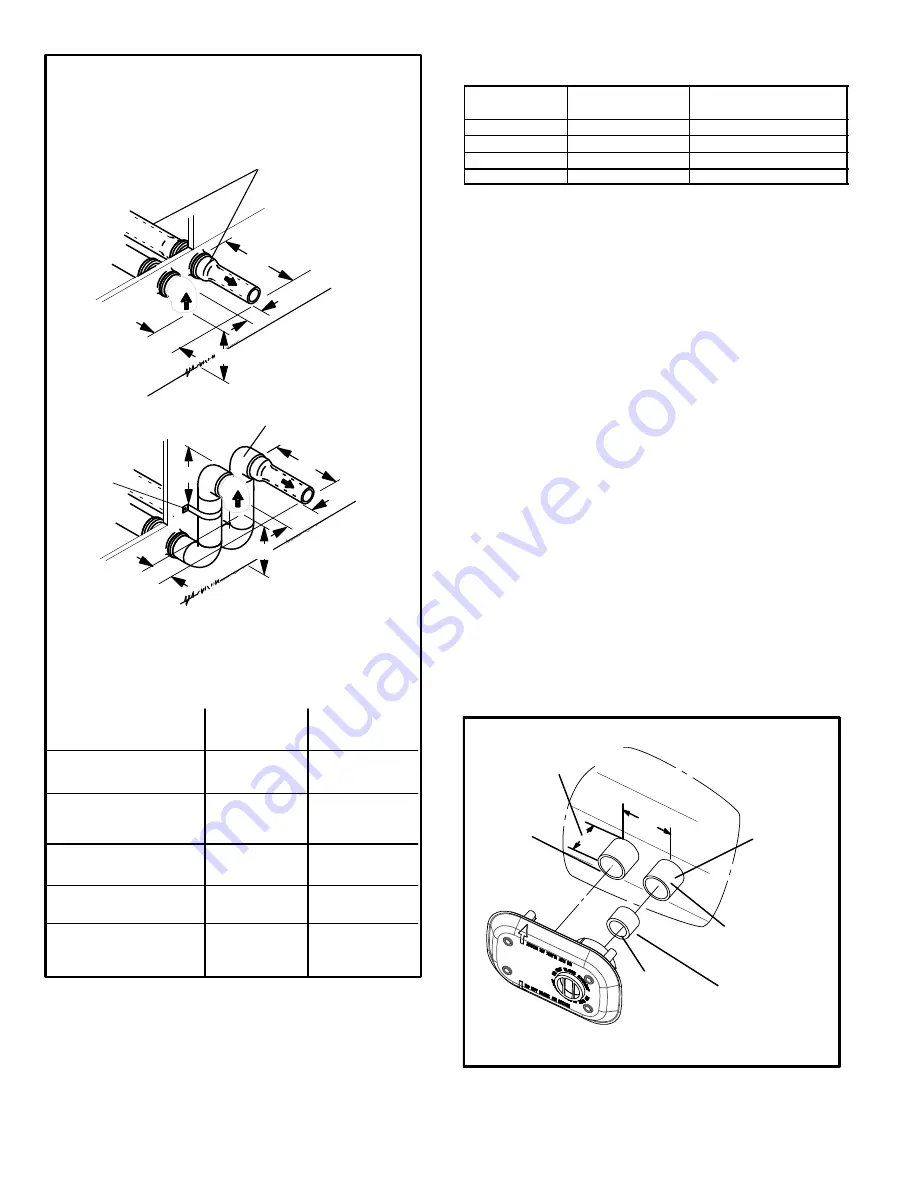
Page 48
FIGURE 29
FIELD−SUPPLIED WALL TERMINATION OR
(15F74) WALL RING TERMINATION KIT
With INTAKE ELBOW
See venting table 23 for maximum venting lengths with this
arrangement.
* Use wall support every 24" (610 mm). Use two wall supports if
extension is greater than 24" (610 mm) but less than 48" (1219 mm).
NOTE − One wall support must be 6" (152 mm) from top of each pipe
(intake and exhaust).
2" (51mm)
Vent Pipe
3" (76mm)
Vent Pipe
12" (508MM)
12" (508MM)
6" (152MM)
6" (152MM)
6" (152MM)
12" (305MM)
20" (508MM)
6" (152MM)
6" (152MM)
6" (152MM)
A
−Minimum clearance
above grade or average
snow accumulation
B
−Maximum horizontal
separation between
intake and exhaust
C
−Minimum from
end of exhaust to
inlet of intake
D
−Maximum exhaust
pipe length
E
−Maximum wall support
distance from top of each
pipe (intake/exhaust)
NOTE − FIELD−PROVIDED
REDUCER MAY BE
REQUIRED TO ADAPT
LARGER VENT PIPE SIZE
TO TERMINATION.
D
B
C
SIZE TERMINATION
PER TABLE 24
1/2" (13mm) ARMAFLEX
INSULATION IN UN-
CONDITIONED SPACE
STRAIGHT
APPPLICATION
B
C
D
* WALL
SUPPORT
1/2" (13mm) ARMAFLEX INSULATION
IN UNCONDITIONED SPACE
E
EXTENDED
APPLICATION
A
A
TABLE 24
EXHAUST PIPE TERMINATION SIZE REDUCTION
SLP98UHV
MODEL
Exhaust Pipe Size
Termination Pipe Size
*070
2", 2−1/2" or 3"
1−1/2"
*090
2", 2−1/2" or 3"
2"
110
2−1/2" or 3"
2"
135
3"
2"
*SLP98UH−070 and −090 units with the flush−mount termina-
tion must use the 1−1/2"accelerator supplied with the kit.
5. On field−supplied terminations for side wall exit, ex-
haust piping may extend a maximum of 12 inches
(305mm) for 2" PVC and 20 inches (508mm) for 3"
(76mm) PVC beyond the outside wall. Intake piping
should be as short as possible. See figures 28 and 29.
6. On field−supplied terminations, a minimum distance
between the end of the exhaust pipe and the end of the
intake pipe without a termination elbow is 8" and a
minimum distance of 6" with a termination elbow. See
figures 28 and 29.
7. If intake and exhaust piping must be run up a side wall
to position above snow accumulation or other ob-
structions, piping must be supported every 24"
(610mm) as shown in figures 28 and 29. In addition,
close coupled wall termination kits must be extended
for use in this application. See figures 36 and 37.
When exhaust and intake piping must be run up an
outside wall, the exhaust piping must be terminated
with pipe sized per table 24.The intake piping may be
equipped with a 90° elbow turndown. Using turndown
will add 5 feet (1.5m) to the equivalent length of the
pipe.
8. Based on the recommendation of the manufacturer, a
multiple furnace installation may use a group of up to
four terminations assembled together horizontally, as
shown in figure 33.
2" EXTENSION FOR 2" PVC PIPE
1" EXTENSION FOR 3" PVC PIPE
FIGURE 30
1−1/2" ACCELERATOR
(ALL 070 AND 090 UNITS)
FURNACE
EXHAUST
PIPE
FURNACE
INTAKE PIPE
4’’
GLUE EXHAUST END
FLUSH INTO
TERMINATION
FLAT SIDE
FLUSH−MOUNT SIDE WALL TERMINATION
51W11