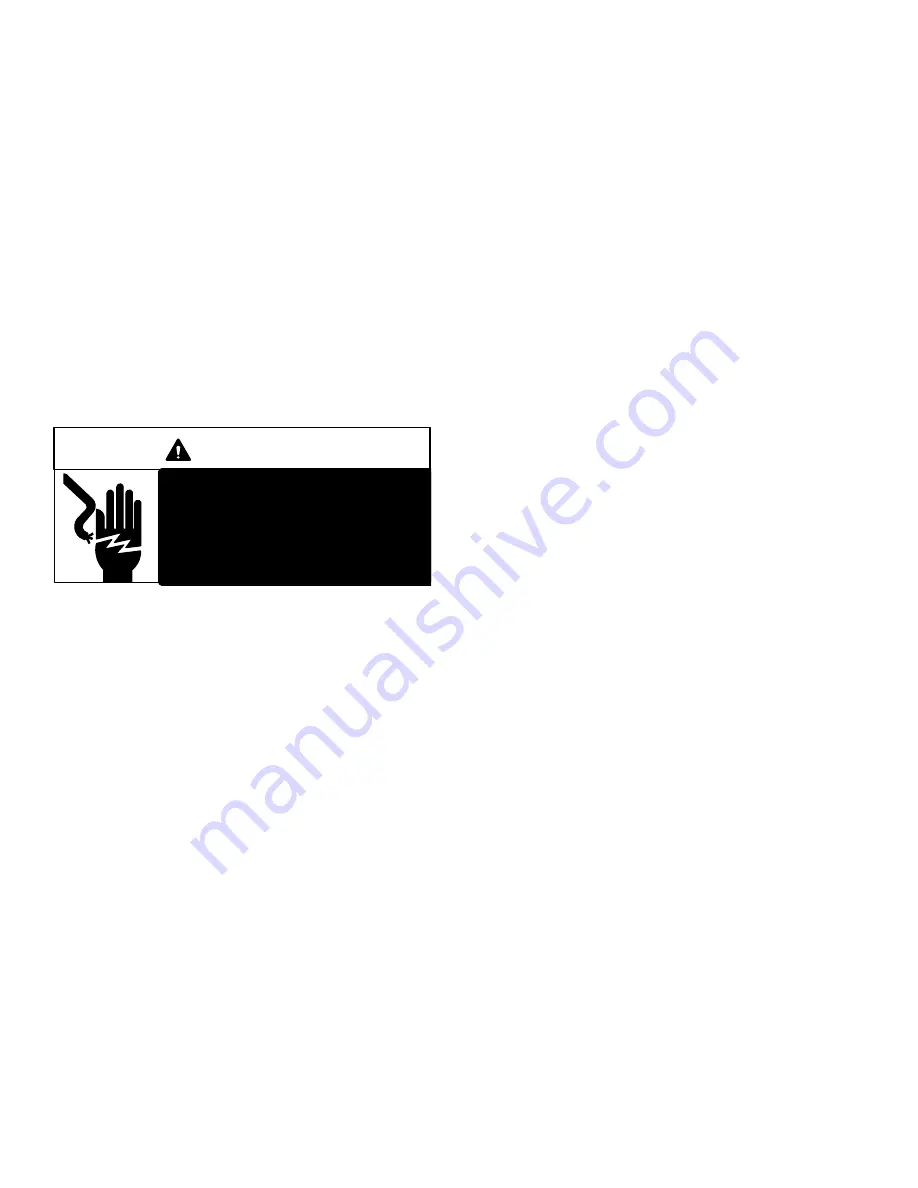
Page 24
Motor Start‐Up
When B3 begins start‐up, the motor gently vibrates back and
forth for a moment. This is normal. During this time the elec
tronic controller is determining the exact position of the rotor.
Once the motor begins turning, the controller slowly eases
the motor up to speed (this is called “soft‐start”). The motor
may take as long as 10‐15 seconds to reach full speed. If the
motor does not reach 200 rpm within 13 seconds, the motor
shuts down. Then the motor will immediately attempt a re
start. The shutdown feature provides protection in case of a
frozen bearing or blocked blower wheel. The motor may at
tempt to start eight times. If the motor does not start after the
eighth try, the controller locks out. Reset controller by momen
tarily turning off power to unit.
The DC filter capacitors inside the controller are connected
electrically to the motor supply wires. The capacitors take
approximately 5 minutes to discharge when the disconnect
is opened. For this reason it is necessary to wait at least 5
minutes after turning off power to the unit before attempt
ing to service motor.
DANGER
Disconnect power from unit and
wait at least five minutes to allow
capacitors to discharge before at
tempting to service motor. Failure
to wait may cause personal injury
or death.
Power Choke (L13)
A choke coil is used on SL280UHNV 4 and 5 ton units
equipped with 1 hp motors. The choke is located on the
blower housing and is used to suppress transient current
spikes.
Troubleshooting Motor Operation
To verify motor operation see steps below and figures 8
and 9.
1- Remove J48 (5 pin power plug) from P48 on the mo
tor.
2- With the power on at the furnace and door switch de
pressed, use a test meter to verify 120V between pins
4 and 5 on J48.
3- Reconnect J48 to P48 on the motor.
4- Remove J49 (4 pin low voltage connector) from P49
on the motor.
5- Using test jumpers, apply 24V to pins 3 and 4 on P49
on the motor.
Note:
Do not apply 24V to pins 2 and 4 on P49. Doing so
will cause permanent damage to the motor.
6- Motor should run at 75%.
7- Test is complete. Remove jumpers and reconnect
plugs.
Another option is to use the TECMate PRO motor tester
with the 16 to 4 pin adaptor. The use of the TECMate PRO
isolates the motor from the integrated control. Follow the
instructions provided with the kit. If the motor runs do not
replace.