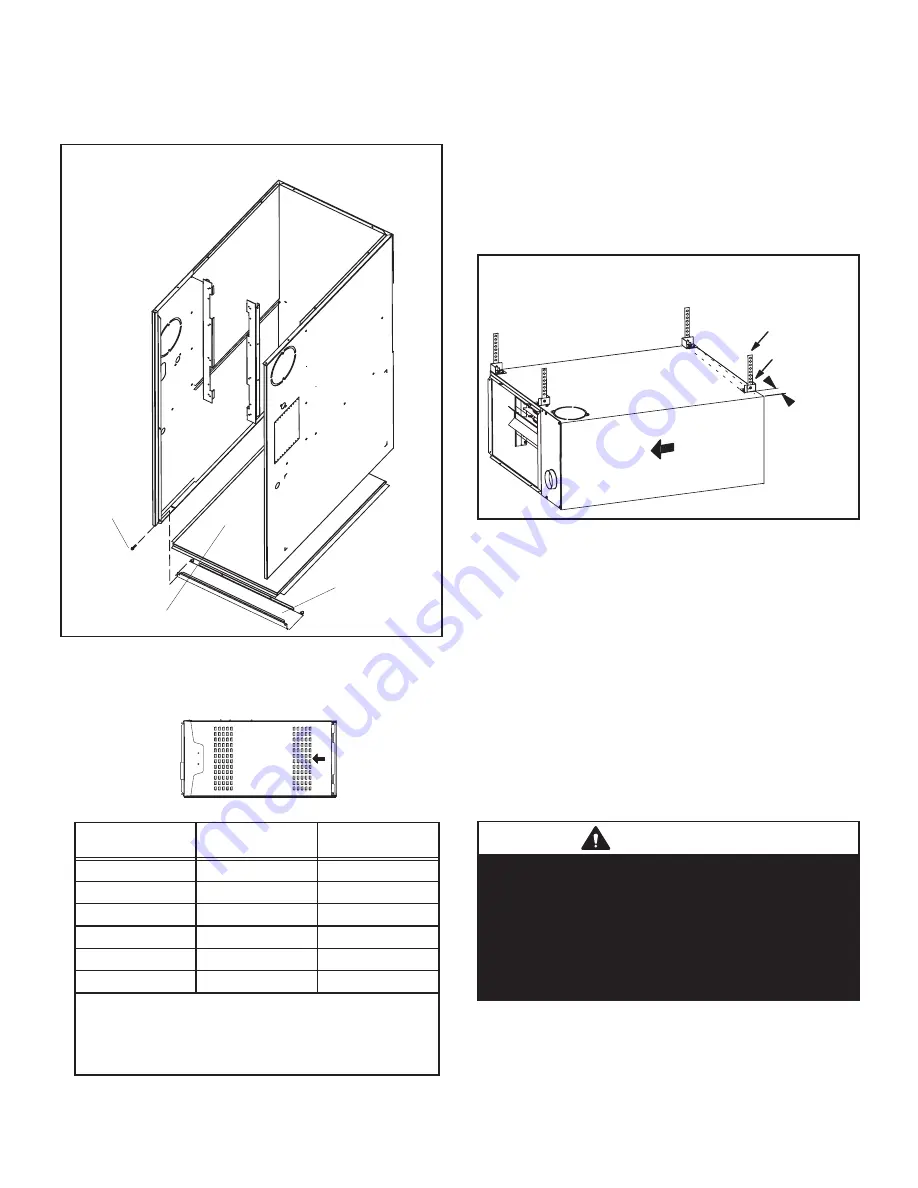
Page 11
Removing the Bottom Panel
Remove the two screws that secure the bottom cap to the
furnace. Pivot the bottom cap down to release the bottom
panel. Once the bottom panel has been removed, reinstall
the bottom cap. See figure 11.
Removing the Bottom Panel
Screw
Bottom Panel
Bottom Cap
Figure 11
Horizontal Application
Installation Clearances
Top
Bottom
Left
End
Right
End
AIR
FLOW
Vent Connector
Type
Type C
Type B1
Top
0
0
*Front
2-1/4 in. (57 mm)**
2-14 in. (57 mm)
Back
0
0
Ends
2 in. (51 mm)
2 in. (51 mm)
Vent
6 in. (152 mm)
1 in. (25 mm)
Floor
0
‡
0
‡
*Front clearance in alcove installation must be 24 in. (610 mm).
Maintain a minimum of 24 in. (610 mm) for front service access.
** 3-1/4 in. if single wall vent pipe is used.
‡
For installations on a combustible floor, do not install the furnace
directly on carpeting, tile or other combustible materials other
than wood flooring.
FIGURE 12
Horizontal Applications
The SL280UHV furnace can be installed in horizontal ap-
plications. Order kit number 51W10 (or use equivalent)
from Lennox.
Allow for clearances to combustible materials as indicated
on the unit nameplate. Minimum clearances for closet or
alcove installations are shown in figure 12.
This furnace may be installed in either an attic or a crawl-
space. Either suspend the furnace from roof rafters or
floor joists, as shown in figure 13, or install the furnace on
a platform, as shown in figure 14.
Typical Horizontal Application
Unit Suspended in Attic or Crawlspace
Bracket
Bottom Cap
Metal Strap
3/16 inch
Air Flow
FIGURE 13
.
NOTE - Heavy-gauge perforated sheet metal straps may
be used to suspend the unit from roof rafters or ceiling
joists. When straps are used to suspend the unit in this
way, support must be provided for both the ends. The
straps must not interfere with the plenum or exhaust pip-
ing installation.
Cooling coils and supply and return air
plenums must be supported separately.
NOTE - When the furnace is installed on a platform in a
crawlspace, it must be elevated enough to avoid water
damage and to allow the evaporator coil to drain.
Return Air -- Horizontal Applications
Return air must be brought in through the end of a fur-
nace installed in a horizontal application. The furnace is
equipped with a removable bottom panel to facilitate in-
stallation. See figure 11.
CAUTION
If this unit is being installed in a space serviced by an
exhaust fan, power exhaust fan, or other device which
may create a negative pressure in the space, take care
when sizing the inlet air opening. The inlet air opening
must be sized to accommodate the maximum volume
of exhausted air as well as the maximum volume of
combustion air required for all gas appliances serviced
by this space.