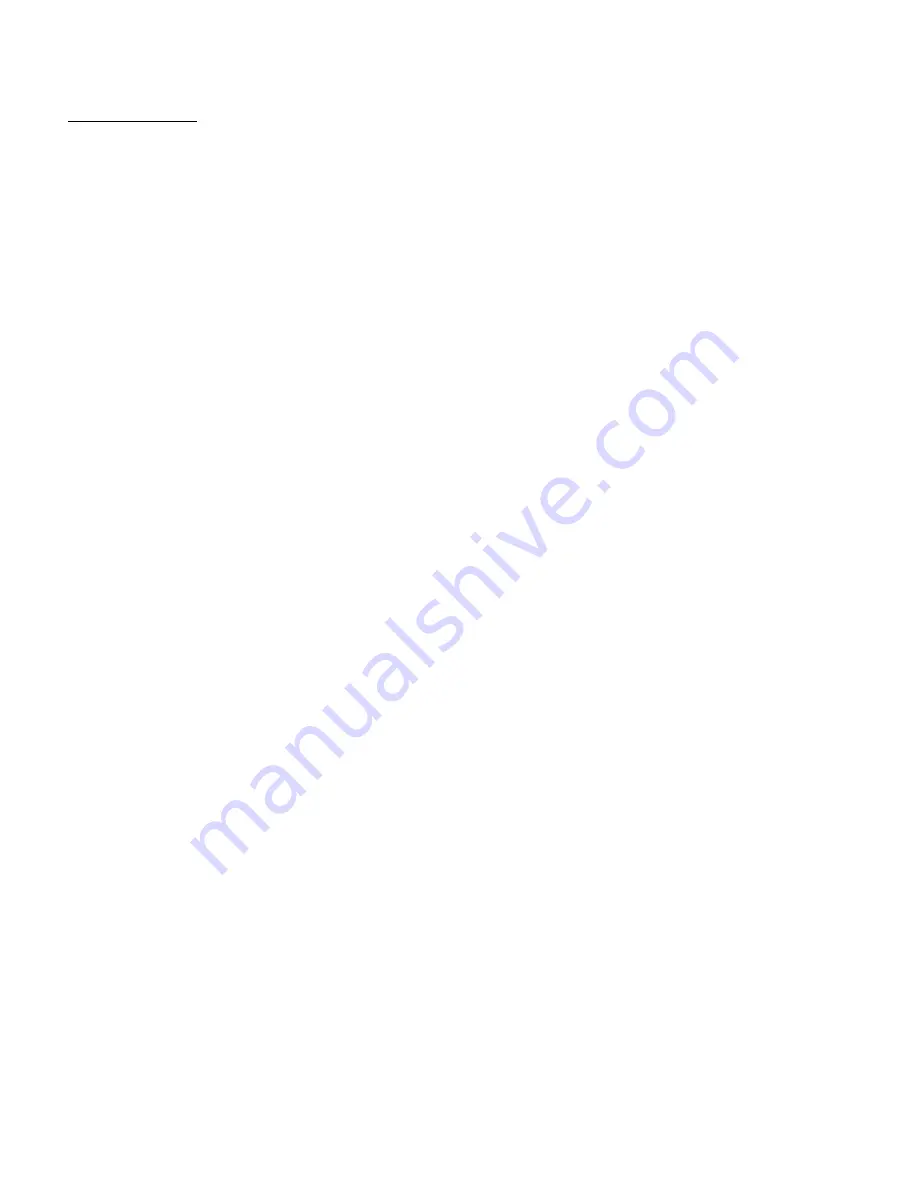
# 504,465M
Page 7
and two sets of gauges (one for use with R22 and one for
use with R410A).
Flushing Procedure
IMPORTANT:
The line set and/or indoor coil must be
flushed with at least the same amount of refrigerant that
previously charged the system. Check the charge in the
flushing cylinder before flushing the unit.
1. Remove existing R22 refrigerant using the appropriate
procedure.
If the existing outdoor unit is not equipped with shutoff
valves, or if the unit is not operational AND you plan to
use the
existing
R22 refrigerant to flush the system:
Disconnect all power to the existing outdoor unit.
Connect the existing unit, a clean recovery cylinder,
and the recovery machine according to the instruc-
tions provided with the recovery machine. Remove all
R22 refrigerant from the existing system. Refer to the
gauges after shutdown to confirm that the entire
system is completely void of refrigerant. Disconnect
the liquid and suction lines from the existing outdoor
unit.
If the existing outdoor unit is equipped with manual
shutoff valves AND you plan to use
new
R22 refriger-
ant to flush the system:
Start the existing R22 refrigerant system in cooling
mode and close the liquid line valve. Pump all the
existing R22 refrigerant back into the outdoor unit.
(It may be necessary to bypass the low pressure
switches to ensure complete refrigerant evacuation.)
When the low side system pressures reach 0 psig,
close the suction line valve. Disconnect all power to
the existing outdoor unit. Refer to the gauges after
shutdown to confirm that the valves are not allowing
refrigerant to flow back into the low side of the sys-
tem. Disconnect the liquid and vapor lines from the
existing outdoor unit.
2. Remove the existing outdoor unit. Set the new R410A
unit and follow the brazing connection procedure (see
page 5) to make line set connections.
Do not install
provided R410A check/expansion valve at this
time.
Make low voltage and line voltage connections to the
new outdoor unit.
Do not turn on power to the unit
or open the outdoor unit service valves at this
time.
3. Remove the existing refrigerant flow control orifice or
thermal expansion valve before continuing with
flushing procedures. The existing devices are not
approved for use with R410A refrigerant and may
prevent proper flushing. Use a field-provided fitting to
reconnect the lines.
4. Remove the pressure tap valve cores from the
SCU14M unit’s service valves. Connect an R22
cylinder with clean refrigerant to the suction service
valve. Connect the R22 gauge set to the liquid line
valve and connect a recovery machine with an empty
recovery tank to the gauge set.
5. Set the recovery machine for liquid recovery and start
the recovery machine. Open the gauge set valves to
allow the recovery machine to pull a vacuum on the
existing system line set and indoor coil.
6. Invert the cylinder of clean R22 and open its valve to
allow liquid refrigerant to flow into the system through
the suction line valve. Allow the refrigerant to pass
from the cylinder and through the line set and the
indoor coil before it enters the recovery machine.
7. After all of the liquid refrigerant has been recovered,
switch the recovery machine to vapor recovery so that
all of the R22 vapor is recovered. Allow the recovery
to pull a vacuum on the system.
NOTE:
A single system flush should remove all of the
mineral oil from the existing refrigerant lines and
indoor coil. A second flushing may be done (using
clean refrigerant) if insufficient amounts of mineral oil
were removed during the first flush.
Each time the
system is flushed, you must allow the recovery
machine to pull a vacuum on the system at the
end of the procedure.
8. Close the valve on the inverted R22 cylinder and the
gauge set valves. Pump the remaining refrigerant out
of the recovery machine and turn the machine off.
9. Use nitrogen to break the vacuum on the refrigerant
lines and indoor coil before removing the recovery
machine, gauges, and R22 refrigerant drum. Re-
install pressure tap valve cores into the SCU14M
service valves.
10. Install the provided expansion valve (approved for use
with R410A refrigerant) in the liquid line at the indoor
coil.
Manifold Gauge Set
Manifold gauge sets used with systems charged with
R410A refrigerant must be capable of handling the higher
system operating pressures. The gauges should be rated
for use with pressures 0 – 800 on the high side and a low
side of 30" vacuum to 250 psi with dampened speed to
500 psi. Gauge hoses must be rated for use at up to 800
psi of pressure with a 4000 psi burst rating.