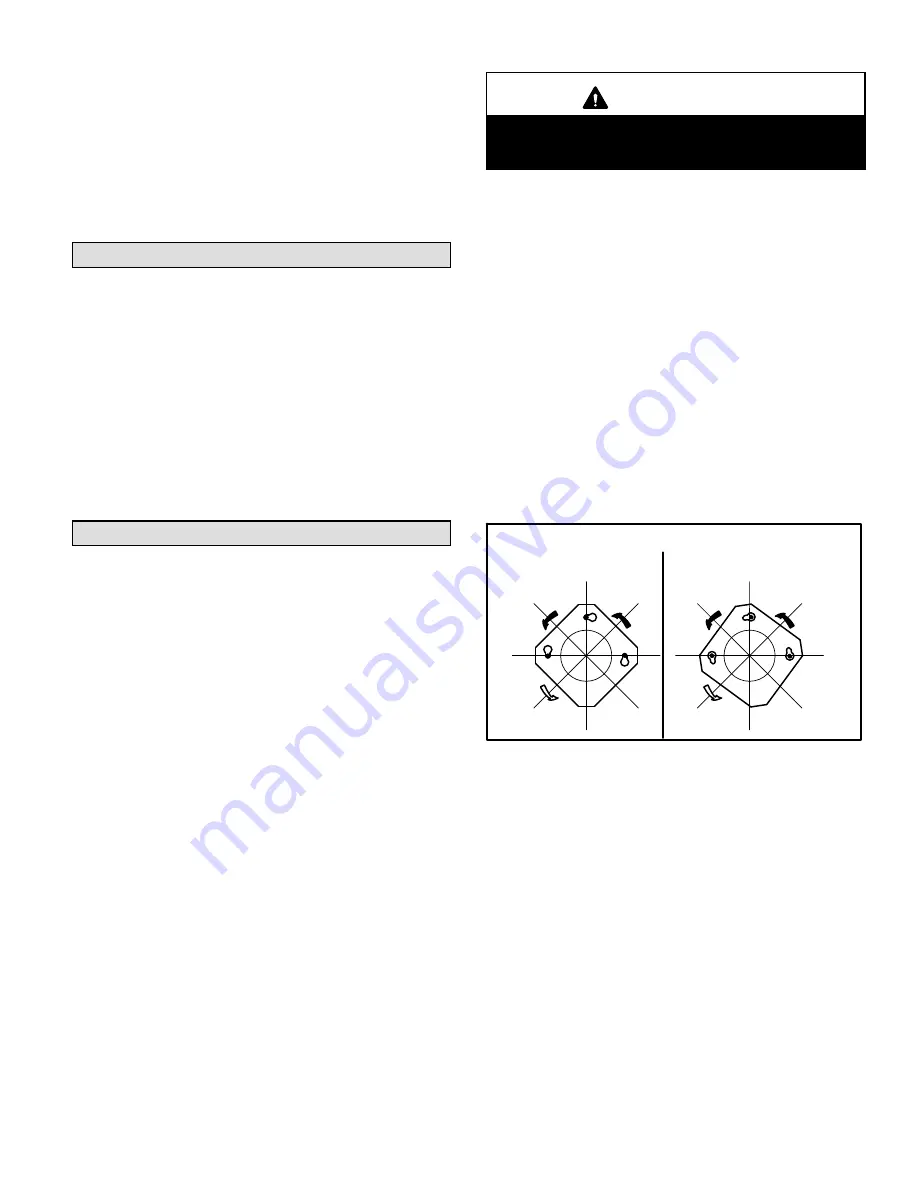
Page 5
When furnace is used in conjunction with cooling units, it
shall be installed in parallel with, or on the upstream side of,
cooling units to avoid condensation in the heating element.
With a parallel flow arrangement, a damper (or other
means to control the flow of air) shall be adequate to pre-
vent chilled air from entering the furnace and, if manually
operated, must be equipped with means to prevent opera-
tion of either unit, unless damper is in the full heat" or cool"
position.
Locate & Level the Unit
1 − Set the unit in desired location keeping in mind the
clearances listed in table 2. Also keep in mind oil sup-
ply connections, electrical supply, flue connections
and sufficient clearance for installing and servicing
unit.
2 − Level the unit from side to side and from front to rear. If
the furnace is not level, place fireproof wedges or
shims between the low side of the furnace and the
floor. Make sure the weight of the furnace is distributed
evenly on all four corners. Strain on sides of cabinet
causing cracking and popping noises may occur if
weight of furnace is not evenly distributed.
Unit Adjustments
Neither the nozzle setting nor the air adjustments are facto-
ry set. The furnace is fire tested and the limit control is
checked to make sure it functions properly; no factory set-
tings are made. During installation, the furnace must be
set up." The installing dealer/contractor must have and
use proper test equipment in order to correctly set up the oil
furnace. Proper testing equipment is required to ensure
correct operation of the unit. The use of test equipment is
now more critical than ever due to tighter tolerances need-
ed to keep the furnace operating efficiently.
Among the test equipment for an oil furnace, the proper
combustion test kit should contain the following:
D
Draft gauge
D
CO
2
or O
2
analyzer
D
Smoke tester
D
Pressure gauge
D
High temperature thermometer
D
Beckett T−500 gauge
D
Oil vacuum gauge
D
Knowledge of proper test equipment operation
CAUTION
Improper nozzle and/or air adjustment of this unit
may result in sooting problems. Refer to the follow-
ing section for correct adjustment procedures.
Adjusting the Nozzle
Proper adjustment of the nozzle assembly is critical be-
cause alignment may have changed during shipping. Be-
fore the furnace and oil lines are installed, the nozzle as-
sembly must be checked. To check the nozzle assembly,
remove the entire burner assembly (not just the nozzle)
from the furnace. The lower firing nozzle is factory
installed. This should be verified by the installer. Inspect
the spark transformer leads also to ensure they are still at-
tached to the electrodes.
The burner assembly is attached to the vestibule panel by
three nuts. Slots are provided in the mounting flange for re-
moving the burner assembly from the vestibule. By loosen-
ing the nuts and by turning the whole burner assembly
counterclockwise (figure 3), the entire burner assembly will
come out of the furnace. There is adequate wire to remove
the burner without disconnecting wires. Once removed,
turn the burner around in the vest panel area.
Figure 3
O23 Series Burner Removal
Loosen three nuts which at-
tach burner to vest panel.
Rotate burner counterclockwise on
slots then pull toward you.
To correctly adjust the nozzle, use a Beckett #T−500 gauge
Insert the small end of the gauge into the end of the cone
and measure from the flat of the end cone to the tip of the
nozzle. When nozzle depth is correct, the tip of the nozzle
should just touch the end of the gauge. Refer to the illustra-
tion sheet provided with the gauge. Note that the scale side
of the gauge is not used for this purpose. Make corrections
by sliding the nozzle assembly forward or backward within
the blast tube (figure 4). At the same time, check the nozzle
alignment.