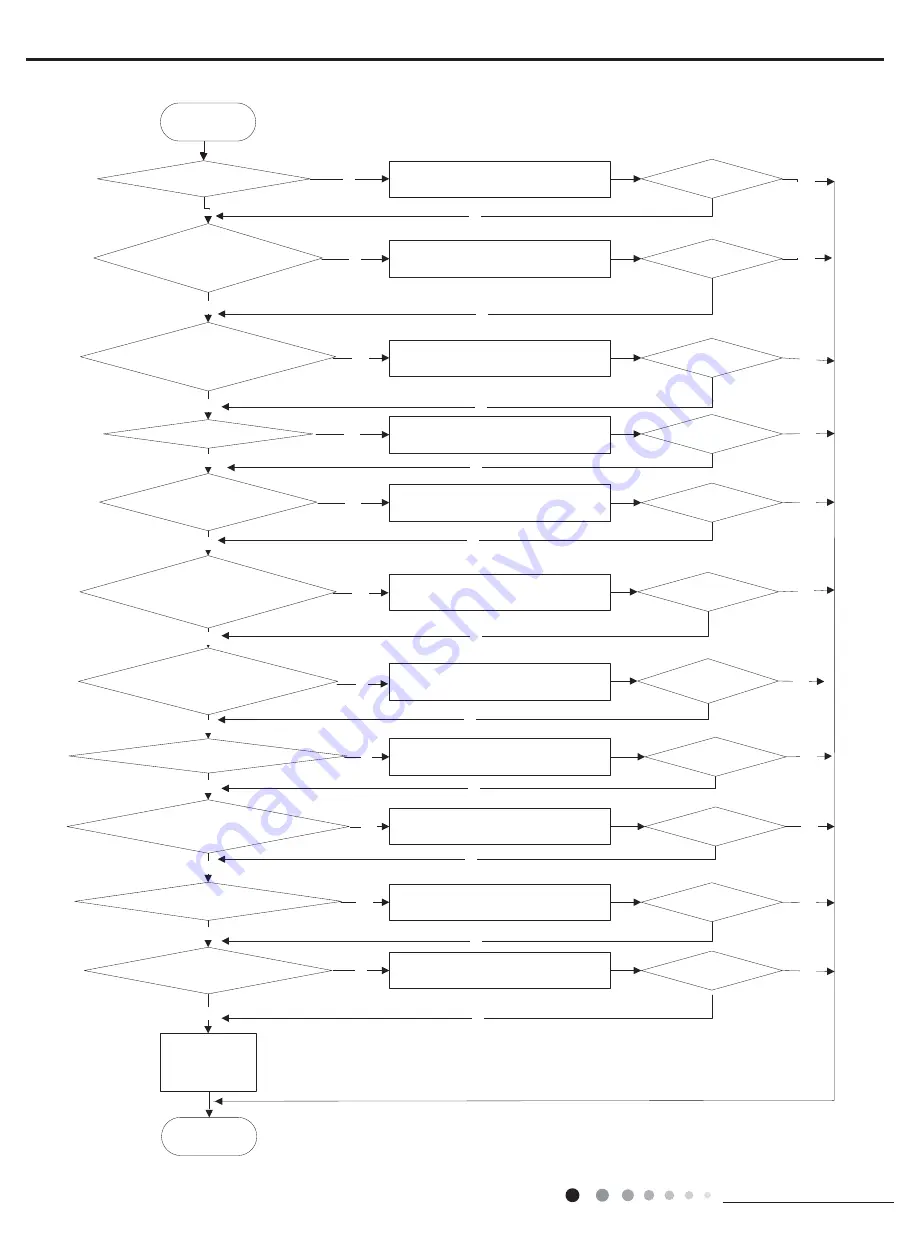
34
Installation and Maintenance
Service Manual
9.2.2 E1 Malfunction
Start
Are the display panel and main board
connected tightly?
Are the HPP terminal
well with the high pressure switch on the
complete unit?
Is the wiring of high pressure
or poorly contacted?
Connect the display panel with the main board well
Is the refrigerant superabundant?
Is there poor heat
exchanger and bad radiating
environment );
Is the supply voltage normal?
be caused by overcurrent protection
due to this)
Are the air
intake and air discharge at indoor / outdoor heat
exchanger smooth?
Is there filth blockage on the filter or on the
heat exchanger fins of indoor / outdoor unit?
Is there blockage inside the pipeline of the system
Are the gas valve and liquid valve for
outdoor unit opened completely?
yes
yes
no
no
no
no
yes
yes
no
no
Replace the controller
yes
End
no
Malfunction is eliminated.
no
Connect the
HPP
terminal on the main board with
the high pressure switch on the complete unit well
no
Malfunction is eliminated.
no
If the wire of high pressure switch is loosened, please
connect the wires according to the circuit diagram.
If the high pressure switch is broken or poorly contacted,
please replace it.
yes
Malfunction is eliminated.
no
Adjust the volume of refrigerant according to the
requirement of the system
yes
Malfunction is eliminated.
no
Adjust the unit to improve the heat exchange of unit
yes
Malfunction is eliminated.
no
Decrease the ambient temperature
yes
Malfunction is eliminated.
no
The normal voltage is lower than 90% of the rated
no
Malfunction is eliminated.
Adjust the system to make the air intake and air
discharge of indoor and outdoor heat exchangers
smooth
no
Malfunction is eliminated.
no
Remove the blockage.
Malfunction is eliminated.
Remove the blockage inside the pipeline of the system
yes
Malfunction is removed.
Open the outdoor gas valve and liquid valve completely
no
Malfunction is eliminated.
no
yes
yes
yes
yes
yes
yes
yes
yes
yes
yes
yes
no
no
no
no
Is the ambient temperature
on the main board connected
voltage on the nameplate
(If it is a 3-phase unit, high pressure protection may
too high?(If it is a 3-phase unit, high pressure
protection may be caused by overcurrent
protection due to this)
exchange? (Including filth blockage of heat
switch loosened? Is the high pressure switch broken