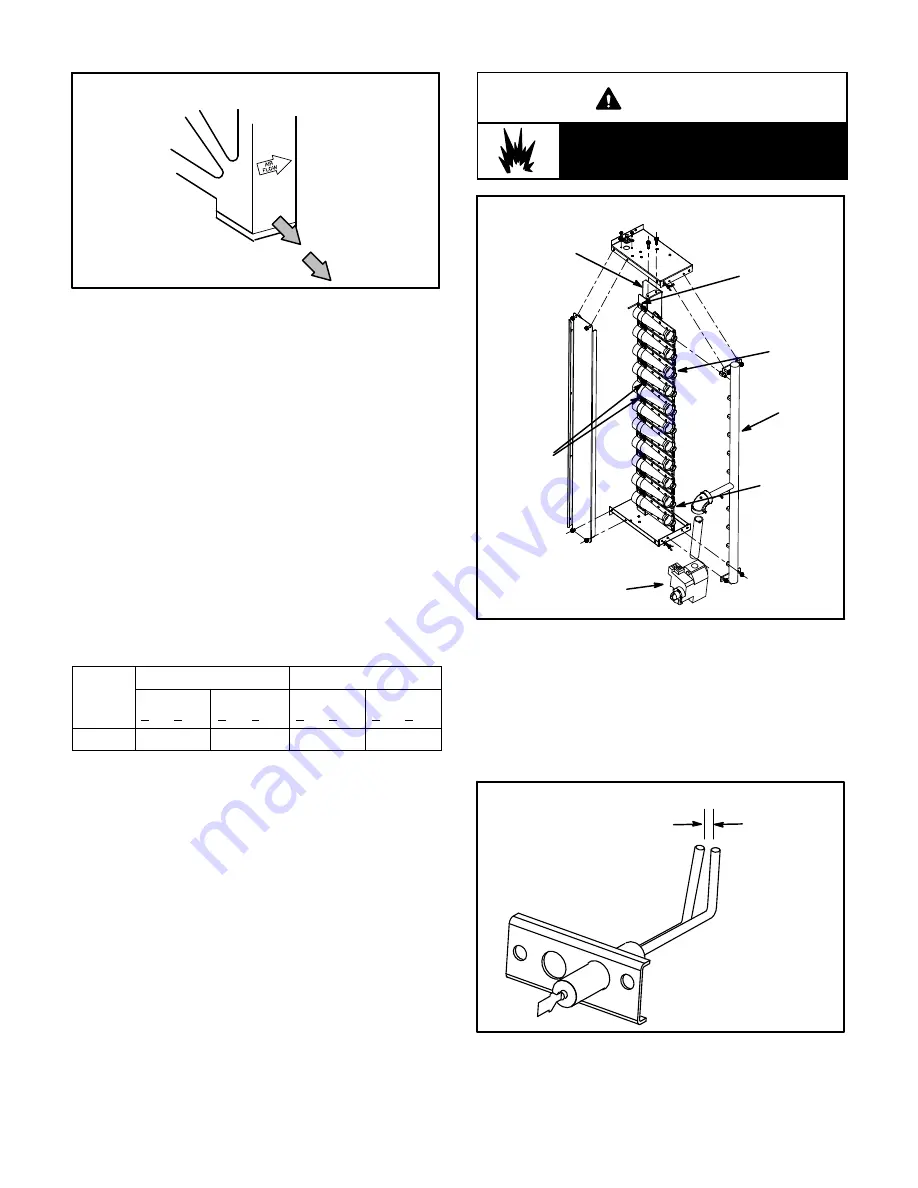
Page 5
REMOVE FILTERS
FIGURE 4
Lubrication
All motors are lubricated at the factory. No further
lubrication is required.
Blower shaft bearings are prelubricated. For extended
bearing life, relubricate at least once every two years
with a lithium base grease, such as Alvania 3 (Shell Oil),
Chevron BRB2 (Standard Oil) or Regal AFB2 (Texas
Oil). Use a hand grease gun for relubrication. Add only
enough grease to purge through the bearings so that a
bead of grease appears at the seal lip contacts.
Manifold Pressures
Manifold pressures are shown in table 1. Refer to figures
1 and 2 to locate pressure ports.
TABLE 1
MANIFOLD PRESSURES
in.wg. (kPa)
Unit
Natural Gas
Propane (LP) Gas
1st Stage
+ 0.2(+.05)
2nd Stage
+ 0.3(+.08)
1st Stage
+ 0.2(+.05)
2nd Stage
+ 0.3(+.08)
420-600
1.6 (0.40)
3.7 (0.92)
5.5 (1.37)
10.5(2.61)
See Optional Modulating Gas Valve (MGV) section on
units equipped with MGVs.
Burners
1- Periodically examine burner flames for proper
appearance during the heating season.
2- Inspect the position of the flame sensor. Sensor
should be centered in the path of the flame.
3- Before each heating season examine the burners for
any deposits or blockage which may have occurred.
Clean burners as follows.
4- Turn off the electrical power and gas supply to the unit
and open heat section access panel.
5- Remove and retain two screws securing burners to
the burner support. See figure 5. Clean as necessary.
Replace burners and secure with retained screws.
WARNING
Danger of explosion. Can cause injury or
death. Do not overtighten main burner
mounting screws. Snug tighten only.
BURNER BOX ASSEMBLY
FIGURE 5
GAS
MANIFOLD
FLAME
SENSOR
GAS
VALVE
BURNERS
REMOVE
SCREWS
TO CLEAN
BURNERS
BURNER
SUPPORT
IGNITOR
6- Remove and retain the two screws securing the
ignitor to the burner support. Remove the burner and
check the spark gap with appropriately sized twist
drills or feeler gauges. See figure 6.
7- Replace the ignitor and secure in place with retained
screws.
FIGURE 6
IGNITOR
SPARK GAP
SHOULD BE 1/8”
(3mm)
8- Restore electrical power and gas supply. Follow
lighting instructions attached to unit and use
inspection port in access panel to check flame.