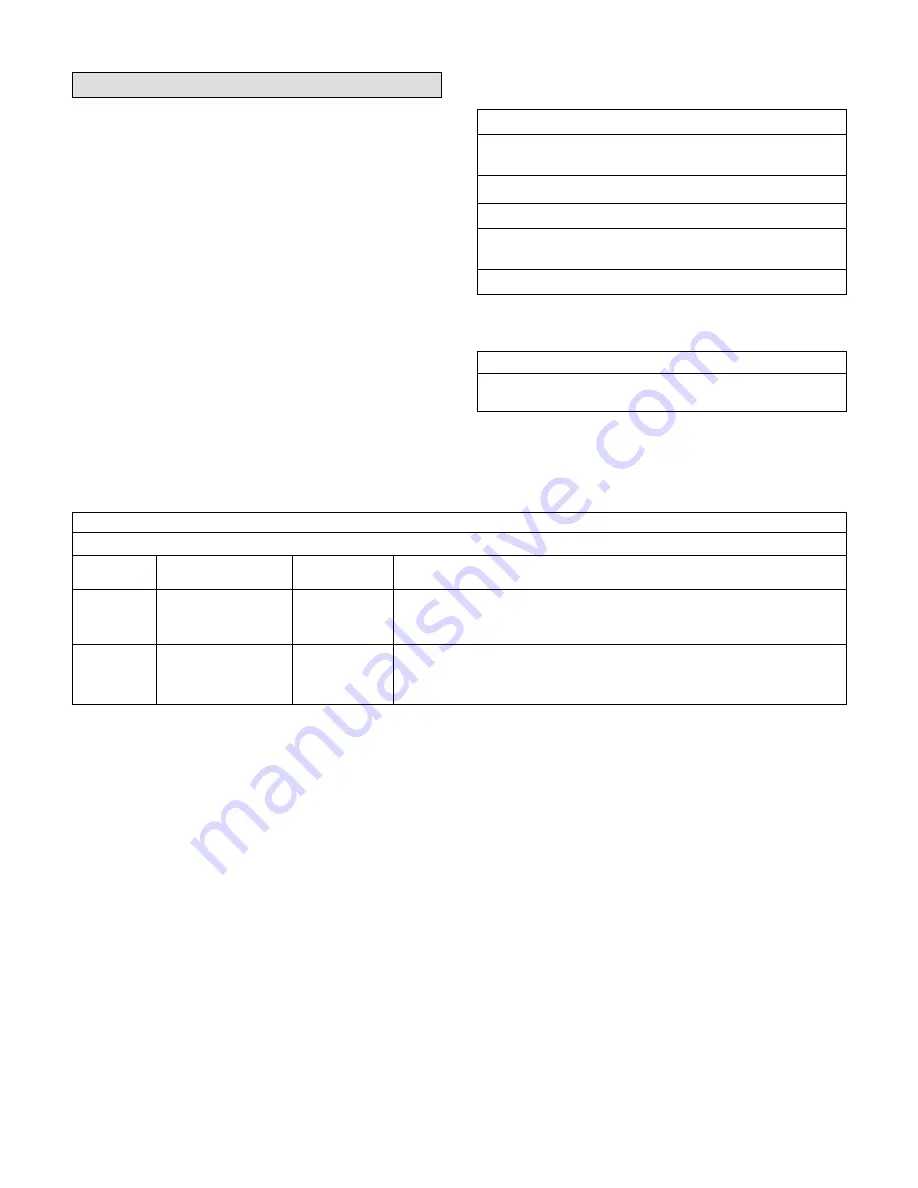
Page 49
LGT/LCT036, 048, 060, 072
Factory Unit Controller Settings
Use the mobile service app to adjust parameters; menu
paths are shown in each table. Refer to the Unit Controller
manual provided with each unit.
Tables 16 through18 show factory settings (in degrees, %
of fan CFM, etc.). Record adjusted settings on the label
located inside the compressor access panel.
When field installing optional kits and accessories, the
Unit Controller must be configured to identify the option
before it will function. Refer to figures 36 and 37 to
determine whether the Unit Controller configuration I.D.
must change. To configure the option, use MAIN MENU >
SETUP > INSTALL menu path. Press SAVE until
CONFIGURATION ID 1 or 2 appears depending on the
option installed. Change the appropriate character in the
configuration I.D. For example, when an economizer is
installed using a single enthalpy sensor, change
configuration I.D. 1, the second character, to “S”.
TABLE 16
581038
Units With BACnet Settings
RTU Menu > Network Integration > Network Setup Wizard >
BACnet MS/TP > See BACnet MAC Address
BACNET MAC ADDRESS:
Units With Room Sensor, CPC/LSE Gateway Settings
RTU Menu > Network Integration > Network Setup Wizard >
SBUS > Set SBUS Address
LCONN ADDRESS:
TABLE 17
581037-01
Units With LonTalk Settings
Use menu RTU Menu > Network Integration > Network Setup
Wizard > Set “LONTALK”
TABLE 18
581101
Units With Hot Gas Reheat
Use SETTINGS > RTU OPTIONS > EDIT PARAMETERS
Parameter
Factory
Setting
Field Setting
Description
105
6
Hot Gas Reheat Option 6: Reheat is only possible if blower is energized
during occupied periods. Controlled by RH sensor (A91) connected to
input A55_P298_5 and set point set at parameter 106 (default 60%).
414
10 sec (All-Aluminum
Coils Only)
HI CL REHEAT TMOUT:
Number of seconds Reheat Valve remains
energized upon thermostat call for high stage cooling (default 0 sec
onds).