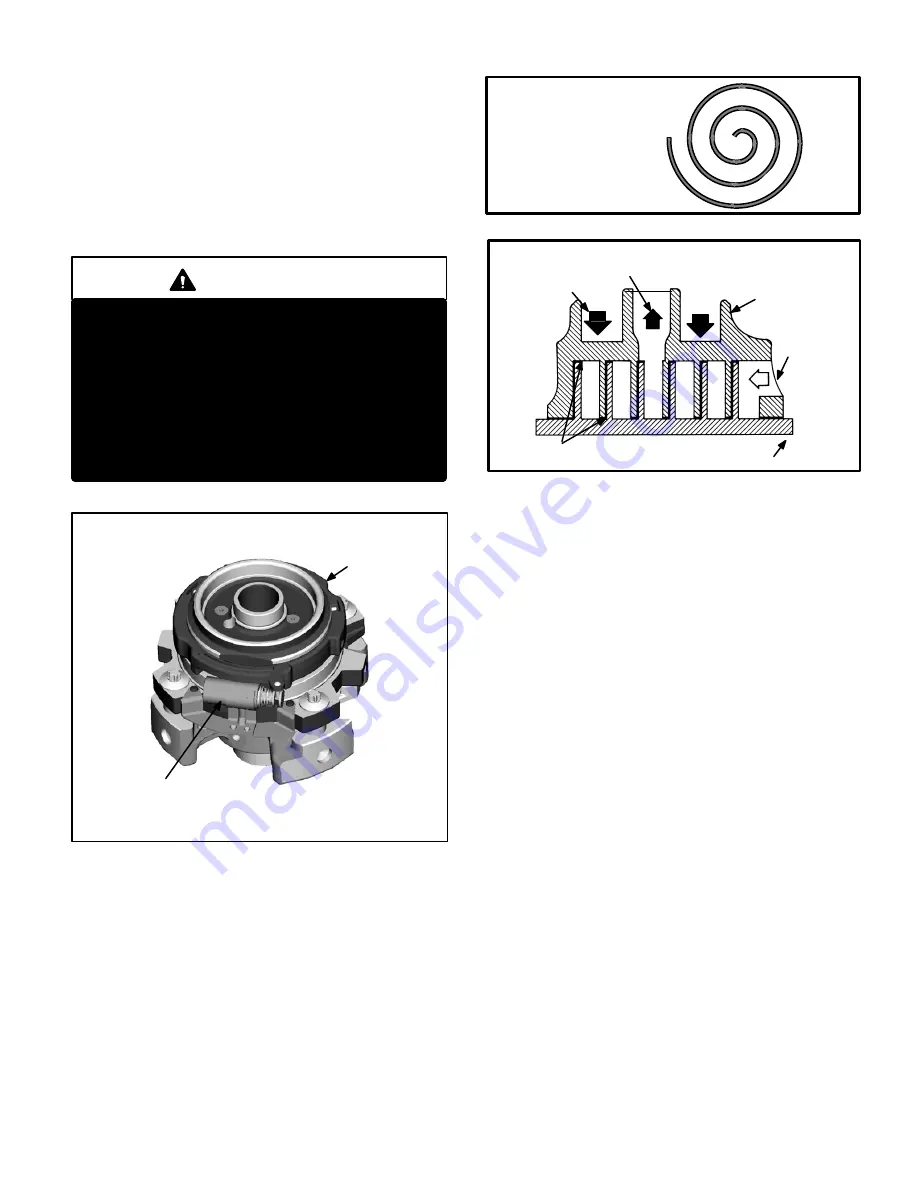
Page 3
I−APPLICATION
All major components (indoor blower and coil) must be
matched according to Lennox recommendations for the
compressor to be covered under warranty. Refer to the En-
gineering Handbook for approved system matchups. A
misapplied system will cause erratic operation and can re-
sult in early compressor failure.
II−Unit Components
ELECTROSTATIC DISCHARGE (ESD)
Precautions and Procedures
CAUTION
Electrostatic discharge can affect electronic
components. Take precautions during unit instal-
lation and service to protect the unit’s electronic
controls. Precautions will help to avoid control
exposure to electrostatic discharge by putting
the unit, the control and the technician at the
same electrostatic potential. Neutralize electro-
static charge by touching hand and all tools on an
unpainted unit surface before performing any
service procedure.
A−Two−Stage Scroll Compressor (B1)
FIGURE 1
TWO−STAGE MODULATED SCROLL
solenoid actuator coil
slider ring
The scroll compressor design is simple, efficient and re-
quires few moving parts. A cutaway diagram of the scroll
compressor is shown in figure 1.The scrolls are located in
the top of the compressor can and the motor is located just
below. The oil level is immediately below the motor.
The scroll is a simple compression concept centered
around the unique spiral shape of the scroll and its inherent
properties. Figure 2 shows the basic scroll form. Two iden-
tical scrolls are mated together forming concentric spiral
shapes (figure 3). One scroll remains stationary, while the
other is allowed to orbit" (figure 4). Note that the orbiting
scroll does not rotate or turn but merely orbits" the station-
ary scroll.
FIGURE 2
SCROLL FORM
FIGURE 3
STATIONARY
SCROLL
ORBITING SCROLL
DISCHARGE
SUCTION
CROSS−SECTION OF SCROLLS
TIPS SEALED BY
DISCHARGE PRESSURE
DISCHARGE
PRESSURE
The counterclockwise orbiting scroll draws gas into the out-
er crescent shaped gas pocket created by the two scrolls
(figure 4 − 1). The centrifugal action of the orbiting scroll
seals off the flanks of the scrolls (figure 4 − 2). As the orbiting
motion continues, the gas is forced toward the center of the
scroll and the gas pocket becomes compressed (figure 4
−3). When the compressed gas reaches the center, it is dis-
charged vertically into a chamber and discharge port in the
top of the compressor (figure1). The discharge pressure
forcing down on the top scroll helps seal off the upper and
lower edges (tips) of the scrolls (figure 3). During a single or-
bit, several pockets of gas are compressed simultaneously
providing smooth continuous compression.
The scroll compressor is tolerant to the effects of liquid re-
turn. If liquid enters the scrolls, the orbiting scroll is allowed
to separate from the stationary scroll. The liquid is worked
toward the center of the scroll and is discharged.
Due to its efficiency, the scroll compressor is capable of
drawing a much deeper vacuum than reciprocating com-
pressors. Deep vacuum operation can cause internal fusite
arcing resulting in damaged internal parts and will result in
compressor failure. This type of damage can be detected
and will result in denial of warranty claims. The scroll com-
pressor can be used to pump down refrigerant as long as
the pressure is not reduced below 7 psig.
NOTE − During operation, the head of a scroll compressor
may be hot since it is in constant contact with discharge
gas.
The scroll compressors in all HPXA16 model units are de-
signed for use with R−410A refrigerant and operation at
high pressures. Compressors are shipped from the factory
with 3MA (32MMMA) P.O.E. oil. If oil must be added for ser-
vice, Copeland has approved Mobile EAL
Arctic 22CC