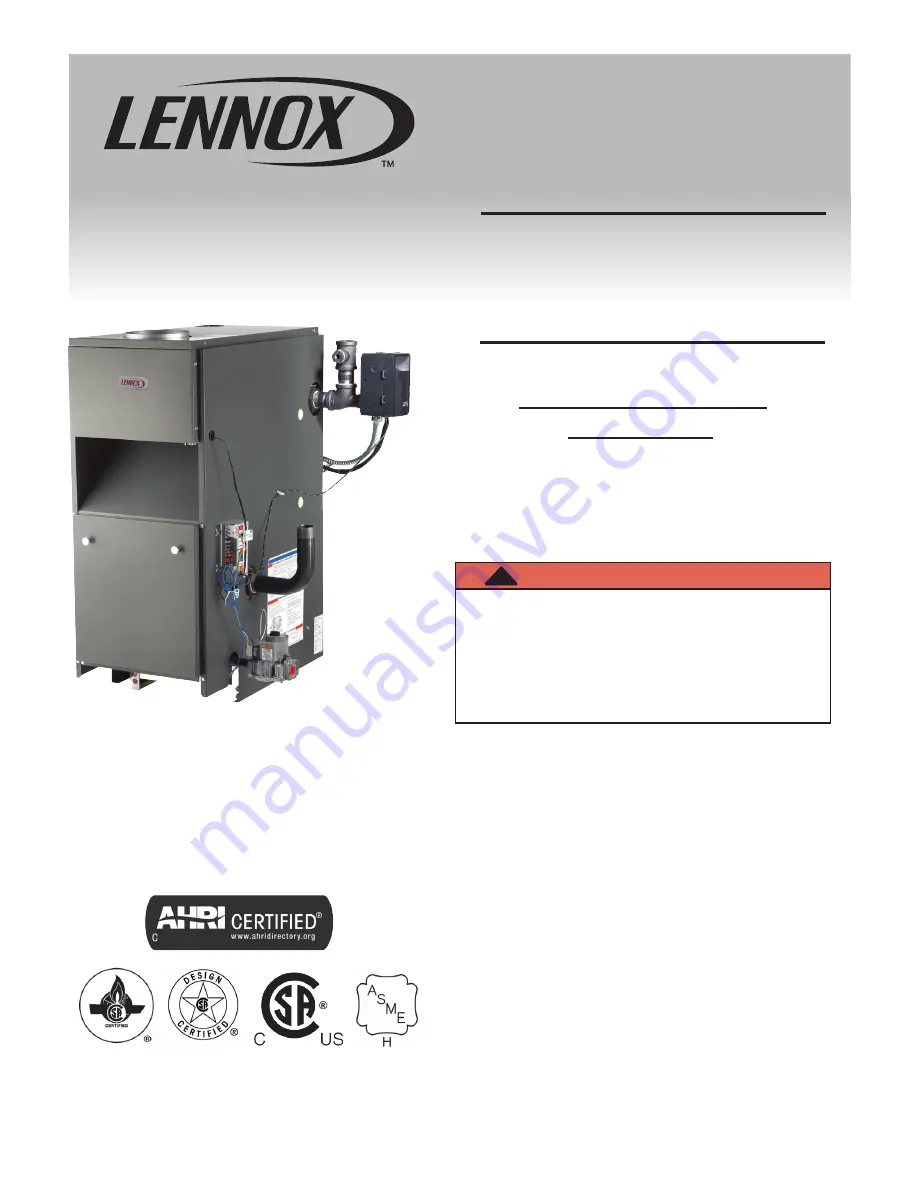
PN 240013089, Rev. A [09/30/2020]
GAS FIRED BOILER
INSTALLATION
INSTRUCTIONS
PRODUCT LITERATURE
Lennox Industries Inc.
Dallas, Texas
This boiler cannot be used with all types of
chimneys. Read these instructions carefully
before installing.
GAS-FIRED HOT WATER BOILERS
These Gas-Fired Water boilers are low pressure,
sectional cast iron boilers Design Certified by CSA
(Canadian Standards Association) for use with
Natural and Propane Gases. They are constructed
and hydrostatically tested for maximum working
pressure of 50 psi (pounds per square inch) in
accordance with A.S.M.E. (American Society of
Mechanical Engineers) Boiler and Pressure Vessel
Code Section IV Standards for Cast Iron Heating
Boilers.
Tested for 50 psi. ASME
Working Pressure
C.S.A. Certified for
Natural gas or Propane
GWB84-262E
GWB84-299E
Retain These Instructions for
Future Reference
These instructions must be affixed on or
adjacent to the boiler.
WARNING
Improper installation, adjustment, alteration,
service, or maintenance can cause injury or
property damage. Refer to this manual. For
assistance or additional information consult
a qualified installer, service agency, or the
gas supplier.
!