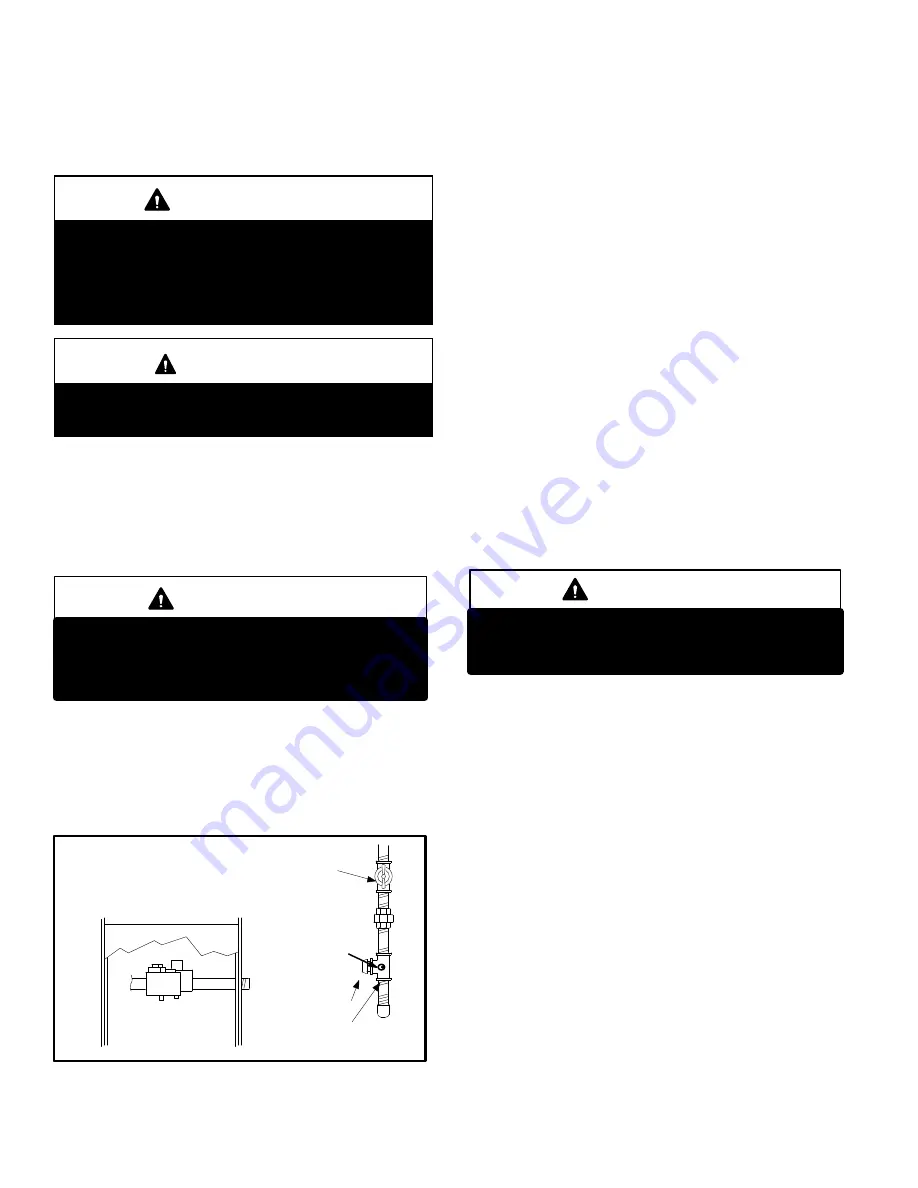
Page 16
IV-HEATING SYSTEM SERVICE CHECKS
A-CSA Certification
All units are CSA design certified without modifications.
Refer to the EL280DF Installation Instruction.
B-Gas Piping
CAUTION
If a flexible gas connector is required or allowed by
the authority that has jurisdiction, black iron pipe
shall be installed at the gas valve and extend outside
the furnace cabinet. The flexible connector can then
be added between the black iron pipe and the gas
supply line.
WARNING
Do not over torque (800 in-lbs) or under torque (350
in-lbs) when attaching the gas piping to the gas
valve.
Gas supply piping should not allow more than 0.5”W.C. drop
in pressure between gas meter and unit. Supply gas pipe
must not be smaller than unit gas connection.
Compounds used on gas piping threaded joints should be
resistant to action of liquefied petroleum gases.
C-Testing Gas Piping
IMPORTANT
In case emergency shutdown is required, turn off
the main shut‐off valve and disconnect the main
power to unit. These controls should be properly
labeled by the installer.
When pressure testing gas lines, the gas valve must be dis
connected and isolated. Gas valves can be damaged if
subjected to more than 0.5 psig (14” W.C.). See figure 12
.
If
the pressure is equal to or less than 0.5psig (14”W.C.), use
the manual shut-off valve before pressure testing to isolate
furnace from gas supply.
FIGURE 12
MANUAL MAIN SHUT-OFF VALVE
WILL NOT HOLD TEST PRESSURE
IN EXCESS OF 0.5 PSIG (14”W.C.)
GAS VALVE
CAP
GAS PIPING TEST PROCEDURE
FIELD PROVIDED
LINE PRESSURE TAP
1/8 NPT PLUG
When checking piping connections for gas leaks, use pre
ferred means. Kitchen detergents can cause harmful corro
sion on various metals used in gas piping. Use of a specialty
Gas Leak Detector is strongly recommended. It is available
through Lennox under part number 31B2001. See Corp.
8411-L10, for further details.
Do not use matches, candles, flame or any other source of
ignition to check for gas leaks.
D-Testing Gas Supply Pressure
An inlet post located on the gas valve provides access to
the supply pressure. See figure 11. Back out the 3/32 hex
screw one turn, connect a piece of 5/16 tubing and connect
to a manometer to measure supply pressure. See table 10
for supply line pressure.
E-Check Manifold Pressure
After line pressure has been checked and adjusted, check
manifold pressure. Move pressure gauge to outlet pres
sure tap located on unit gas valve (GV1). Checks of man
ifold pressure are made as verification of proper regulator ad
justment. Manifold pressure can be measured at any time the
gas valve is open and is supplying gas to the unit. See table
10 for normal operating manifold pressure.
IMPORTANT
For safety, connect a shut‐off valve between the
manometer and the gas tap to permit shut off of
gas pressure to the manometer.
The gas valve is factory set and should not require adjust
ment. All gas valves are factory regulated.
Manifold Adjustment Procedure:
1 - Connect test gauge to manifold pressure tap (figure
11) on gas valve.
2 - Ignite unit on
low fire
and let run for 5 minutes to allow
3 - After allowing unit to stabilize for 5 minutes, record
manifold pressure and compare to value given in table
10.
4 - If necessary, make adjustments. Figure 11 shows
location of high fire and low fire adjustment screw.
5 - Repeat steps 2, 3 and 4 on high fire.
6 - Shut unit off and remove manometer as soon as an ac
curate reading has been obtained. Take care to re
place pressure tap plug
.
7 - Start unit and perform leak check. Seal leaks if found.