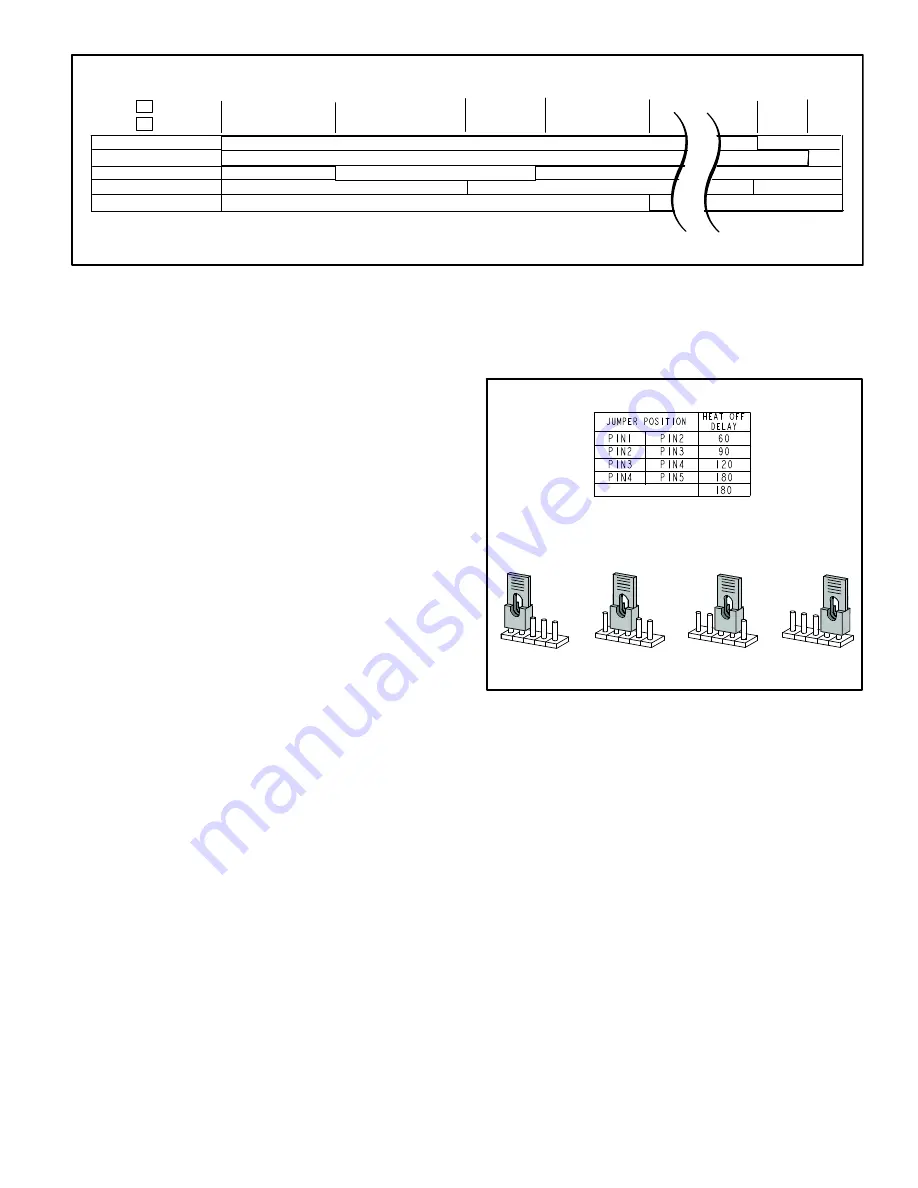
Page 9
ÉÉÉÉÉÉÉÉÉÉÉÉÉÉÉÉÉÉÉÉÉÉÉÉ
ÉÉÉÉÉÉÉÉÉÉÉÉÉÉÉÉÉÉÉÉÉÉÉÉ
ÉÉÉÉÉÉÉÉÉÉÉÉÉ
ÉÉÉÉÉÉÉÉÉÉÉÉÉ
ÉÉ
DEMAND
CAI
GAS VALVE
15
ON
OFF
ÉÉÉÉÉÉÉÉÉÉÉÉÉÉÉÉÉÉÉÉÉÉÉÉÉÉÉ
ÉÉÉÉÉÉÉÉÉÉÉÉÉÉÉÉÉÉÉÉÉÉÉÉÉÉÉ
ÉÉ
38
ÉÉÉÉÉÉÉÉÉÉ
IGNITOR
34
1
Pre -Purge
Ignitor Warm-up
Trial for
Ignition
Post
Purge
5 SEC
80
*Blower on time will be 30 seconds after flame is sensed. Blower off time will depend on “OFF TIME” Setting.
INDOOR BLOWER
ÉÉÉÉÉÉÉÉÉ
ÉÉÉÉÉÉÉÉÉ
Blower “On”*
Delay
ELECTRONIC IGNITION
FIGURE 4
Fan Time Control
Heating Fan On Time
The fan on time of 30 seconds is not adjustable.
Heating Fan Off Time
Fan off time (time that the blower operates after the heat
demand has been satisfied) can be adjusted by moving the
jumper to a different setting. The unit is shipped with a fac
tory fan off setting of 90 seconds. For customized comfort,
monitor the supply air temperature once the heat demand
is satisfied. Note the supply air temperature at the instant
the blower is de-energized.
Adjust the fan-off delay to achieve a supply air temperature
between 90° - 110° at the instant the blower is de-ener
gized. (Longer delay times allow for lower air temperature,
shorter delay times allow for higher air temperature). See
Cooling Fan On Time
The fan on time is 2 seconds and is not adjustable.
Cooling Fan Off Time
The control has a 45 second fan off delay after cooling de
mand has been met. This delay is factory set and not ad
justable.
HEAT FAN‐OFF TIME IN SECONDS
To adjust fan-off timing, reposition jumper across pins to
achieve desired setting.
NO JUMPER
FIGURE 5
60
90
120
180
60
90
120
180
60
90
120
180
60
90
120
180
60 Second
off Time
90 Second
off Time
120 Second
off Time
180 Second
off Time