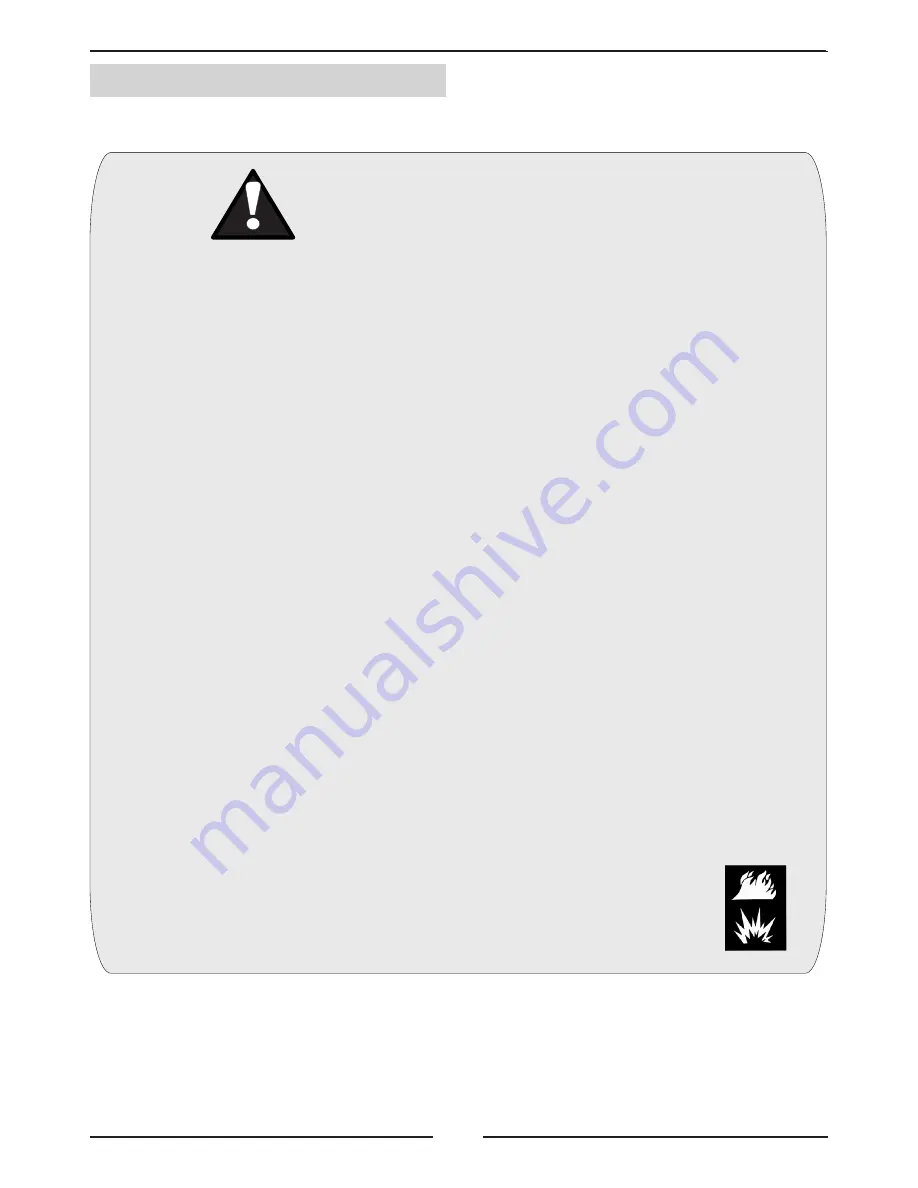
27
3.- COMMISSIONING AND OPERATION
3.2.- PRELIMINARY CHECKS AT STARTUP
The unit must be installed in accordance with local safety codes
andregulations and can only be used in a well ventilated area.
Please readcarefully the manufacturer’s instructions before star-
ting this unit
All work on the unit must be carried out by a qualified and
authorised employee.
Non-compliance with the following instructions may result in in-
jury or serious accidents.
Work on the unit:
The unit shall be isolated from the electrical supply by discon-
nection and locking using the main isolating switch. Workers
shall wear the appropriate personal protective equipment (hel-
met, gloves, glasses,etc.).
Electrical system:
Electrical connections can become loose during transport. Plea-
se check them before starting-up the unit Compressors with
specific rotation direction. Check the correct rotation direction
of the fan before closing the compressor circuit breakers. If the
direction is incorrect, the phases must be reversed at the head
of the main switch. Work on electric components shall be perfor-
med with the power off (see below) by employees having valid
electrical qualification and authorisation.
Refrigerating circuit(s):
After more than 12 hours of power cut, the cranckcase heater
(compressor) should be powered for 5 hours before any return
to service. Non-compliance with this instruction can cause dete-
rioration of the compressors.
Monitoring of the pressures, draining and filling of the system
under pressure shall be carried out using connections provided
for this purpose and suitable equipment.
To prevent the risk of explosion due to spraying of coolant and
oil,
the relevant circuit shall be drained and at zero pres
-
sure
before any disassembly or unbrazing of the refrigerating
parts takes place.
There is a residual risk of pressure build-up by degassing the
oil or by heating the exchangers after the circuit has been
drained.
Zero pressure shall be maintained
by venting the
drain connection to the atmosphere on the low pressure side.
The brazing shall be carried out by a qualified brazier. The
brazing shall comply according to code ASME section IX follo-
wing the procedures specific.
Before starting up:
-Test the circuit to the maximum working pressure(see the na-
meplate)
-Verifify the operation of the high pressure swich.
-Check the piping and the components of the refrigerant cir-
cuit.
Replacing components:
In order to maintain CE marking compliance, replacement of
components shall be carried out
using spare parts, or using parts approved by Lennox.
Only the coolant shown on the manufacturer’s nameplate
shall be used, to the exclusion of all other
products (mix of coolants, hydrocarbons, etc.).
CAUTION:
In the event of fire, refrigerating
circuits can cause an explosion
and spray coolant gas and oil.
Summary of Contents for COMPACTAIR CDC
Page 31: ...30 NOTES...