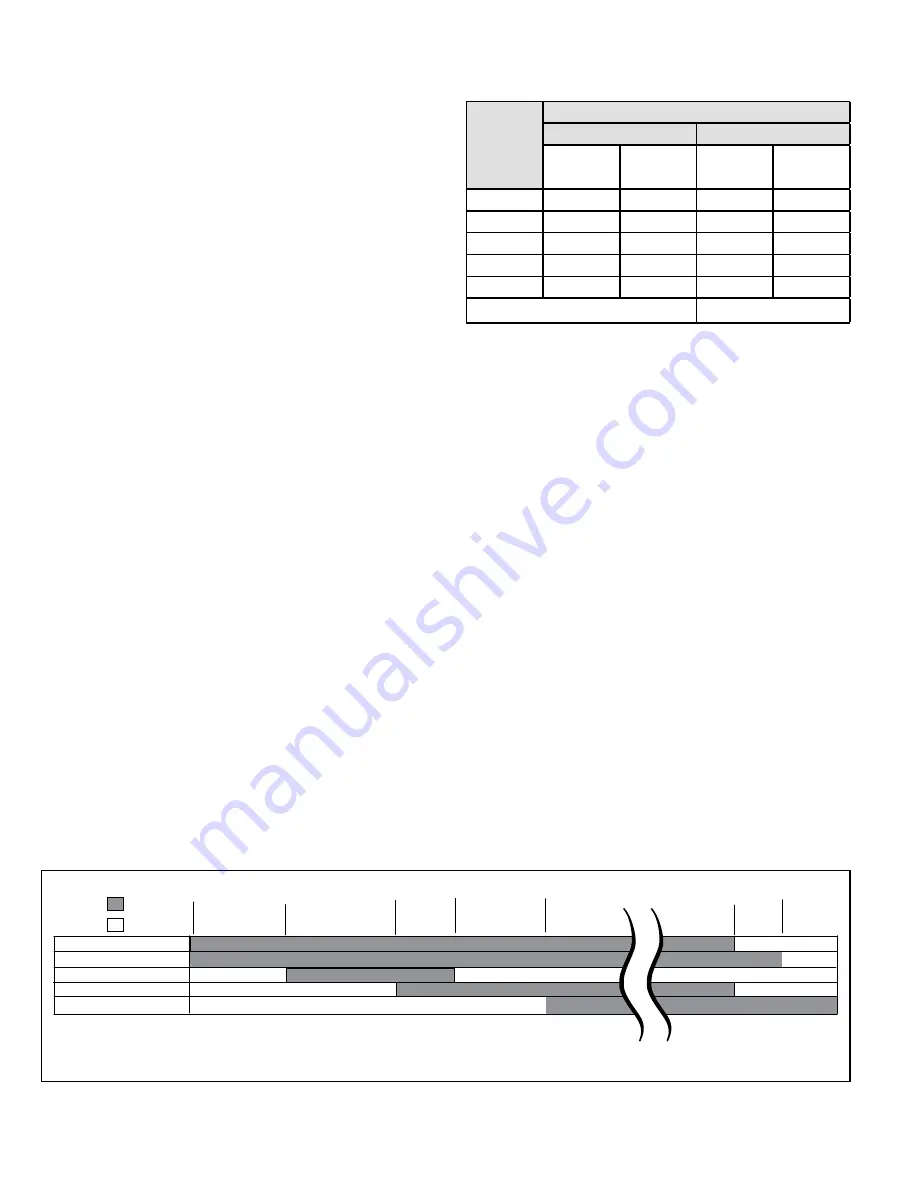
507327-01
Page 28 of 34
Issue 1809
Demand
15
ON
OFF
CAI
35
1
Pre-Purge
Ignitor Warm-up
Blower
“On” Delay
Post
Purge
5 SEC
80
Ignitor
Gas Valve
Indoor Blower
39
Trial for
Ignition
Blower on time will be 45 seconds after gas valve is energized. Blower off time will depend on “OFF TIME” Setting.
Figure 28. Integrated Ignition Control
5.
Is the filter dirty or plugged? Dirty or plugged filters will
cause the limit control to shut the unit off.
6. Is gas turned on at the meter?
7. Is the manual main shut-off valve open?
8. Is the internal manual shut-off valve open?
9. Is the unit ignition system in lock out? If the unit locks
out again, call the service technician to inspect the unit
for blockages.
10.
Is pressure switch closed? Obstructed flue will cause
unit to shut off at pressure switch. Check flue and
outlet for blockages.
11.
Are flame rollout switches tripped? If flame rollout
switches are tripped, call the service technician for
inspection.
Heating Sequence of Operation
See Figure 28
1. When thermostat calls for heat, combustion air blower
starts.
2. Combustion air pressure switch proves blower
operation. Switch is factory set and requires no
adjustment.
3. After a 15 second pre-purge, the hot surface ignitor
energizes.
4. After a 20 second ignitor warm-up period, the gas
valve solenoid opens. A 4 second trial for ignition
period begins.
5.
Gas is ignited, flame sensor proves the flame, and the
combustion process continues.
6.
If flame is not detected after first ignition trial, the
ignition control will repeat steps 3 and 4 four more
times before locking out the gas valve. The ignition
control will then automatically repeat steps 1 through
6 after 60 minutes.
7. To interrupt the 60 minute, move thermostat from
“Heat” to “OFF” then back to “Heat.” Heating sequence
then restarts at step 1.
Gas Pressure Adjustment
Gas Flow (Approximate)
Table 11. Gas Meter Clocking Chart
Capacity
Seconds for One Revolution
Natural
LP
1 cu ft
Dial
2 cu ft
Dial
1 cu ft
Dial
2 cu ft
Dial
-045
80
160
200
400
-070
55
110
136
272
-090
41
82
102
204
-110
33
66
82
164
-135
27
54
68
136
Natural - 1000 btu/cu ft.
LP-2500 btu/cu ft
Furnace should operate at least 5 minutes before checking
gas flow. Determine time in seconds for two revolutions of
gas through the meter. (Two revolutions assures a more
accurate time.) Divide by two and compare to time in Table
11. If manifold pressure matches Table 13 and rate is
incorrect, check gas orifices for proper size and restriction.
Remove temporary gas meter if installed.
NOTE
:
To obtain an accurate reading, shut off all other gas
appliances connected to meter.
Supply Pressure Measurement
A threaded plug on the inlet side of the gas valve provides
access to the supply pressure tap. Remove the threaded
plug, install a field provided barbed fitting and connect a
manometer to measure supply pressure. See Table 13
for proper line pressure. Replace the threaded plug after
measurements have been taken.