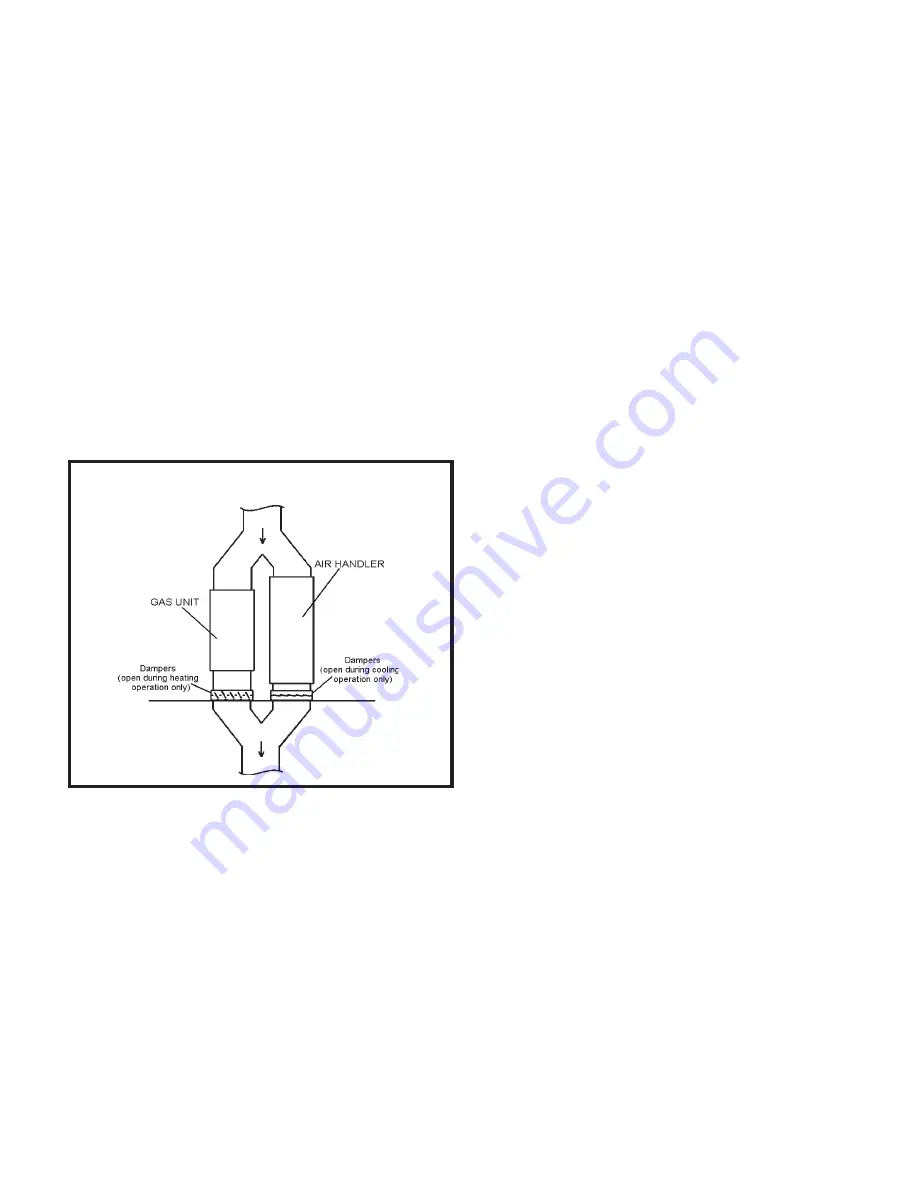
506528-01
Page 5 of 37
Issue 1035
Temperature Rise
NOTE:
Furnace must be adjusted to obtain
a
temperature
rise within the range specified on the unit nameplate. Failure
to do
so
may cause erratic limit operation and may result in
premature heat exchanger failure.
This furnace must be installed so that its electrical
components are protected from water.
Installed in Combination with a Cooling Coil
When this furnace is used with cooling units, it shall be
installed in parallel with, or on the upstream side of, cooling
units to avoid condensation in the heating compartment. See
Figure 2. With a parallel flow arrangement, a damper (or
other means to control the flow of air) must adequately
prevent chilled air from entering the furnace. If the damper
is manually operated, it must be equipped to prevent
operation of either the heating or the cooling unit, unless it
is in the full
HEAT or COOL
setting. See Figure 2.
This furnace may be installed in alcoves, closets, attics,
basements, garages, and utility rooms in the upflow or
horizontal position.
This furnace design has not been certified for installation in
mobile homes, recreational vehicles, or outdoors.
Use of Furnace as a Construction Heater
These units are not recommended for construction heating
during any phase of construction. Very low return air
temperature, harmful vapors and operation of the unit with
clogged or misplaced filters will damage the unit.
These units may be used for heating of buildings or structures
under construction, if the following conditions are met:
•
The vent system must be permanently installed per these
installation instructions.
•
A room thermostat must control the furnace. The use
of fixed jumpers that will provide continuous heating is
not allowed.
•
The return air duct must be provided and sealed to the
furnace.
•
Return air temperature range between 60°F (16°C) and
80°F (27°C) must be maintained.
•
Air filters must be installed in the system and must be
maintained during construction.
•
Air filters must be replaced upon construction
completion.
•
The input rate and temperature rise must be set per the
furnace rating plate.
•
One hundred percent (100%) outdoor air must be
provided for combustion air requirements during
construction. Temporary ducting may supply outdoor
air to the furnace. Do not connect duct directly to the
furnace. Size the temporary duct following these
instructions in section for Combustion, Dilution and
Ventilation Air in a confined space with air from outside.
•
The furnace heat exchanger, components, duct system,
air filters and evaporator coils must be thoroughly
cleaned following final construction clean-up.
•
All furnace operating conditions (including ignition, input
rate, temperature rise and venting) must be verified
according to these installation instructions.
When installed, this furnace must be electrically grounded
according to local codes. In addition, in the United States,
installation must conform with the current National Electric
Code, ANSI/NFPA No. 70. The National Electric Code (ANSI/
NFPA No. 70) is available from the following address:
National Fire Protection Association
1 Battery March Park
Quincy, MA 02269
NOTE:
This furnace is designed for
a
minimum continuous
return air temperature
of
60° F (16°C) or an intermittent
operation down to 55° F (13°C) dry bulb for cases where
a
night setback thermostat is used. Return air temperature
must not exceed 85° F (29°C) dry bulb.
Figure 2
Heating Unit Installed Parallel to Air Handler Unit