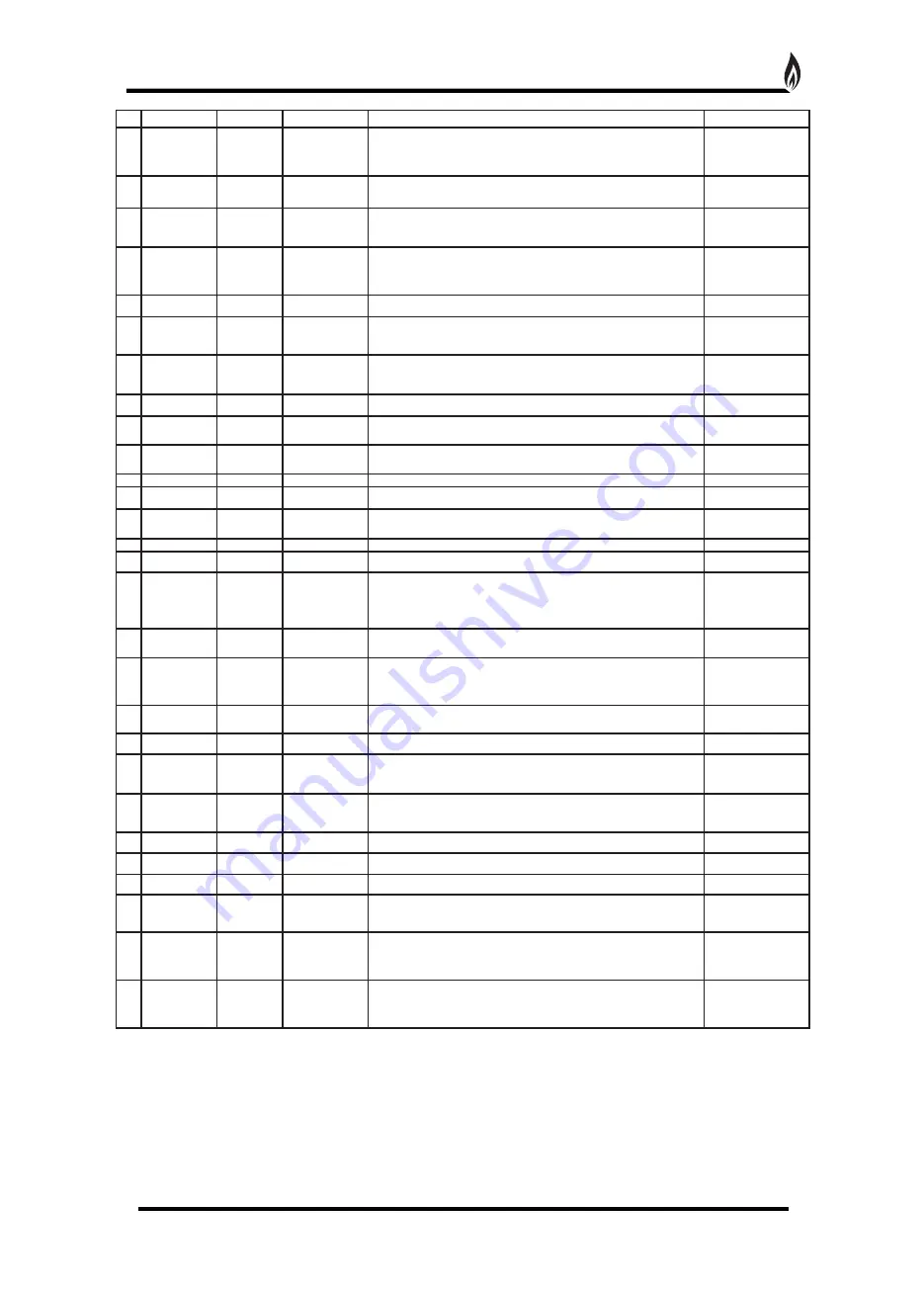
TROUBLE SHOOTING (GAS SAFE ENGINEER ONLY)
12
Reset control by pressing start button for 1 second and releasing. Then press again the same way
to attempt a normal start command. Repeat up to 10 times as necessary to see if this overcomes
the issue as it may resolve itself eventually.
Check to see if gas is present at gas appliance inlet. (Check gas supply is on, the gas line purged of
air and the supply pipework is free of blockages or contamination)
Rectify and perform start
cycle to clear the Error code.
Try to light the fire as normal.
No gas on appliance
inlet
Clean the pilot free of any dirt, dust carbon granules or lint, especially around the brass body of the
bunsen burner and its gas and electrical connection and the area around the flame ports and the
spark plug and electrode tip. Check the electrode gap is 3- 4 mm.
Rectify and perform start cycle
to clear the Error code. Try to
light the fire as normal.
Replace pilot if necessary
Pilot contaminated with
lint or other materials
Check ignition cable for damage and listen and watch for tracking out of spark to see if it is present
but not making it to the electrode tip on the pilot burner.
If cable damaged, replace
cable. Reset error by
performing a normal start
cycle and try to start again.
Replace pilot if necessary.
Reset and try again
Reset and try again
No Spark at Electrode
(fire not igniting pilot
burner)
Clear pipe and consider changing pilot
Pilot pipe or pilot injector
could be blocked)
E00
Code Comment
Apperance
Possible Cause
Action
TESC locked due to
failed ignition
Red Led is
permanently on
TESC unit ( and
E00 on handset, if
used)
Temporary air
disturbance around pilot
burner
Check pilot pipe, check flame appearance of pilot flames
E01
Low current from
thermocouple but
flame: possibly CO
alarm
Flashing Red LED
on TESC Control
Pilot pipe blocked - no
gas reaching pilot
burner
Occurs if started ok then subsequently loss of thermocouple current. Check for flue problems. Fire
cuts out to prevent over heating
E02
Too high ambient
temperature ( >73 °C)
around control
Negative flue pull or
blocked flue or similar
Reset and try again
Check if connected correctly and terminations are sound
E03
No, defective, or bad
connected
thermocouple
Bad connection
Reset and try again
Sensing flame on pilot when no flame should be there. Investigate.
E04
False flame signal
Occurs during stopping
fire
Reset and try again
Replace batteries
E06
Too low voltage on
power supply to start
the burner
Weak or old or defective
batteries
Reset and try again
Replace batteries / power adaptor
E07
Power supply
breakdown during
peak current
consumption
Check/change all the
batteries or check power
adaptor. : Note always
change all batteries
together never only 1 or 2
Reset and try again
Replace if necessary
E08
Error caused by
external pressure
switch
Check the pressure
switch
Reset and try again
Check pressure switch connections, check to see if jumpers are in place on back of TESC.
E09
Error caused by
external pressure
switch
Pressures switch action
connection or jumpers
missing or not connected
properly
Reset and try again
Check pressure switch connections, check to see if jumpers are in place on back of TESC.
E10
Error caused by
external pressure
switch
Pressure switch action
connection or jumpers
missing or not connected
properly
Reset and try again
Check switch for damage, contamination across terminals or damaged wiring. Disconnect wired
thermostat if fitted and try a start, if it works replace thermostat
E11
Short circuit on wired
thermostat (if used)
Check switch
Reset and try again
Check switch for damage, contamination across terminals or damaged wiring. Disconnect wired
thermostat if fitted and try a start, if it works replace thermostat
E12
Open circuit on wired
thermostat (if used)
Check wiring and
thermostat
Reset and try again
Check switch for damage, contamination across terminals or damaged wiring. Disconnect wired
thermostat if fitted and try a start, if it works replace thermostat
E13
Wired thermostat is
out of tolerance
Check wiring and
thermostat
Reset and try again
Clean as necessary. Replace switch panel as necessary if damaged or too contaminated.
disconnect wired control panel and try again – if it works replace wired control panel
E14
Button (-) sticks
either on TESC or on
wired control panel (if
used)
Check for contamination
around buttons
Reset and try again
Clean as necessary. Replace switch panel as necessary if damaged or too contaminated.
disconnect wired control panel and try again – if it works replace wired control panel
E15
Button (+) is shorted
to other buttons
either on TESC or on
wired control panel (if
used)
Check for contamination/
damage
Reset and try again
Clean as necessary. Replace switch panel as necessary if damaged or too contaminated.
disconnect wired control panel and try again – if it works replace wired control panel
E16
Button (ON/OFF) is
shorted to other
buttons either on
TESC or on wired
control panel (if used)
Check for contamination
/ damage and replace
wired switch panel if
necessary
Reset and try again
Jumpers on back of
valve missing
Check to see if jumpers
are in 10 way connector
Reset and try again
Check and clean around the area of the pilot for lint and other contamination. Check where the
thermocouple connects to the TESC control for the same contamination. Clean these areas.
E05
False flame signal
Flame sensing on pilot
before start of ignition
sequence or after valve
has shut off.
Contamination of
electrode to ground
Reset and try again
Replace Pilot
Defective thermocouple
Check and clear
Blocked flue
Reset and try again
Check manual for correct placement
Poor position of
Ceramic parts
Check flue
Chimney blocked
causing Co / Co2 to
build up in the room
build
Change pilot or thermocouple
Pilot thermocouple
defective / old
Clear error and restart to check ignition ok
Possible temporary air
disturbance on pilot
flame
Summary of Contents for Ethos 3S
Page 23: ......