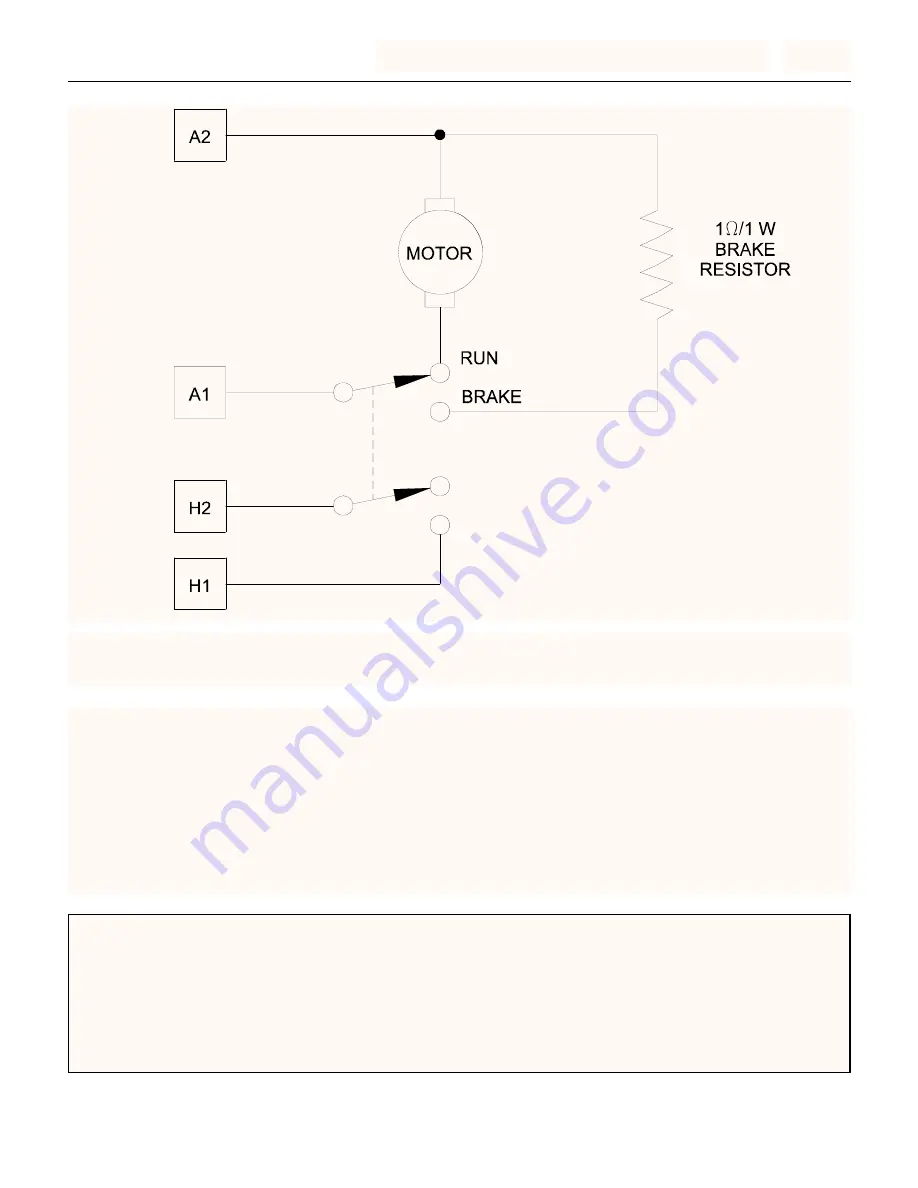
13
Operation
A 1
Ω
, 1 W resistor is used as the dynamic brake resistor. For
motors rated
1/
17
horsepower and lower, a dynamic brake resistor
is not necessary since the armature resistance is high enough to
stop the motor without demagnetization. In this case, replace the
dynamic brake resistor with 12 gauge wire.
m
Warning
Wait for the motor to completely stop before switching it back
to RUN. This will prevent high armature currents from
damaging the motor or drive.
Figure 9. Dynamic Brake Connection
250-0256.qxd 3/12/99 10:05 AM Page 13
Summary of Contents for M1740009.OO
Page 1: ...USER S MANUAL M1740009 OO Pulse Width Modulated Adjustable Speed Drives for DC Brush Motors...
Page 8: ...2 Dimensions Figure 1 M1740009 OO Dimensions...
Page 31: ...25 Block Diagrams Figure 16 Block Diagram...
Page 32: ...26 Block Diagrams Figure 22 Input Circuit Diagram...
Page 33: ...Notes 27...
Page 34: ...Notes 28...