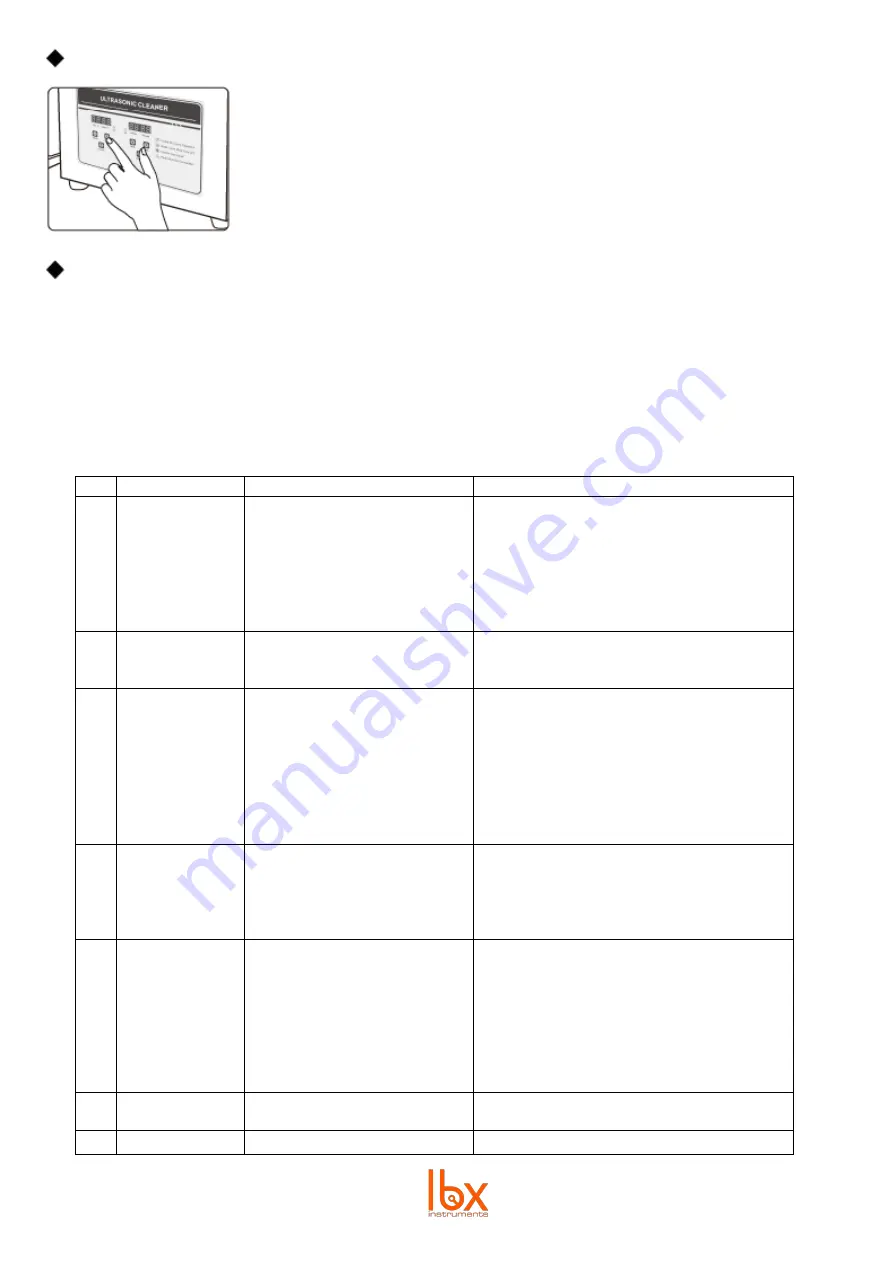
6
Heat
For the first boot, the setting temperature on the display is random, and actual
temperature is room temperature. Touch
TEMP+
once to increase temperature by
1
℃
; Touch
TEMP-
once to decrease temperature by 1
℃
. Temperature display
shows setting temperature and actual temperature when heater is working, the
heater indicator goes off when actual temperature reaches setting temperature.
Power OFF
Press “ON/OFF” to stop worki
ng and then cut off the power. Pour the liquid out, clean the tank and the unit with
cloth for next use.
4.
Maintenance
•
To keep your device in good working conditions the electrical control system should be blown regularly
with high pressure air to get rid of the dust.
•
Clean the tank at least once a week
Trouble clearing
No.
Problems
Possible Cause
Solutions
1
No ultrasonic
activity
A.
Power supply not connected
B.
Fuse broken
C.
Cable is short circuited
D.
Transducer is short circuited
E.
PCB Board broken
F.
Other reasons
A.
Check and plug power switch
B.
Check the fitted power supply and change
the same specification fuse
C.
Connect fitted cable or replace a new
D.
Consult with your supplier
E.
Check the broken part and change it
F.
Consult with your supplier
2
Time control
failure
A.
Timer failure
B.
Other reasons
A.
Replace the timer or digital control
panel
B.
Consult with your supplies
3
No heating
A.
Heater power switch
had a bad linkage
B.
Fuse burn out
C.
Heating pad burn out
D.
Digital display board
out of control
E.
Other reasons
A.
Check heating plug and connect it
well. Check outlet line with multimeter: OK
if resistance value is a few hundred OHMs.
B.
Change the same specification fuse
C.
Replace the bad heating pad if open
circuit
D.
Check the broken part and change it
E.
Consult with your supplier
4
Temperature
control failure
A.
Thermostat loosen
B.
Thermostat tube broken
C.
Digital display out of
control
D.
Other reasons
A.
Fasten the thermostat header
B.
Replace the thermostat
C.
Check the broken part and change it
D.
Consult with your supplier
5
Not well
cleaning
A.
Not strong ultrasonic
cleaning
B.
Too high or too low liquid
surface
C.
Too high too low
temperature
D.
Not suitable cleaning liquid
E.
Other Reasons
A.
Connect ultrasonic button and adjust
B.
Adjust liquid into the best surface
C.
Adjust the temperature into the most fitted
D.
Stop and switch off power supply, replace
suitable liquid after previous liquid
cooling down
E.
Consult with your supplier
6
Electric Leakage A.
Customer side not grounded
B.
Machine not grounded
A.
Ensure it is grounded
B.
Check if machine earth wire loosens
7
Scrap
Not repairable or discarded
Summary of Contents for ULTR Series
Page 20: ...www labbox com ...