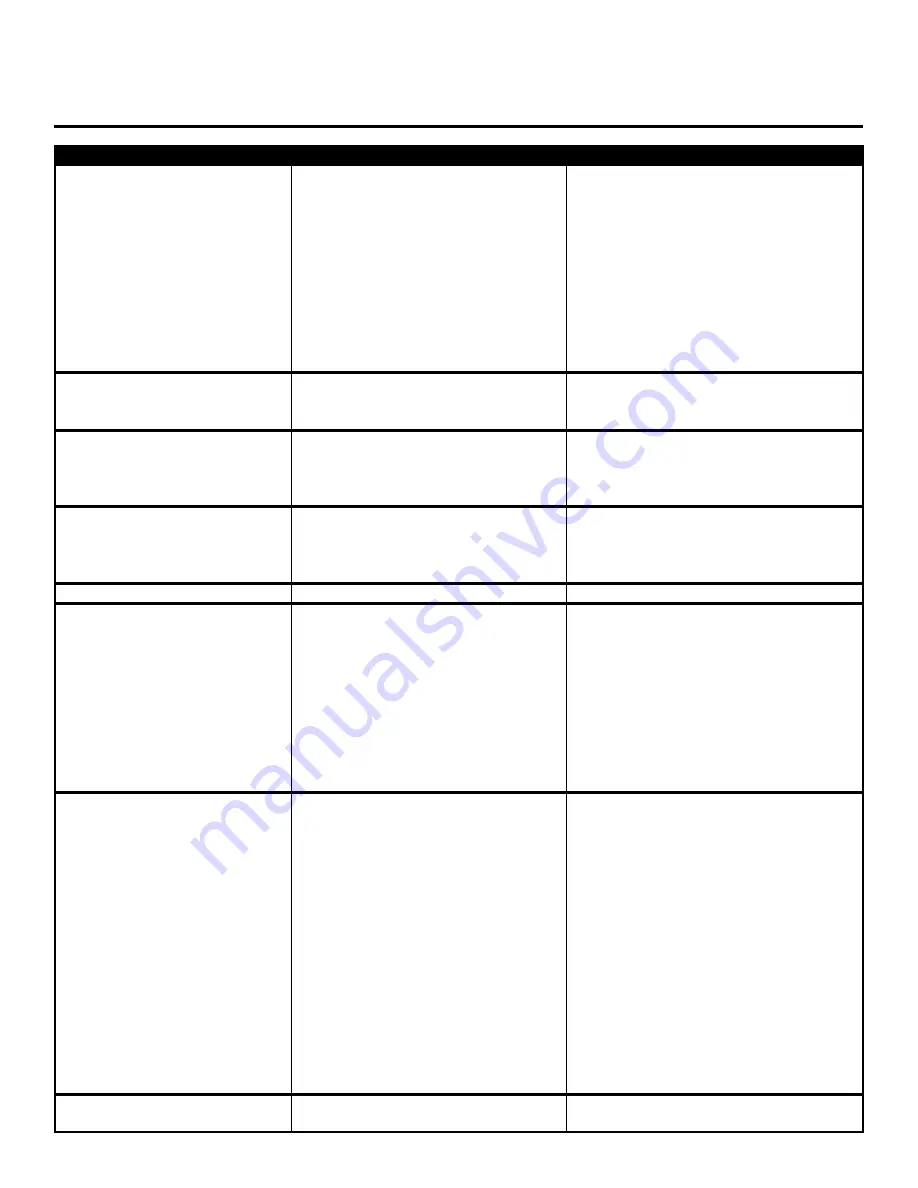
Rev A 07132018
Page | 4
Troubleshooting
Problem
Cause
Solution
System does not dispense solution
1. Water inlet strainer is clogged
1. Clean it or replace if necessary
2. Too much water pressure
2. Use a water pressure regulator in case of
more than 100PSI
3. Insufficient water pressure
3. 20PSI is the minimum required pressure.
4. The venturi is clogged
4. Soak venturi in hot water and inspect visually,
gently removing debris. Replace assembly if
needed.
5. Activation valve is clogged by mineral
5. Soak the valve assembly in a solution of hot
water and limescale remover. Replace assemly
if needed.
Water flow won' t stop
1. Activation valve is clogged by minerals or
other water borne debris
1. Soak the valve parts and valve seat in lime-
scale remover to clean. Replace them if neces-
sary
Activation valve is leaking
1. Valve cap not tight enough to seat
1. Firmly hand tighten the valve cap until leak
stops.
2. Not properly positioned
2. Reposition the valve or change it if necessary
Connections and end cap are leaking
1. Missing o
-
ring in the connection fitting
and / or end cap
1. Apply the o
-
ring or replace the entire part
2. O
-
ring in the connections or end cap are
damaged
2. Replace the o
-
rings or replace the entire end
cap
Flex gap is leaking
1. Flexible membrane is damaged
1. Replace the Flex Gap
A
-
gap is spraying out and or leaking
1.Limescale film or dirt on the A
-
gap
’
s upper
nozzle
1. Soak in hot water and limescale remover to
remove buildup. Replace if necessary
2. Venturi coated with limescale or dirt
2. Soak in hot water and limescale remover to
clean. Replace it if necessary
3. There is a buildup or clog in the discharge
hose
3. Clean the hose to eliminate restriction
4. Discharge hose is above the dispenser
4. Make sure the discharge hose dispenses be-
low the dispenser insuring no back pressure
Improper concentration of chemical or
no suction
1. Insufficient water pressure
1. 14PSI is the minimum working pressure.
2. Metering tip clogged
2. Replace tip
3. Foot valve clogged
3. Soak in hot water, hand clean or change it
4. Venturi clogged
4. Soak in hot water or limescale remover to
clean. Replace it if necessary
5. Air leak in chemical pick up tubing line
5. Check the entire line. Replace the tubing
check the connections and cable tie
6. Product is too thick
6. Change the pick up hose. Switch to a bigger
diameter. (need ¼ x 5/16 coupler)
7. Product container is too far from the sys-
tem
7. The standard installation is positioning the
tank under the system, 5ft max
8. Excess concentration
8. Tip is not the correct one or not inserted fully.
System continues to draw chemical
after the valve is closed
1. Chemical tank is positioned higher than
the dispenser causing siphoning
1. Move chemical container below the dispenser
discharge point