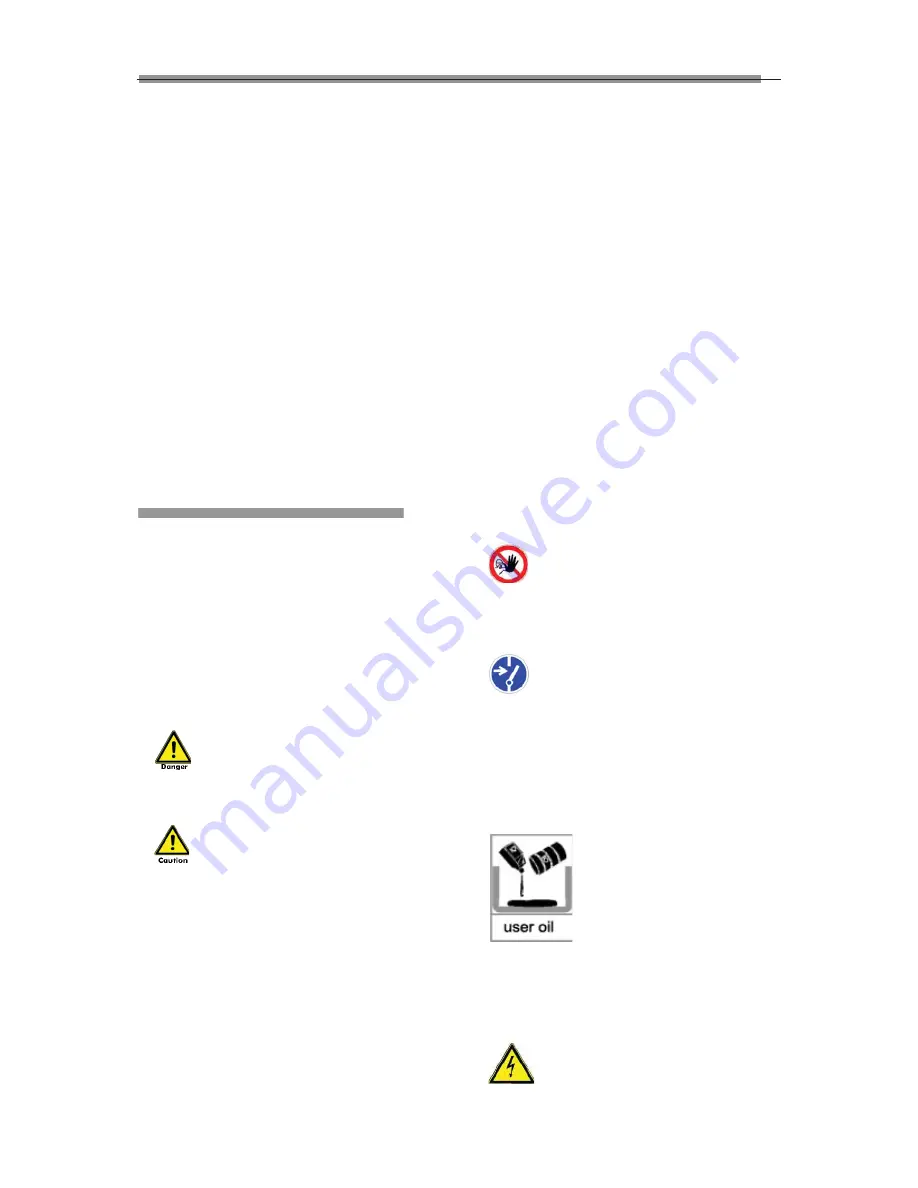
LAUNCH X-631/X-631+ Wheel Aligner
iii
inspected as to their operational condition.
• The necessary personal safety equipment for
operating, maintenance and repair personnel is
available and being worn.
• The operating instructions are always in a legible
condition and are completely available at the
machine location.
• The machine is only operated, maintained and
repaired by qualified and authorized personnel.
• This personnel is instructed routinely in all pertaining
questions of work safety and environmental
protection, and knows the operating instructions,
especially the safety instructions contained therein.
• All safety and warning labels attached to the
machine are not removed and are legible.
Concrete safety instructions
and applied symbols
Concrete safety instructions are provided in the
following operating instructions which will point out
any unavoidable remaining risks during the machine
operation. These remaining risks contain hazards for:
Persons
Product and machine
The environment
Symbols used in the operating instructions should
draw attention to the safety signs!
This symbol points out that specifically
personal injury risks may be anticipated (Mortal
danger, risk of injuries).
This symbol signifies that especially
hazards for the machine, material and the
environment may be encountered.
The most important objective of the safety signs
exists in the prevention of personal injuries.
If the warning triangle with the wording “danger” is on
a safety notice, hazards for the machine, material and
the environment are not excluded.
If the warning triangle with the wording “caution” is on
a safety reference, personal injuries are not
anticipated.
The applied symbol cannot replace the text of the
safety reference. The text must therefore always be
completely read!
Basic safety measures during normal
operations:
The machine may only be operated by trained and
authorized personnel who know the operating
instructions and are capable of working with them!
Prior to switching the machine on, check and verify
that:
Only authorized personnel are located within the
working range of the machine.
No one can be injured when the machine is activated!
Check the machine for visible damages prior to use
and verify that it is only operated in perfect condition!
Report any problems immediately to the supervisor!
Prior to each operating start, check and verify that all
safety equipment operates perfectly!
Basic safety measures during service
and maintenance:
Adhere to the inspection and maintenance intervals
specified in the operating instructions!
Block access to the work area of the machine
to unauthorized personnel prior to performing
maintenance or repairs! Attach or set up a warning
sign that points out maintenance or repair work!
Pull the power plug prior to any maintenance
or repair work or switch off the main switch for the
power supply and secure with a lock, if the power
supply is installed.
The key to this lock must be in the hands of the
person that is completing the maintenance or repair
work! Only use perfect load suspension and lifting
equipment when replacing heavy machine parts!
Properly dispose of environmentally
hazardous lubricants, coolants or cleaning agents!
Working on the electrical equipment:
Repairs on electrical equipment of the
machine may only be performed by trained
Summary of Contents for X-631 Plus
Page 1: ......