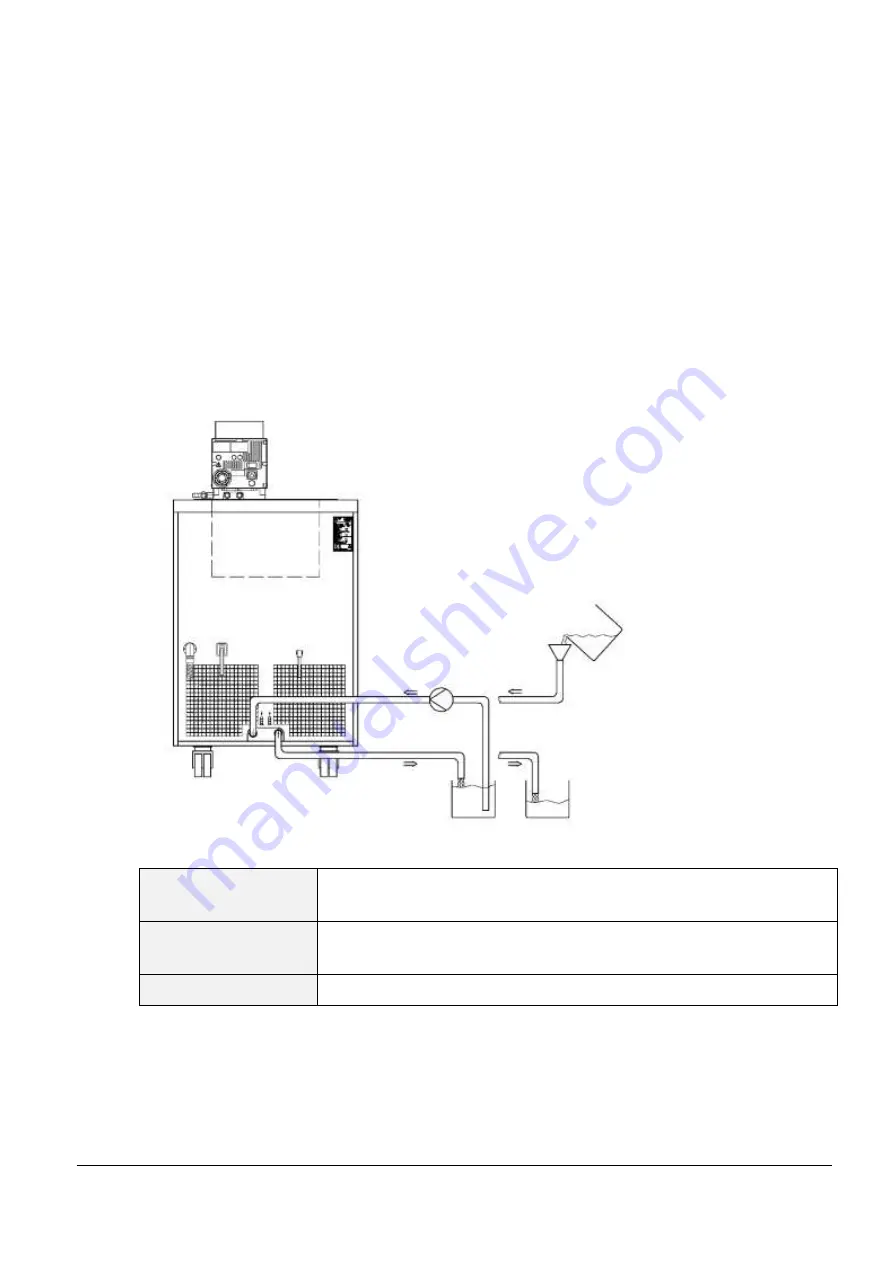
116 / 137
Proline Kryomats
9.3.4.2.2
Decalcifying the water cooling circuit
At regular intervals of 3 months or longer, the water-cooled condenser must be decalcified or cleaned. This depends
on the hardness of the cooling water and the degree of soiling. Drain according to (
Required equipment:
Two containers of approx. 10 to 20 liters volume.
Use a suitable pump (drum pump) or a hose with funnel. Place the funnel as high as possible so that the
device can fill quickly.
Fit connecting hoses between container, pump, cooling water inlet and between cooling water outlet
and back to container.
Change containers when top
one is empty.
Acting time:
Continue the pump stage until most of the foamy reaction, usually at the start, has
decayed. Generally, this is achieved after about 15 to 30 minutes.
Decalcifier:
Water with LAUDA Decalcifier LZB 126.
It is essential to follow the safety instructions when handling the chemicals.
Flushing:
Allow at least 30 liters of water to flow through.
9.3.5
Repair information
If you need to send in a unit for repair, it is essential to first contact the LAUDA Service (
9.5).
When sending in the unit, ensure that it is carefully and properly packed. LAUDA cannot be
held liable for any damage caused by improper packing.
Standard & Alternative