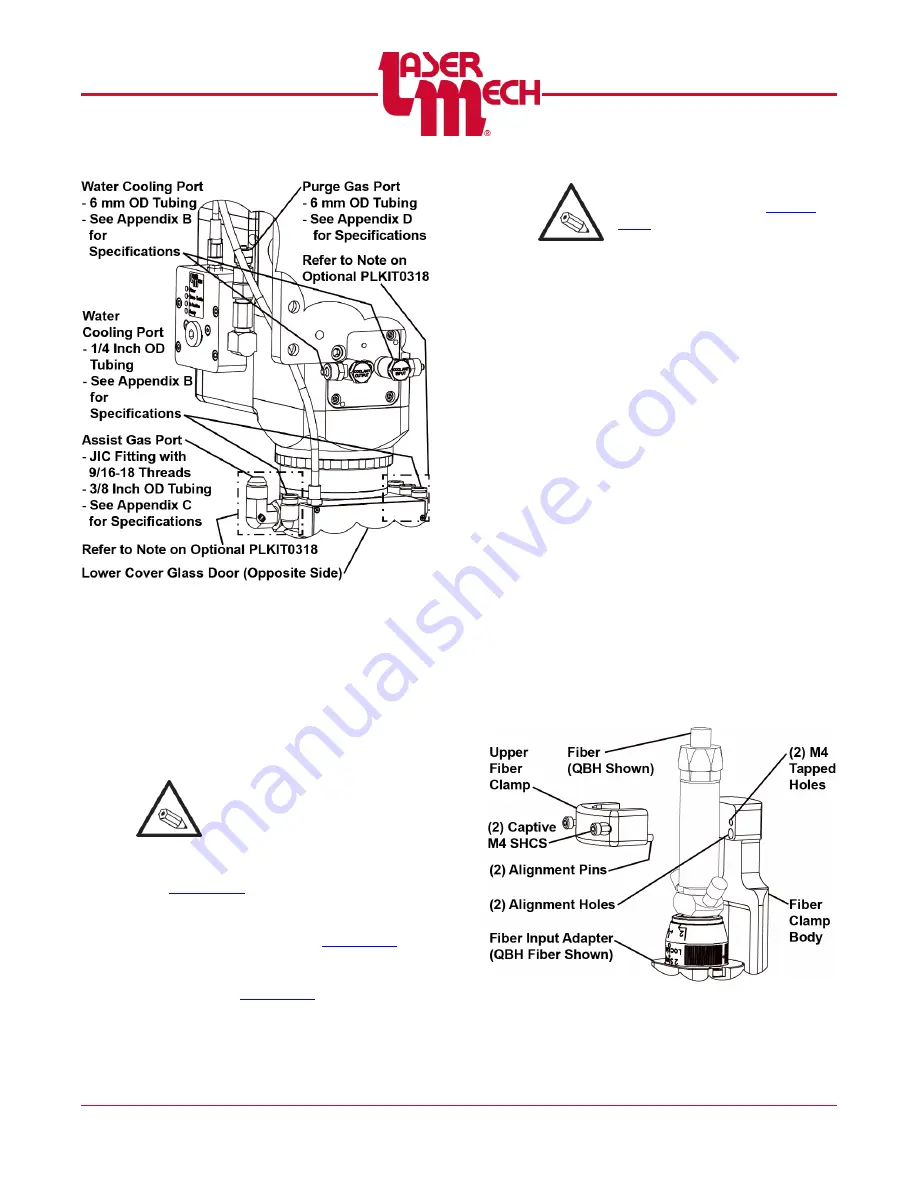
PLMNL0252 REV. B Effective Date: 10/16/17
4
FiberCUT
®
HR Operation Manual
Figure 5
2.3 Fiber Input
The fiber input adapter is where the fiber
optic cable plugs into the cutting head. See
. There are several standard types
of industrial fiber (QBH/HLC-8,
QD/LLK-D/LCA, Q5/LLK-B, and PIPA).
Each of these fibers requires a unique fiber
input adapter.
EVERY TIME the fiber is
removed and/or installed the
upper cover glass MUST BE:
Inspected and/or cleaned according to
OR
Replaced according to
2.3.1 To Install the Fiber
Refer to
guidelines and the fiber
manufacturer’s information for
specific instructions.
The upper fiber clamp MUST be
removed according to
fiber.
2.3.2 QBH Upper Fiber Clamp
The fiber clamp provides added
stability to the fiber connection.
It is necessary to remove the upper
fiber clamp to access the fiber. See
To remove the upper fiber clamp:
1. Loosen the (2) captive M4 SHCS
and remove the upper fiber
clamp.
To install the upper fiber clamp:
2. Align the upper fiber clamp so:
The (2) alignment pins are
in-line with the alignment
holes in the fiber clamp body.
The (2) captive M4 SHCS
are in line with the M4
tapped holes in the fiber
clamp body.
3. Tighten the (2) captive M4
SHCS.
Figure 6