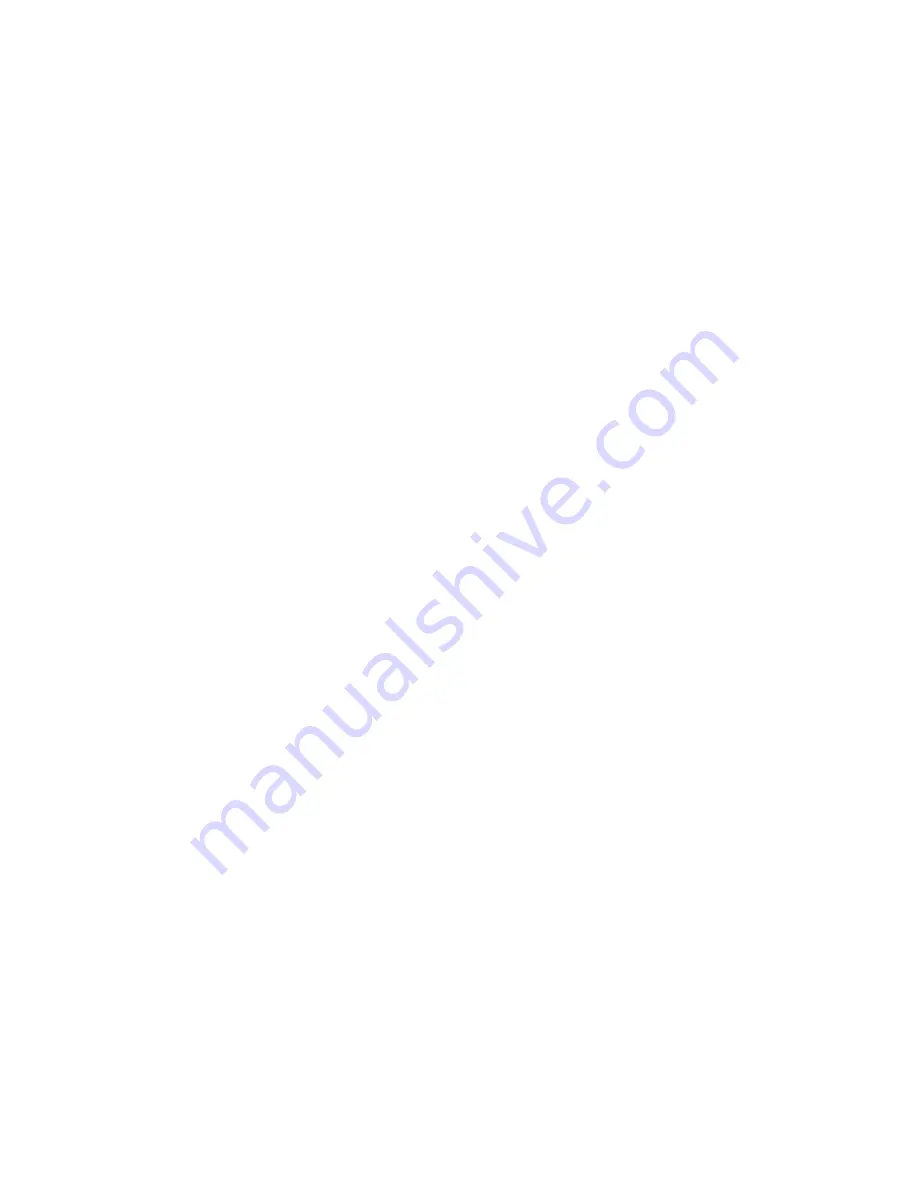
1W UHF AMPLIFIER ASSEMBLY
PUB99-92 rev 1: June 19, 2000
92-10
1
W UHF Amplifier
Inexpensive cotton swabs (available in drug stores or supermarkets) can be used for wiping the solvent
over the area to be cleaned, then a stiff bristle brush (an old toothbrush) can be used to scrub if
necessary. Use the swabs for mopping up the residue. Clean the board thoroughly, then inspect and
clean it again; don't merely rearrange the residue.
Be careful - do not allow solvent to run under power
transistors where it can dilute the heatsink compound.
CAUTION: VAPOURS FROM ALCOHOLS AND OTHER SOLVENTS ARE TOXIC AND
FLAMMABLE... DO NOT INHALE! IF YOU ARE A SMOKER, DO NOT SMOKE WHILE USING
FLAMMABLE SOLVENTS! USE ALL SOLVENTS ONLY IN A PROPERLY VENTILATED
LOCATION!
i)
Finally, if you have not already done so, set the bias potentiometers for the stage to maximum
resistance so that when power is applied, the FET will start at its lowest current. Then set the bias
as described in the RF PA, Visual/Vision Driver, and IPA RF amplifier sections of this manual. We
mentioned this procedure during step "j" above as well, because some circumstances may make it
simpler to set the bias in a High Band PA before replacing L9. When L9 is in place, each half of
the stage will need to be adjusted concurrently with a bias short on the opposite side (to turn off
the side not being set), otherwise the DC path through L9 makes the procedure impossible. This
is explained in the applicable PA, Visual Driver, or IPA section of the manual
7.1.1
Surface-mount Components Hints and Advice:
Failures of small surface mounted resistors on boards where they were companion to other components
having leads, were traced to mechanical overstress of their end caps as a result of the soldering
procedure to the component. Our manufacturing procedure has since been altered to fix this problem, and
despite our embarrassment, we think it is important that you should know about it. For your information:
1.
It is critical that surface mount components are soldered onto a clean flat surface. Use a suction
device followed by fluxed braid wick material to ensure that all old solder is removed from pads of
the board.
2.
If this is not possible due to the presence of other components, try to clean at least one of the
pads so it is flat (don't solder this end yet), then solder the other (solder-laden) pad FIRST,
pressing the component down into the puddle of solder. (Plain wooden toothpicks will serve well
as tools to apply pressure to components while soldering them). The remaining flat pad then can
be soldered.
To ensure minimum stress on any SM component, always be certain that the component is laying
flat in contact with the board before soldering except as above when it is necessary to melt the
solder on a pad first, and
never force it unless both ends of the component are free to move.
3.
If all the pads are loaded with solder, it will be necessary to heat all terminals of the component
simultaneously. Check with your local electronic parts dealer for special soldering iron tips and/or
other attachments (in addition to toothpicks) that will aid in surface-mount work.
4.
Always keep the tip of your iron clean and freshly tinned (wetted), for maximum heat transfer.