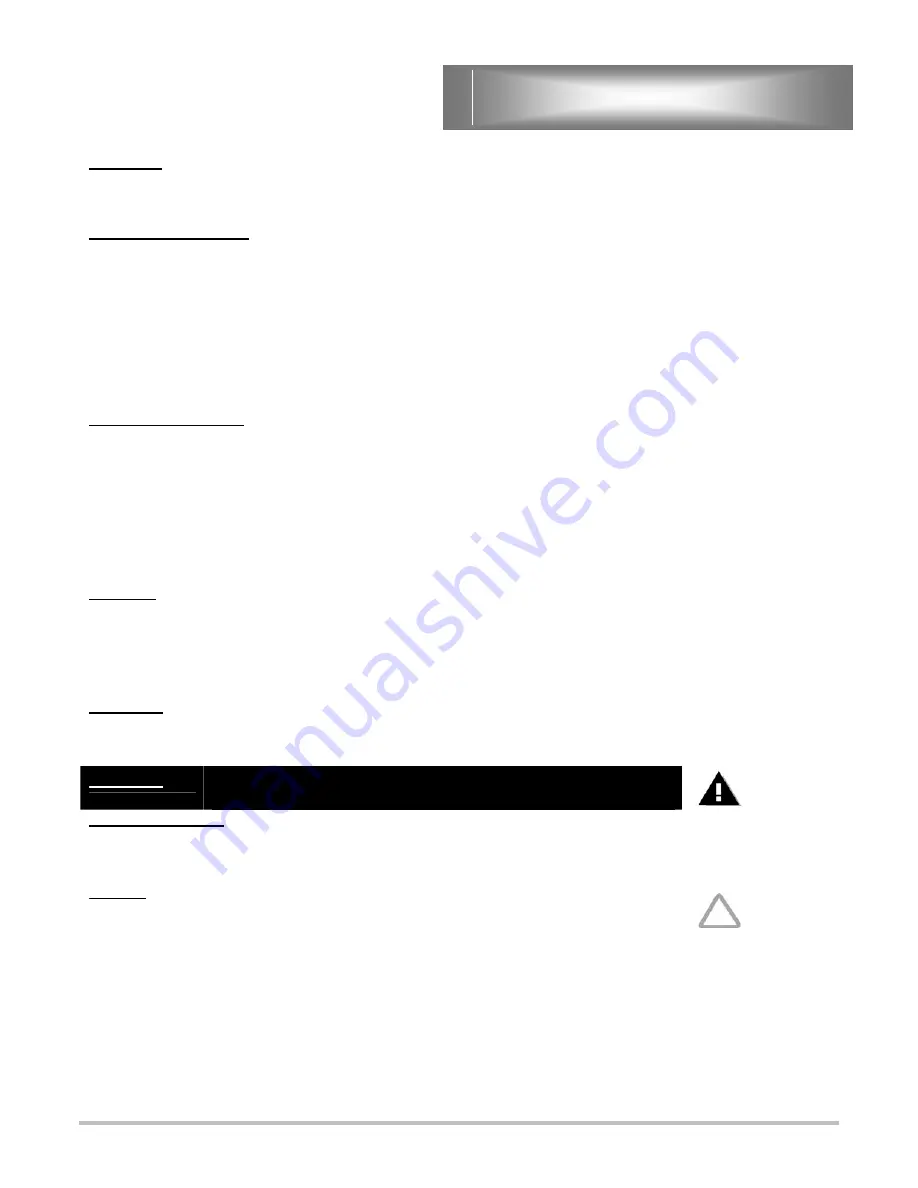
ETL File 3028821
7
Rev. A 2002
EQUIPMENT DESCRIPTION
Data Plate
On this plate you will find the oven model, serial number, electrical ratings, BTU’s, gas type, and
clearance specification.
Exterior Construction:
The oven exterior dimensions are 55” (139.7 cm) wide x 105” (266.7 cm) high x 51” (129.5 cm) Deep.
The Top, front, Back, and Sides are constructed of stainless steel with 5 inches of insulation.
Floor level loading.
Type I or Type II hood with single point exhaust connection complying with Uniform Mechanical Code
and NFPA 96.
The oven door is constructed of stainless steel with a full height single pain window and an interior
releasing mechanism.
Externally mounted florescent light.
Interior Construction:
The oven cavity dimensions are 36.5” (92.71 cm) wide x 75” (190.5 cm) high x 39” (99.06 cm) deep.
The interior is constructed of stainless steel.
Smooth and simple rack loading and unloading.
Gentle rack lift and rotation protects delicate products.
The rack is designed to hold up to twenty 18”x 26” sheet pans.
A built in steam generator generates steam quickly.
Fully adjustable airflow for even cook.
Controls:
Large digital display, which is easy to understand and operate.
Icon-driven (touch) panel allows for easy operation.
Pre-Programmable Product Selections.
Heat Loss Compensation for Consistent baking.
Technical:
The oven requires a 208/240 three-phase power supply and a 115 single phase power supply for controls.
The oven requires no clearance from combustible wall construction.
WARNING
THE WATER FROM THE STEAM DRAIN OUTLET IS EXTREMELY
HOT AND MAY CAUSE SERIOUS BURNS.
Steam Drain Outlet
Water exits the steam generating system through this outlet It is located at the lower right-hand jamb or
left rear corner of the oven.
NOTICE
Left rear drain point is provided. Remove the plug from
the location required and route to a floor drain. A 1” gap
must be provided between oven drain and floor drain.