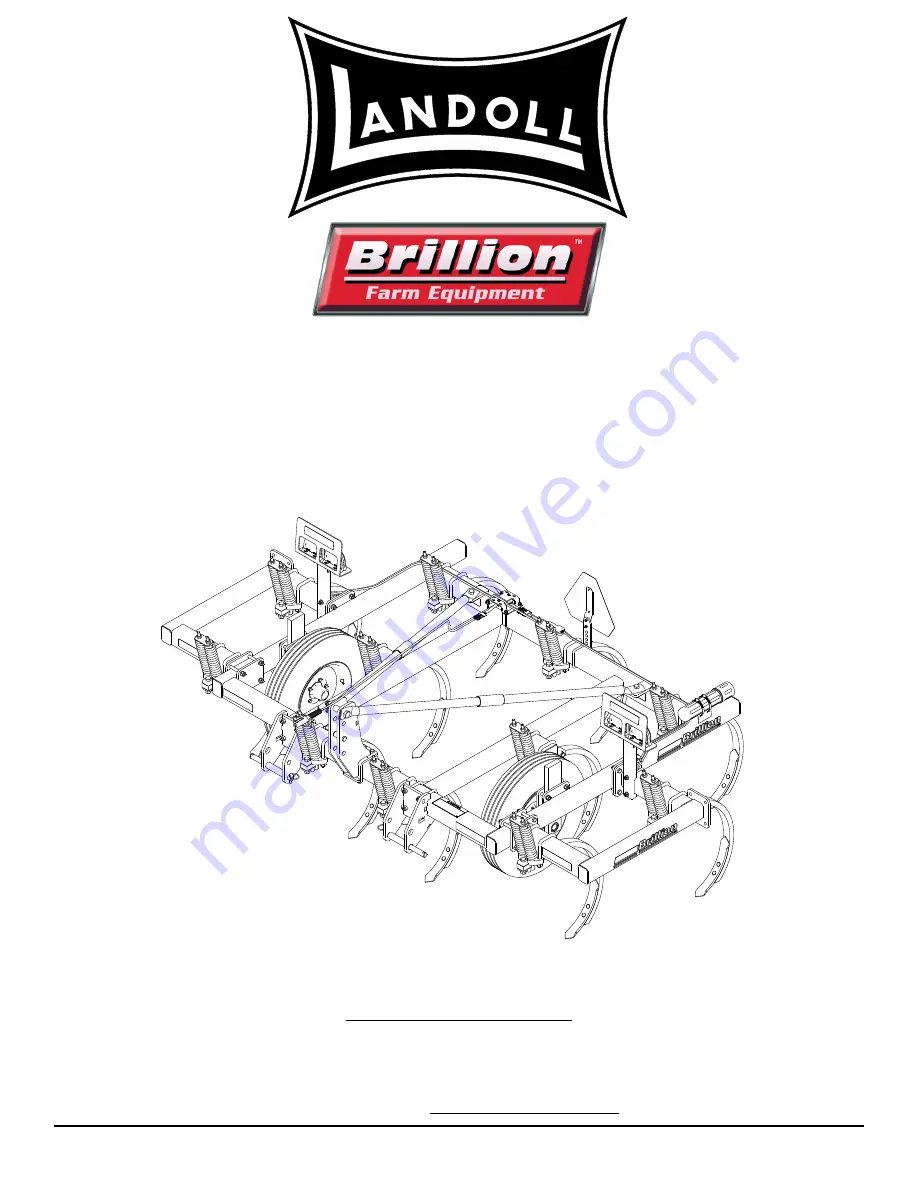
®
175rev1113 7D525
LANDOLL CORPORATION
1900 North Street
Marysville, Kansas 66508
(785) 562-5381
800-428-5655 ~ WWW.LANDOLL.COM
Chisel Plow, 3 - Bar Mounted
Models: CPP7 through CPP12
Operator’s Manual
Summary of Contents for Brillion CPP7
Page 2: ......
Page 12: ...1 8 7D525 INTRODUCTION AND SAFETY INFORMATION Table provided for general use NOTES...
Page 17: ...ASSEMBLY 2 5 Figure 2 4 Lower Hitch Orientation View AA View BB View CC...
Page 21: ...ASSEMBLY 2 9 Figure 2 8 CPP9 Shank and Shovel Locations 5 5 5 5 5 33 6KDQN...
Page 22: ...2 10 7D525 ASSEMBLY Figure 2 9 CPP10 Shank and Shovel Locations 5 5 5 5 5 33 6KDQN...
Page 23: ...ASSEMBLY 2 11 Figure 2 10 CPP11 Shank and Shovel Locations 5 5 5 5 5 5 33 6KDQN...
Page 24: ...2 12 7D525 ASSEMBLY Figure 2 11 CPP12 Shank and Shovel Locations 5 5 5 5 5 5 33 6KDQN...
Page 34: ...2 22 7D525 ASSEMBLY Table provided for general use NOTES...
Page 38: ...3 4 7D525 OPERATION Table provided for general use NOTES...
Page 42: ...4 4 7D525 MAINTENANCE Table provided for general use NOTES...