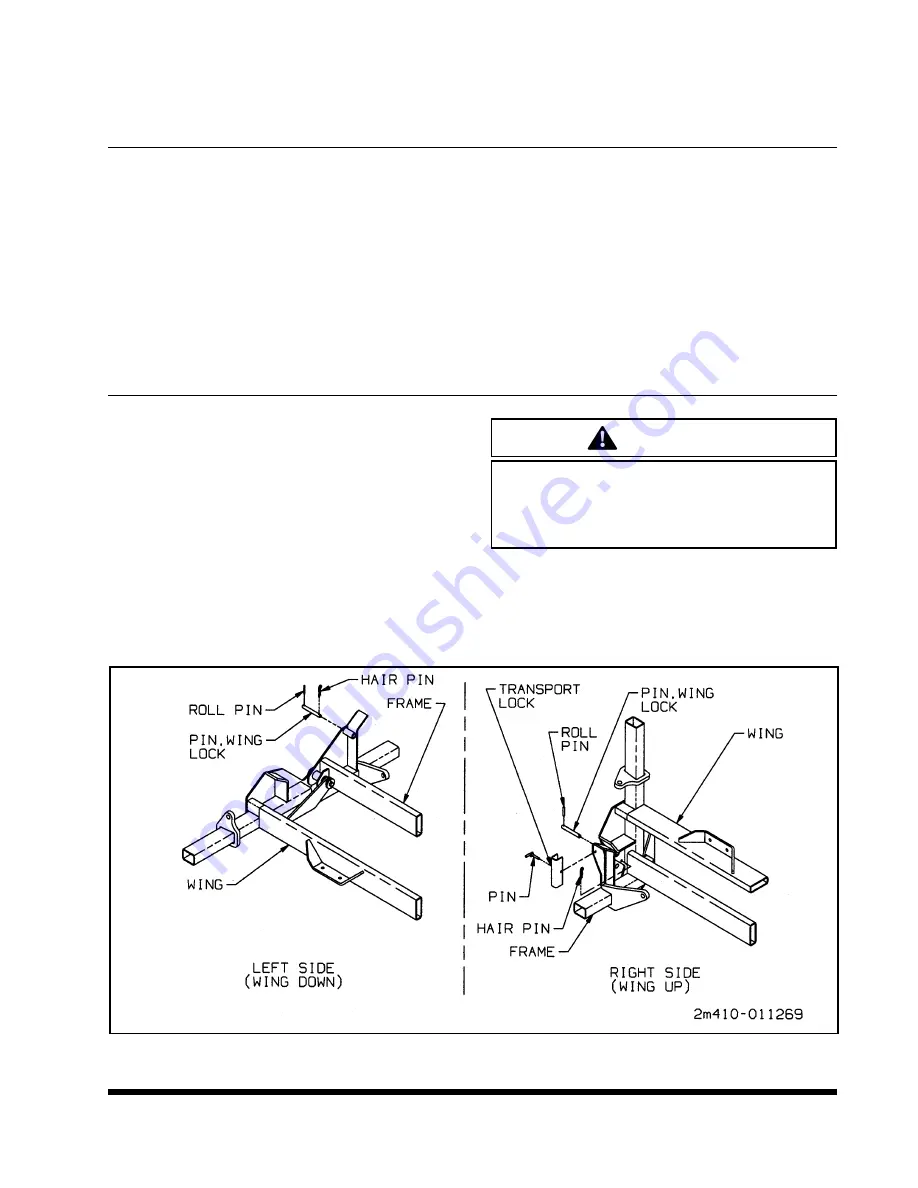
4-3 ATTACHING TO THE TRACTOR
4-3.1
Align the tractor drawbar with the ma-
chine. Raise or lower the Finisholl ring hitch,
as needed, using the swivel jack. Attach the
unit with proper size hitch pin.
4-3.2
Clean all hydraulic couplings and attach
to the tractor. When properly attached, the
hydraulic control lever should cause the Fin-
isholl to:
a.
Lower to the ground when the control arm is
moved forward or downward, and
b.
Raise when the control arm is moved back-
ward or upward.
4-3.3
Fully extend the hydraulic gauge wheel
cylinders, and place the cylinder lockouts in
the transport lock position over the cylinder
rods. Secure the lockouts with the lockout
pins.
4-3.4
Always place the swivel jack on the in-
terior mount before setting the machine in
motion.
4-4 FIELD OPERATION
4-4.1
Raise the unit to take the weight off of
the transport locks. Remove the transport
locks from the lift cylinders (on the main
frame only). Store the transport locks on the
front hinge brackets
(See Figure 4-2)
.
4-4.2
Remove the wing lock pins and store in
the extra hole in the hinge bracket. Unfold
the wings and extend the fold cylinders com-
pletely
(See Figure 4-2)
.
CAUTION
FAILURE TO REMOVE WING LOCK
PINS BEFORE UNFOLDING WINGS
WILL CAUSE PERMANENT EQUIP-
MENT DAMAGE.
4-4.3
Check the front to rear leveling of the
frame. Adjust radius rod until frame is level
at working depth and lock it with the jam nut.
4-3
Figure 4-2 Transport Locks
Summary of Contents for 850 FINISHOLL
Page 3: ...MODEL 850 FINISHOLL OPERATOR S MANUAL PURCHASED FROM DATE ADDRESS PHONE NO SERIAL NO...
Page 4: ...i...
Page 8: ......
Page 12: ...2 4 Figure 2 1 850 11 Shank Placement Assembly...
Page 13: ...2 5 Figure 2 2 850 14 Shank Placement Assembly...
Page 14: ...2 6 Figure 2 3 850 16 8 Shank Placement Assembly...
Page 15: ...2 7 Figure 2 4 850 16 8 Shank Placement Assembly...
Page 16: ...2 8 Figure 2 5 850 19 4 Shank Placement Assembly...
Page 17: ...2 9 Figure 2 6 850 19 4 Shank Placement Assembly...
Page 18: ...2 10 Figure 2 7 850 22 Shank Placement Assembly...
Page 19: ...2 11 Figure 2 8 850 22 Shank Placement Assembly...
Page 20: ...2 12 Figure 2 9 850 24 8 Shank Placement Assembly...
Page 21: ...2 13 Figure 2 10 850 24 8 Shank Placement Assembly...
Page 22: ...2 14 Figure 2 11 850 27 4 Shank Placement Assembly...
Page 23: ...2 15 Figure 2 12 850 27 4 Shank Placement Assembly...
Page 24: ...2 16 Figure 2 13 850 30 Shank Placement Assembly...
Page 25: ...2 17 Figure 2 14 850 30 Shank Placement Assembly...
Page 26: ...2 18 Figure 2 15 850 33 N Shank Placement Assembly...
Page 27: ...2 19 Figure 2 16 850 33 N Shank Placement Assembly...
Page 28: ...2 20 Figure 2 17 850 33 Shank Placement Assembly...
Page 29: ...2 21 Figure 2 18 850 33 Shank Placement Assembly...
Page 30: ...2 22 Figure 2 19 850 35 Shank Placement Assembly...
Page 31: ...2 23 Figure 2 20 850 35 Shank Placement Assembly...
Page 32: ...NOTES 2 24...
Page 34: ...3 2 Figure 3 1 Frame Assembly 30 to 35...
Page 36: ...3 4 Figure 3 2 Rockshaft Installation Frame Figure 3 3 Rockshaft Installation Frame 30 and 35...
Page 38: ...3 6 Figure 3 5 Wing and Wing Extensions 17 35 Models...
Page 41: ...3 9 Figure 3 9 Fold Cylinder Bracket 17 through 27...
Page 42: ...3 10 Figure 3 10 Fold Cylinder Bracket 30 and Larger...
Page 43: ...3 11 Figure 3 11 Installation of Fittings in Manifold...
Page 44: ...3 12 Figure 3 12 Installation of Shanks and Clamps...
Page 46: ...3 14 Figure 3 14 Spring Shank Assembly Figure 3 15 Ratchet Jack Installation...
Page 47: ...3 15 Figure 3 16 Disc Gang Hydraulic Assembly...
Page 50: ...3 18 Figure 3 19 Leveling Assembly Installation...
Page 52: ...3 20 Figure 3 20 Warning Light Installation...
Page 54: ...3 22 Figure 3 21 Hydraulic Radius Rod...
Page 55: ...3 23 Figure 3 22 Rear Hitch Assembly Option...
Page 58: ...NOTES 3 26...
Page 65: ...4 7 Figure 4 6 Spike Harrow 3 and 5 Bar Figure 4 7 Spike Harrow Tilloll Style...
Page 68: ...4 10 Figure 4 11 Lubrication Schedule...
Page 70: ...NOTES 4 12...
Page 73: ...NOTES 5 3...
Page 74: ......