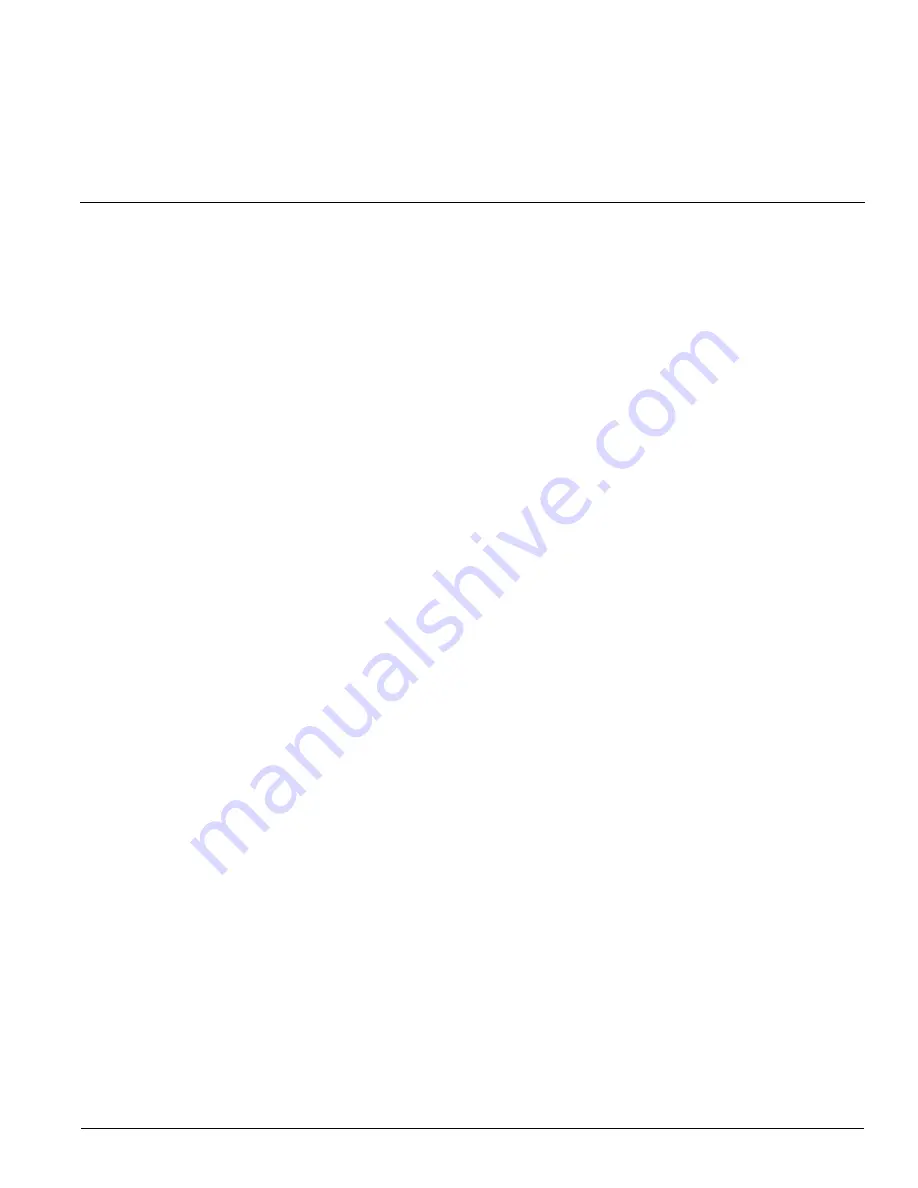
1-1
Chapter 1
Introduction and Safety Information
Introduction
This manual provides operating, servicing, and maintenance instructions for Model 825E/835E/845E semitrailer,
manufactured by Landoll Corporation, Marysville, Kansas 66508.
CHAPTER 1
Gives basic instructions on the use of this manual and understanding the safety
statements.
CHAPTER 2
Gives product specifications for the trailer, including measurements and component
specifications. A Standard Bolt Torque Table is provided to give guidelines for bolt
torques to be used when servicing this product.
CHAPTER 3
Gives instructions for the proper operation of the equipment.
CHAPTER 4
Gives general maintenance procedures, a maintenance schedule, and a lubrication
schedule.
I
mproper maintenance will void your warranty.
IF YOU HAVE ANY QUESTIONS CONTACT:
LANDOLL CORPORATION
1900 NORTH STREET
MARYSVILLE, KANSAS 66508
PHONE # (785) 562-5381 or (800) 428-5655
OR
FAX # (888) 527-3909
CHAPTER 5
Is a troubleshooting guide to aid in diagnosing and solving problems with the trailer.
PARTS MANUAL
Is a separate manual showing the various assemblies, sub-assemblies, and systems.
Refer to that manual when ordering Landoll replacement parts. Order parts from your
Landoll dealer.
WARRANTY
The Warranty Registration form is included with the product documents. Fill it out and
mail it within 15 days of purchase.
NOTE: IMPROPER ASSEMBLY, MODIFICATION, OR MAINTENANCE OF YOUR
LANDOLL MACHINE CAN VOID YOUR WARRANTY.
COMMENTS
Address comments or questions regarding this publication to:
LANDOLL CORPORATION
1900 NORTH STREET
MARYSVILLE, KANSAS 66508
ATTENTION: PUBLICATIONS - DEPT. 55