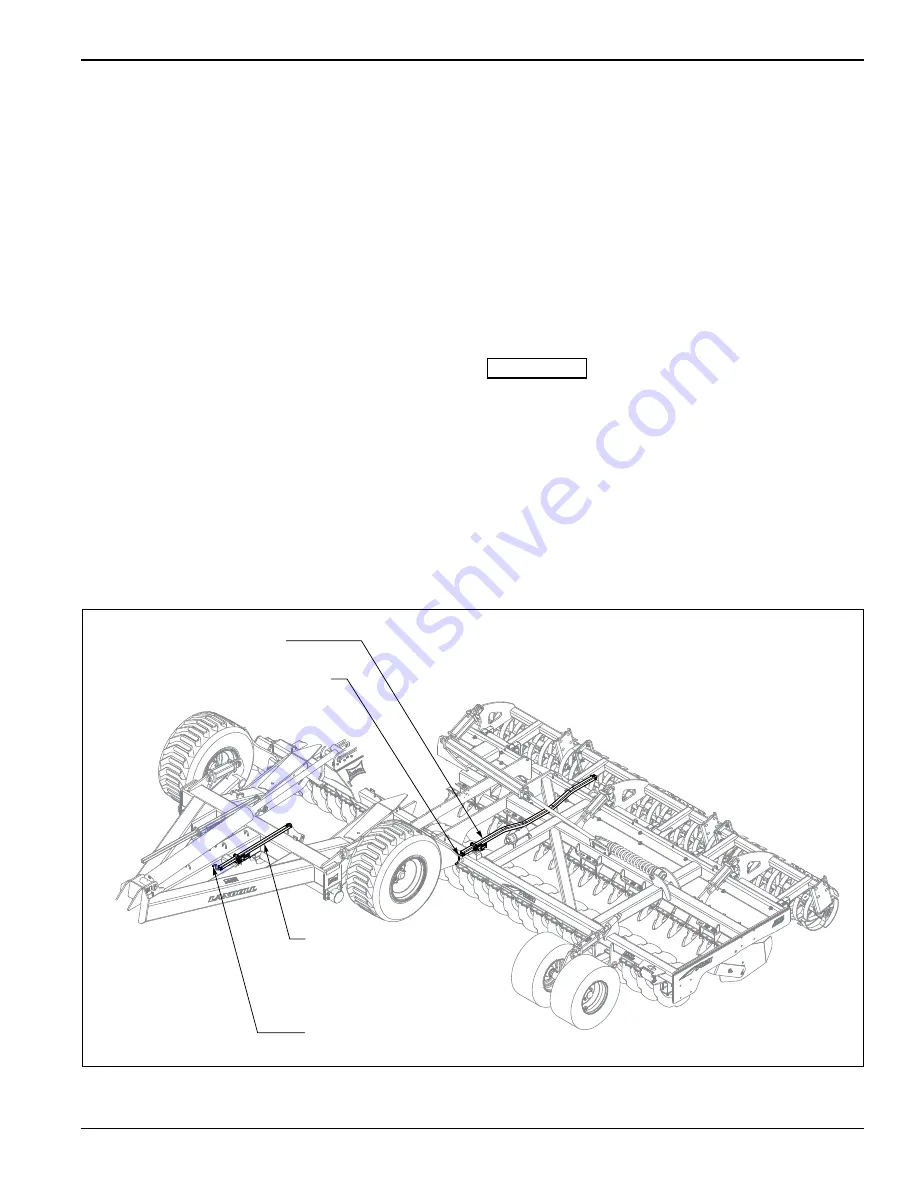
OPERATION AND MAINTENANCE
4-9
Operating Speed
Operating speed is very significant to the performance of
the HSL. It requires some speed to make it work
correctly.
1.
The minimum operating speed should be
approximately 7-1/2 to 8 miles per hour unless the
goal is to minimize the percent of crop residue being
buried.
2.
Maximum operating speed recommended is
approximately 12 miles per hour.
Operating speed is a function of the amount of crop
residue that is buried.
• The higher the speed of operation of the HSL the
greater the percent of crop residue that will be buried.
• The slower the speed of operation of the HSL the
greater the percent of crop residue left that will be left
on the surface.
When operating the HSL, high speed can be a substitute
for operating deep. On the other hand, in some cases, it
is desirable to reduce the percentage of crop residue
buried. In such cases the operator will need to reduce the
speed of operation. Typically the 8 to 10 miles per hour
window of operating speed will yield the most desirable
results.
Operating Depths and
Adjustments
The HSL has two depth control gauges. One directly in
front of the front row of disc assemblies and one directly
behind the rear row of disc assemblies
• Both depth gauges are independently adjustable.
• Both have their deepest setting correlate to the
gauge cylinders being completely retracted but that is
where the correlation stops.
• Typically the front gauges will need to be set slightly
deeper than the rear because the front disc row is
doing more work than the rear is.
IMPORTANT
Do not be concerned with the front and rear gauges
being set differently for optimum operation!
The optimum working depth is considered to be 2 to
3-1/2 inches. The HSL can work on either side of this
range with good performance and results. Working depth
adjustments should always be made in conjunction with
considerations of operating speed. The HSL can bury as
much plant debris in a relatively shallow working depth as
conventional machines can at considerable deeper
operating depths because of the mixing action inherent to
the HSL if operating speed is not sacrificed.
Figure 4-6: Operating Depths and Adjustments
DEPTH CONTROL TUBE
DEPTH CONTROL TUBE
DEPTH ADJUSTMENT HANDLE
DEPTH ADJUSTMENT HANDLE
Summary of Contents for 7831
Page 2: ......
Page 4: ......
Page 12: ...2 4 F 801 1115 Edition STANDARD SPECIFICATIONS Table provided for general use NOTES...
Page 30: ...4 14 F 801 1115 Edition OPERATION AND MAINTENANCE Table provided for general use NOTES...
Page 34: ...5 4 F 801 1115 Edition TROUBLESHOOTING GUIDE Table provided for general use NOTES...
Page 35: ......