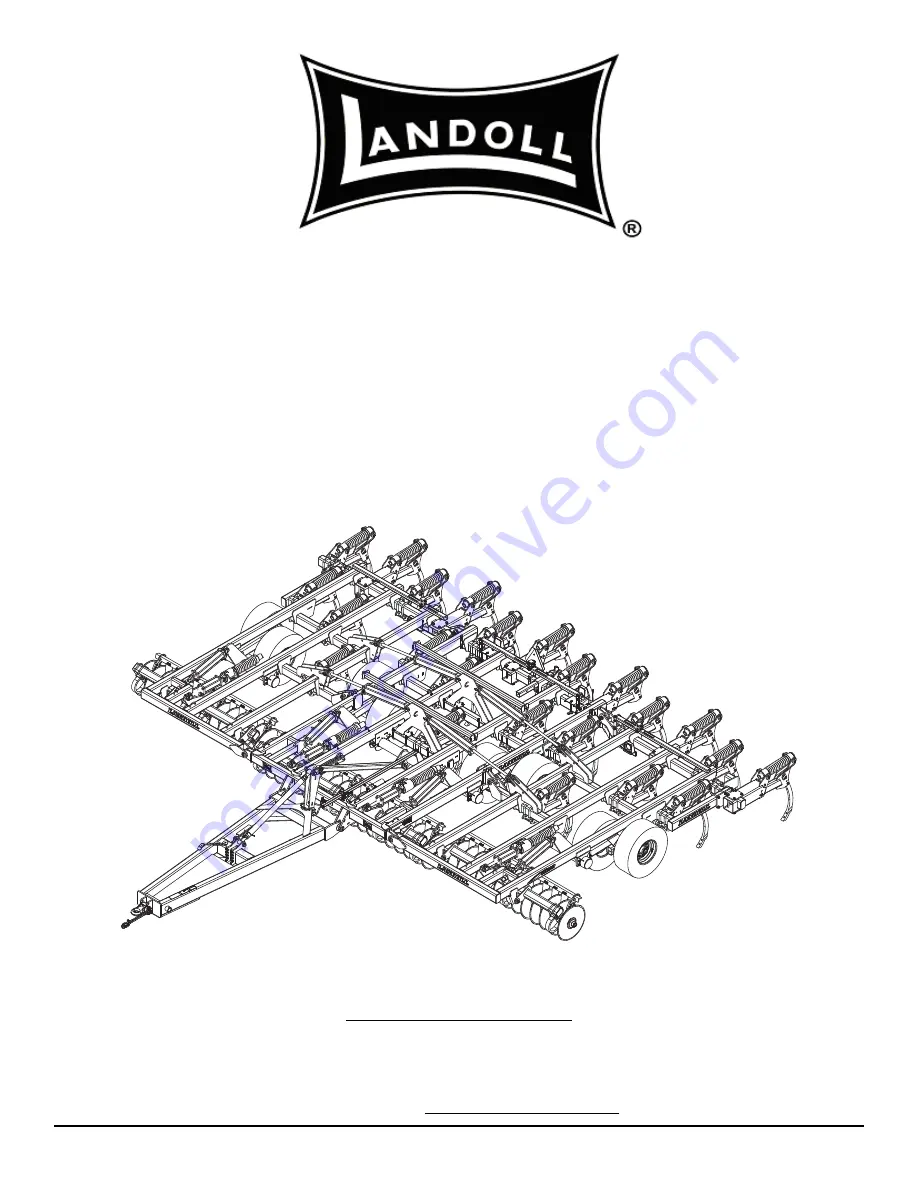
F-721-0513
LANDOLL CORPORATION
1900 North Street
Marysville, Kansas 66508
(785) 562-5381
800-428-5655 ~ WWW.LANDOLL.COM
Model 2131
Wing Coulter Chisel
Operator’s Manual
F-721-0513
LANDOLL CORPORATION
1900 North Street
Marysville, Kansas 66508
(785) 562-5381
800-428-5655 ~ WWW.LANDOLL.COM
Model 2131
Wing Coulter Chisel
Operator’s Manual