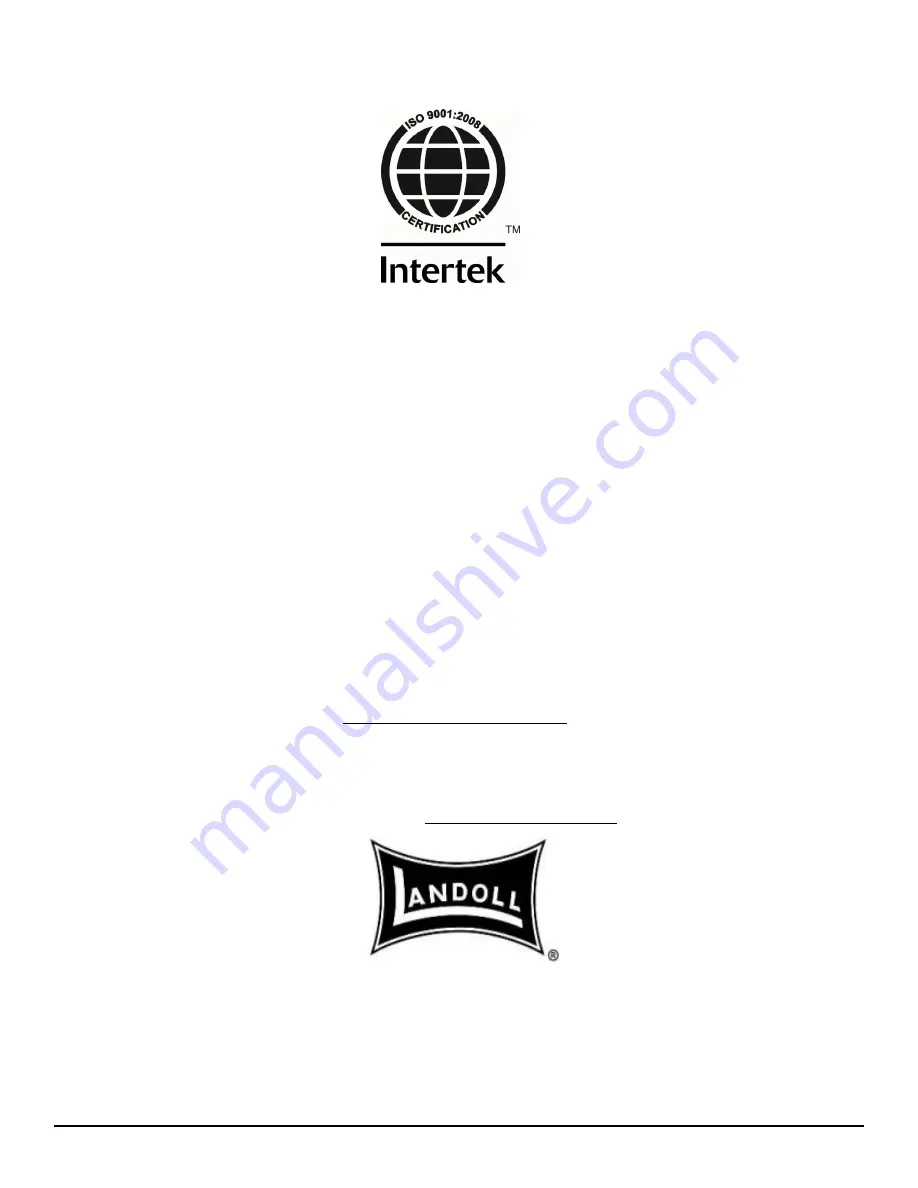
Equipment from Landoll Corporation is built to exacting
standards ensured by ISO 9001:2008 registration at all
Landoll manufacturing facilities.
Model 1550 Series
In-Row Ripper
Operator’s Manual
Re-Order Part Number F-298-0111
LANDOLL CORPORATION
1900 North Street
Marysville, Kansas 66508
(785) 562-5381
800-428-5655 ~ WWW.LANDOLL.COM
F-298-0111
01/2011
Copyright 2010. Landoll Corporation
"All rights reserved, including the right to reproduce this material or portions thereof in any form"
Summary of Contents for 1550 Series
Page 2: ......
Page 4: ...ii F 298 0111 Edition...
Page 9: ...STANDARD SPECIFICATIONS 2 3...
Page 12: ...2 6 F 298 0111 Edition STANDARD SPECIFICATIONS...
Page 26: ...3 14 F 298 0111 Edition ASSEMBLY INSTRUCTIONS Notes...
Page 31: ...OPERATION AND MAINTENANCE 4 5 Notes...
Page 32: ...4 6 F 298 0111 Edition OPERATION AND MAINTENANCE...
Page 34: ...5 2 F 298 0111 Edition TROUBLESHOOTING GUIDE Notes...
Page 35: ......