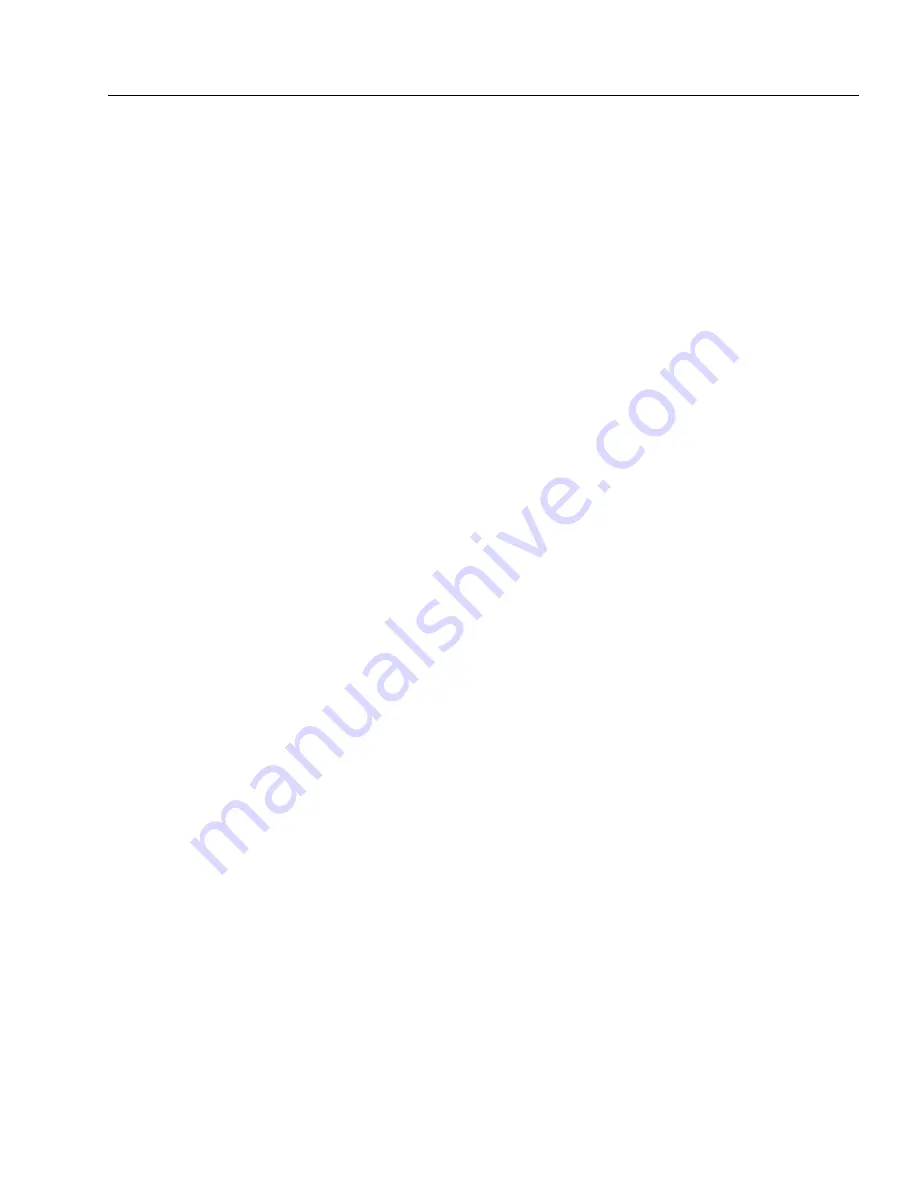
MVC SERIES PRESSURE WASHER
OPERATOR’S MANUAL
9
LANDA MVC
•
#96-61836 • REV. 5/03
PREVENTATIVE MAINTENANCE
1. Check to see that the water pump is properly lubri-
cated.
2. Follow winterizing instructions to prevent freeze dam-
age to the pump and coils.
3. Always neutralize and flush detergent from system
after use.
4. If water is known to be high in mineral content, use a
water softener in your water system or de-scale as
needed.
5. Do not allow acidic, caustic or abrasive fluids to be
pumped through system.
6. Always use high grade quality Landa cleaning prod-
ucts.
7. Never run pump dry for extended periods of time.
8. Use clean fuel-kerosene, No. 1 fuel oil or diesel. Re-
place fuel filter every 100 hours of operation. Avoid
water contaminated fuel as it will seize up the fuel
pump.
9. If machine is operated with smoking or eye burning
exhaust, coils will soot up, not letting water reach
maximum operating temperature. (See section on
Air Adjustments.)
10. Never allow water to be sprayed on or near engine
or burner assembly or any electrical component.
11. Periodically delime coils as per instructions.
12. Check to see that engine is properly lubricated.
It is advisable, periodically, to visually inspect the burner.
Check air inlet to make sure it is not clogged or blocked.
Wipe off any oil spills and keep this equipment clean
and dry.
The areas around the Landa washer should be kept clean
and free of combustible materials, gasoline and other
flammable vapors and liquids.
The flow of combustion and ventilating air to the burner
must not be blocked or obstructed in any manner.
MAINTENANCE AND SERVICE
Unloader Valves:
Unloader valves are preset and tested at the factory be-
fore shipping. Occasional adjustment of the unloader may
be necessary to maintain correct pressure. Call your
local dealer for assistance.
Winterizing Procedure:
Damage due to freezing is not covered by warranty. Ad-
here to the following cold weather procedures whenever
the washer must be stored or operated outdoors under
freezing conditions.
During winter months, when temperatures drop below
32°F, protecting your machine against freezing is nec-
essary. Store the machine in a heated room. If this is not
possible then mix a 50/50 solution of anti-freeze/water
into a 5 gallon bucket. Place a short section of garden
hose into the bucket and connect it to the machine. El-
evate the bucket and turn the pump on to siphon the
anti-freeze through the machine. If compressed air is
available, an air fitting can be screwed into the inlet con-
nector and, by injecting compressed air, all water will be
blown out of the system.
High Limit Hot Water Thermostat:
For safety, each machine is equipped with a high limit
control switch. In the event that the temperature of the
water should exceed its operating temperature, the high
limit control will turn the burner off until the water cools.
Pumps:
Use only SAE 30W non-detergent oil. Change oil after
the first 50 hours of use. Thereafter, change the oil every
three months or at 500 hour intervals. Oil level should be
checked by using the dipstick found on top of the pump
or the red dot visible through the oil gauge window. Oil
should be maintained at that level.
Cleaning of Coils:
In alkaline water areas, lime deposits can accumulate
rapidly inside the coil pipes. This growth is increased by
the extreme heat build up in the coil. The best prevention
for liming conditions is to use high quality cleaning de-
tergents. In areas where alkaline water is an extreme
problem, periodic use of Landa Deliming Powder (part
#9-028008) will remove lime and other deposits before
coil becomes plugged. (See Deliming Instructions for use
of Landa Deliming Powder.)
Deliming Coils:
Periodic flushing of coils is recommended.
1. Fill a container or optional float tank with 4 gallons of
water, then add 1 lb. of deliming powder. Mix thor-
oughly.
2. Remove wand assembly from spray gun and put
spray gun into container. Secure the trigger on the
spray gun into the open position.
3. Attach a short section (3-5 ft.) of garden hose to
machine to siphon solution from an elevated con-
tainer. Turn pump switch on, allowing solution to be
pumped through coils back into the container. Solu-
tion should be allowed to circulate 2-4 hours.
4. After circulating solution flush entire system with
fresh water. Reinstall wand assembly to spray gun.
Summary of Contents for MVC3-30321
Page 2: ......