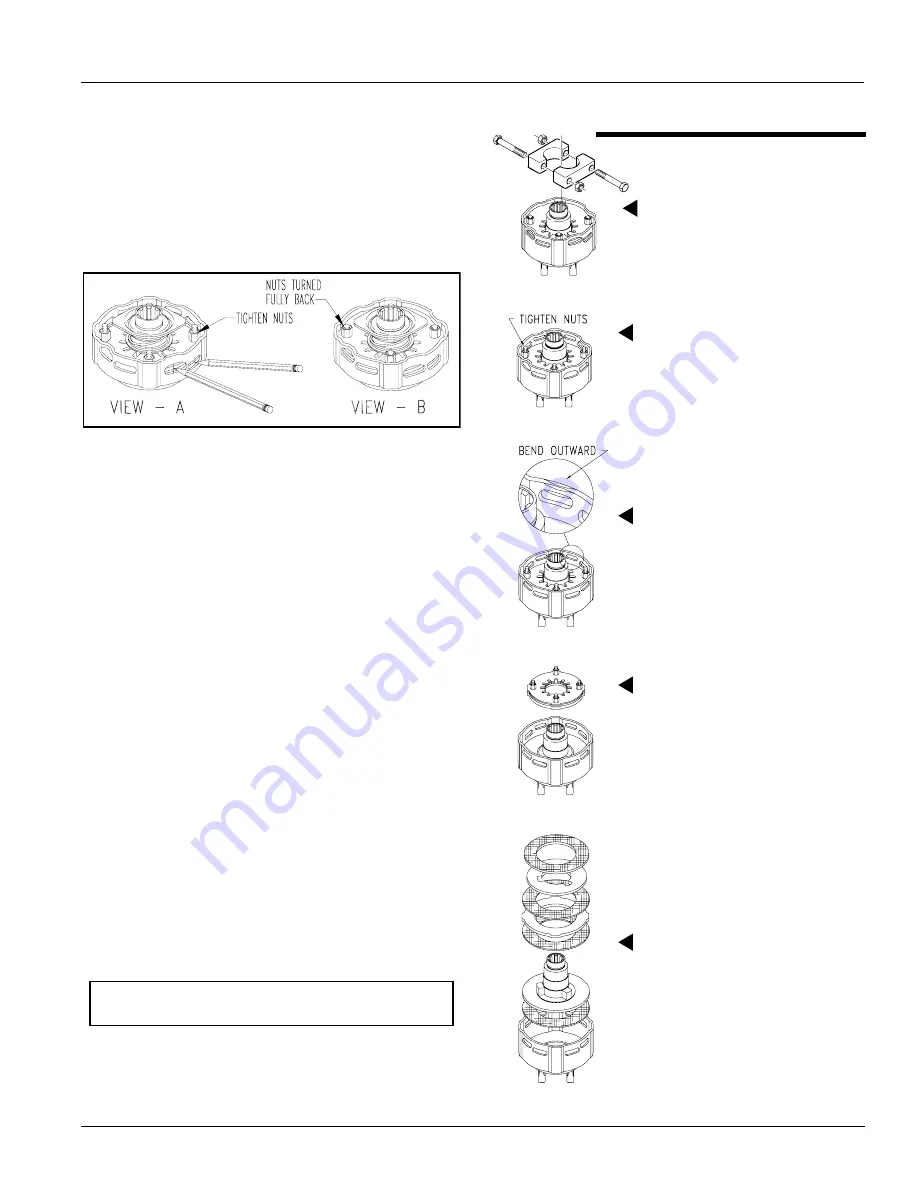
27
Section 5: Maintenance & Lubrication
2/02/08
RC5014 (540 RPM) and RCM5014 (1000 RPM) Rotary Cutters 330-117M
Land Pride
Type B Clutches
Clutch Run-In
Refer to Figure 5-8 (View - A):
1.
Using a pencil or other marker, scribe a line across the
exposed edges of the clutch plates and friction disks.
2.
Tighten all 4 nuts uniformly until spring load is low
enough that the clutch slips freely with PTO
engaged.
Type B Clutch Run-In
Figure 5-8
3.
Make sure the area is clear of all bystanders and
machine is safe to operate.
4.
Start tractor and engage PTO for 2-3 seconds to
permit slippage of clutch surfaces. Disengage PTO,
then re-engage a second time for 2-3 seconds.
Disengage PTO, shut off tractor and remove key.
Wait for all components to stop before dismounting
from tractor.
5.
Inspect clutch and ensure that the scribed markings
made on the clutch plates have changed position.
Slippage has not occurred if any two marks on the
friction disk and plate are still aligned. A clutch that
has not slipped must be disassembled to separate
the friction disk plates. See “Clutch Disassembly,
Inspection & Assembly” below.
Refer to Figure 5-8 (View - B):
6.
If no two marks on the friction disk and plate are still
aligned, Turn all 4 nuts fully back.
7.
Allow clutch to cool to ambient temperature before
operating again. Clutch is now ready for use.
8.
The clutch should be checked during the first hour of
cutting and periodically each week. An additional set
of scribe marks can be added to check for slippage.
Clutch Disassembly, Inspection & Assembly
If clutch run-in procedure above indicated that one or more
of the friction disks did not slip, then the clutch must be
disassembled to separate the friction disks.
23696
NOTE: Before proceeding, secure clutch firmly in a
vise or other clamping device to prevent injury.
Step 2
Tighten the four hex nuts
uniformly until the clutch pack
and hub are loose.
Step 3
Bend all four retaining lugs
out on edge of clutch housing.
Step 4
Remove thrust plate with
Belleville Springs and lug
rings to access friction discs
and hub for inspection or
service.
4-Plate Disassembly
Step 1
If included, remove end half
clamps.
Step 5
Inspect friction discs and hub.
23553