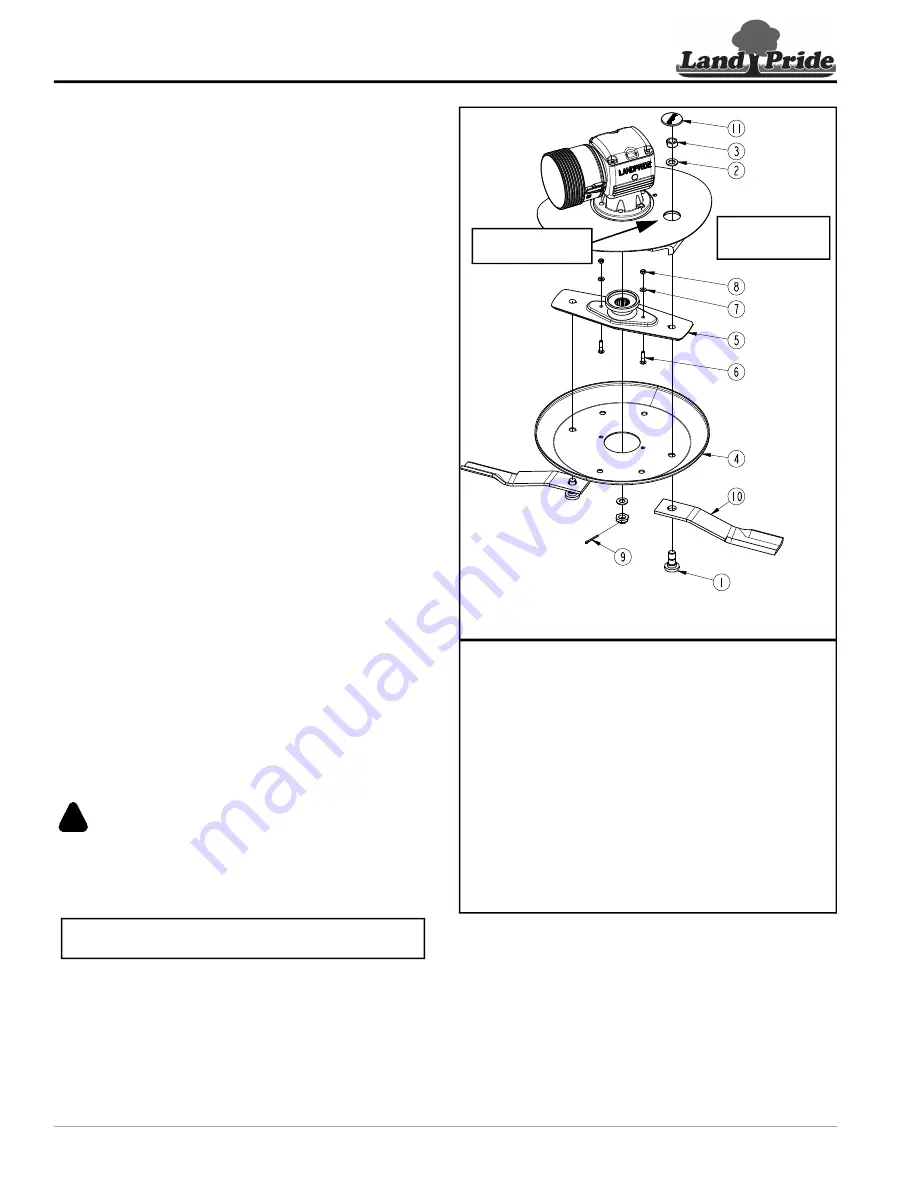
Section 5: Maintenance & Lubrication
RC(M)4715 & RCG(M)4715 Rotary Cutters 334-113M
6/3/20
48
Remove cutting blades and sharpen or replace as
follows:
1. Secure cutter deck in the up position with solid,
non-concrete supports before servicing underside of
cutter.
2. Shut tractor down properly before dismounting. Refer
to
3. Disconnect main driveline from the tractor.
4. Remove rubber plug (#11). Rotate dishpan (#4) until
blade bolt (#1) aligns with access hole (A).
5. Unscrew locknut (#3) to remove cutter blade (#10).
Blade bolt (#1) is keyed and will not turn freely.
6. Both blades should be sharpened at the same angle
as the original cutting edge and must be replaced or
re-ground at the same time to maintain proper
balance in the cutting unit. The following precautions
should be taken when sharpening blades:
a. Do not remove more material than necessary.
b. Do not heat and pound out a cutting edge.
c. Do not grind blades to a razor edge. Leave a blunt
cutting edge approximately 1/16" (2 mm) thick.
d. Always grind cutting edge so end of blade remains
square to cutting edge and not rounded.
e. Do not sharpen back side of blade.
f. Both blades should weigh the same with not more
than 1 1/2 oz. (0.04 kg) difference. Unbalanced
blades will cause excessive vibration which can
damage gearbox bearings and create structural
cracks.
7.
Carefully check cutting edges of blades in relation to
blade carrier rotation to ensure correct blade
placement. Cutter blades must be installed with
cutting edge leading in rotation
.
WARNING
!
To prevent serious injury or death:
A locknut that has been removed can lose its thread locking
properties. Reusing a used locknut can result in a thrown
blade. Always use a new locknut when installing blades.
8. Insert blade bolt (#1) through blade (#10),
dishpan (#4), and flat washer (#2). Secure blade with
a new locknut (#3) and torque to 450 ft-lbs (610
N· m
).
9. Replace rubber plug (#11).
10. Reconnect main driveline to tractor power take-off.
IMPORTANT:
Examine blade bolts and their flat
washers for excessive wear and replace if worn.
Forged Bar With Bolt-on Dishpan Assembly
Figure 5-9
Use 1-11/16"
Socket Wrench
On Blade Nut (#3)
Forged Bar With Bolt-on Dishpan
# Part No.
Part Description
318-586A BLADE BOLT KIT
(Includes items 1, 2, & 3 below)
1 802-277C BLADE BOLT
2 804-147C WASHER FLAT 1
3 803-170C NUT HEX TOP LOCK
4 331-507D BOLT ON DISHPAN
5 334-053H DIAMOND BLADE BAR
6 802-250C 1/2 - 13 X 2 1/4 GR5 BOLT
7 804-016C WASHER FLAT 1/2"
8 803-342C NUT HEX TOP LOCK 1/2 - 13
9 805-105C PIN COTTER 1/4 x 2 1/2
10 820-722C CUTTER BLADE 1/2x4x23 CW LH WING
10 820-721C CUTTER BLADE 1/2x4x29 CCW CENTER
10 820-720C CUTTER BLADE 1/2x4x23 CW RIGHT WING
11 840-273C PLUG LP 3" ID RUBBER
72288
Access Hole (A)