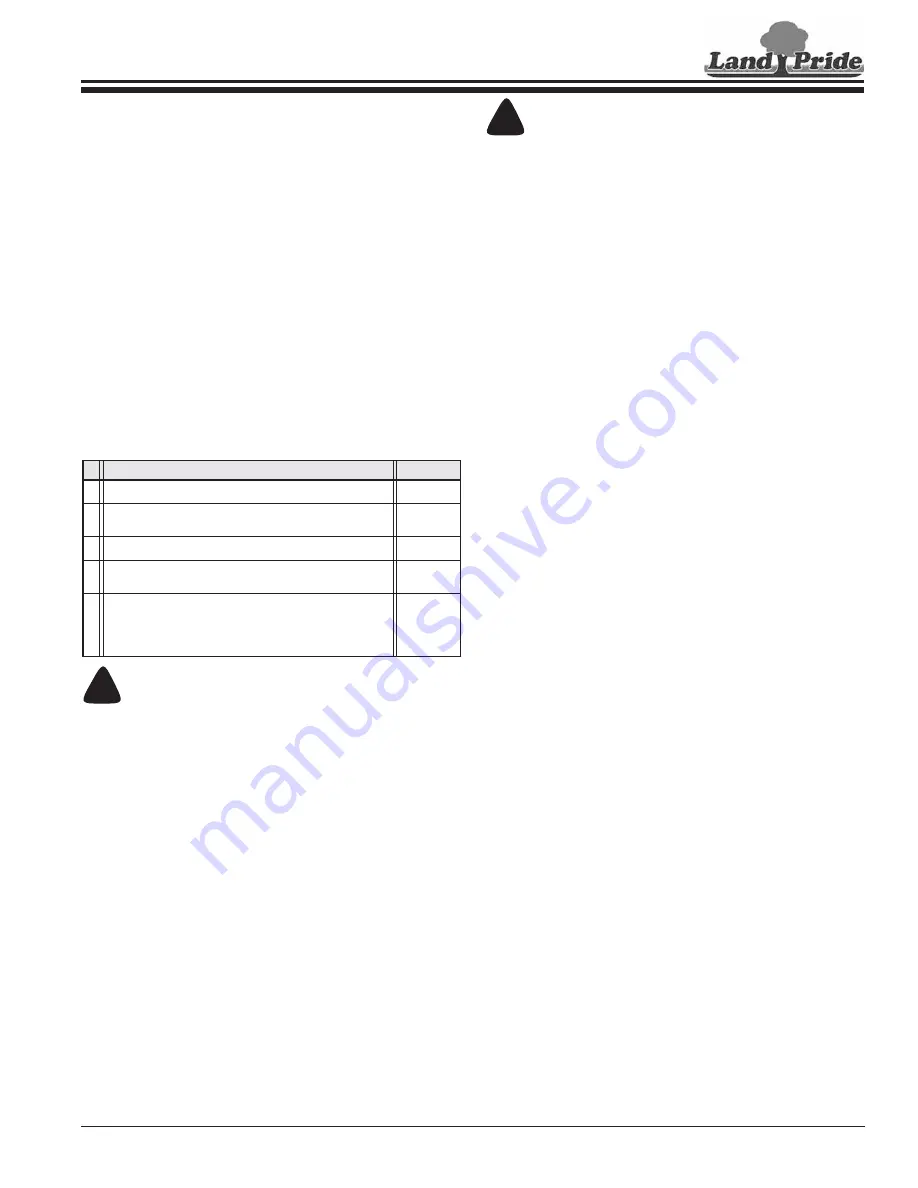
Section 4: Operating Procedures
DH3510 & DH3512 Disc Harrow 322-251M
12/7/18
25
Section 4: Operating Procedures
!
WARNING
To avoid serious injury or death:
•
Allow only persons to operate this implement who have
fully read and comprehended this manual, who have been
properly trained in the safe operation of this implement, and
who are age 16 or older. Serious injury or death can result
from the inability to read, understand, and follow
instructions provided in this manual.
•
Do not use implement to lift objects; to pull objects such as
fence posts, stumps, etc; or to push objects. The unit is not
designed or guarded for these uses.
•
Never carry riders on the implement or tractor. Riders can
obstruct the operator’s view, interfere with control of the
equipment, be pinched by moving components, become
entangled in rotating components, be struck by objects, be
thrown or fall from the equipment, etc.
•
Do not alter implement or replace parts on the implement
with other brands. Other brands may not fit properly or
meet OEM (Original Equipment Manufacturer)
specifications. They can weaken the integrity and impair the
safety, function, performance, and life of the implement.
Replace parts only with genuine OEM parts.
•
Perform scheduled maintenance. Check for loose
hardware, missing parts, broken parts, structural cracks,
and excessive wear. Make repairs before putting implement
back into service. Serious breakdowns can result in injury
•
Keep everyone away from the Disc Harrow while raising,
lowering, and transporting the implement to protect against
falling blade hazard.
•
Always make sure the tractor is shut off and no one is near
the tractor when installing stroke control spacers and/or
transport lock. Also, keep away from possible pinch points
during installation as the hydraulic lines could burst
dropping the unit suddenly.
•
Do not use tires as a step or lean against them. They can
suddenly move even when they appear to be solidly against
the ground causing a falling hazard against metal
protruding objects and sharp disc blades.
•
Make sure safety labels are in their proper location and are
in good condition before operating the attached implement.
Read and obey all instructions on the labels.
•
Pin drawbar in the fixed center position and make sure
tractor 3-Point arms are positioned so that they will not
make contact with the Disc Harrow hitch.
•
Raise Disc Harrow out of the ground to make sharp turns.
Do not turn tractor tires into the tongue or frame. Doing this
can result in loss of control and/or damage the implement.
Slow down and watch tractor tires carefully when forced to
make sharp turns.
•
Do not use implement to lift objects; to pull objects such as
fence posts, stumps, etc; or to push objects. The unit is not
designed or guarded for these uses.
•
Do not use implement to tow other equipment unless it is
designed with a tow hitch. Doing so can result in loss of
control and damage the equipment.
Operator’s Responsibilities
Hazard control and accident prevention are dependent
upon the awareness, concern, prudence, and proper
training involved in the operation, transport, storage, and
maintenance of the Disc Harrow. It is absolutely essential
that no one operates the harrow unless they are age 16
or older and have read, fully understood, and are totally
familiar with the Operator’s Manual. Make sure the
operator has paid particular attention to:
•
Important Safety Information
, page 1
•
•
Section 2: Optional Equipment Set-up,
•
•
Section 4: Operating Procedures
•
Section 5: Maintenance & Lubrication
Perform the following inspections before using your Disc
Harrow.
!
DANGER
To avoid serious injury or death:
•
Do not allow anyone near the tractor or implement while
operating. Stop operation if bystanders are too close. They
can be hit by flying projectiles, become entangled in the
•
Never make contact with underground utilities such as
electrical power lines, gas lines, phone lines, etc. They can
cause serious injury or death from electrocution, explosion,
or fire. If in doubt, call 811 (USA) before digging so that
they can mark the location of underground services in the
area. For contact information, see Dig Safe in the
“Important Safety Information” starting on page 1.
•
Always secure equipment with solid, non-concrete supports
before working under it. Never go under equipment
supported by concrete blocks or hydraulics. Concrete can
break, hydraulic lines can burst, and/or hydraulic controls
can be actuated even when power to hydraulics is off.
Operating Checklist
Check
Ref.
Read
“Important Safety Information”
1
Read all of the “Tractor Hook-up” and
preparation instructions.
Read
“Section 4: Operating Procedures”
Lubricate the harrow as needed.
Refer to
Check harrow initially and periodically for
loose bolts & pins. Pay special attention to disc
gang hanger bolts and axle nuts.
Refer to “Torque Values Chart”
.