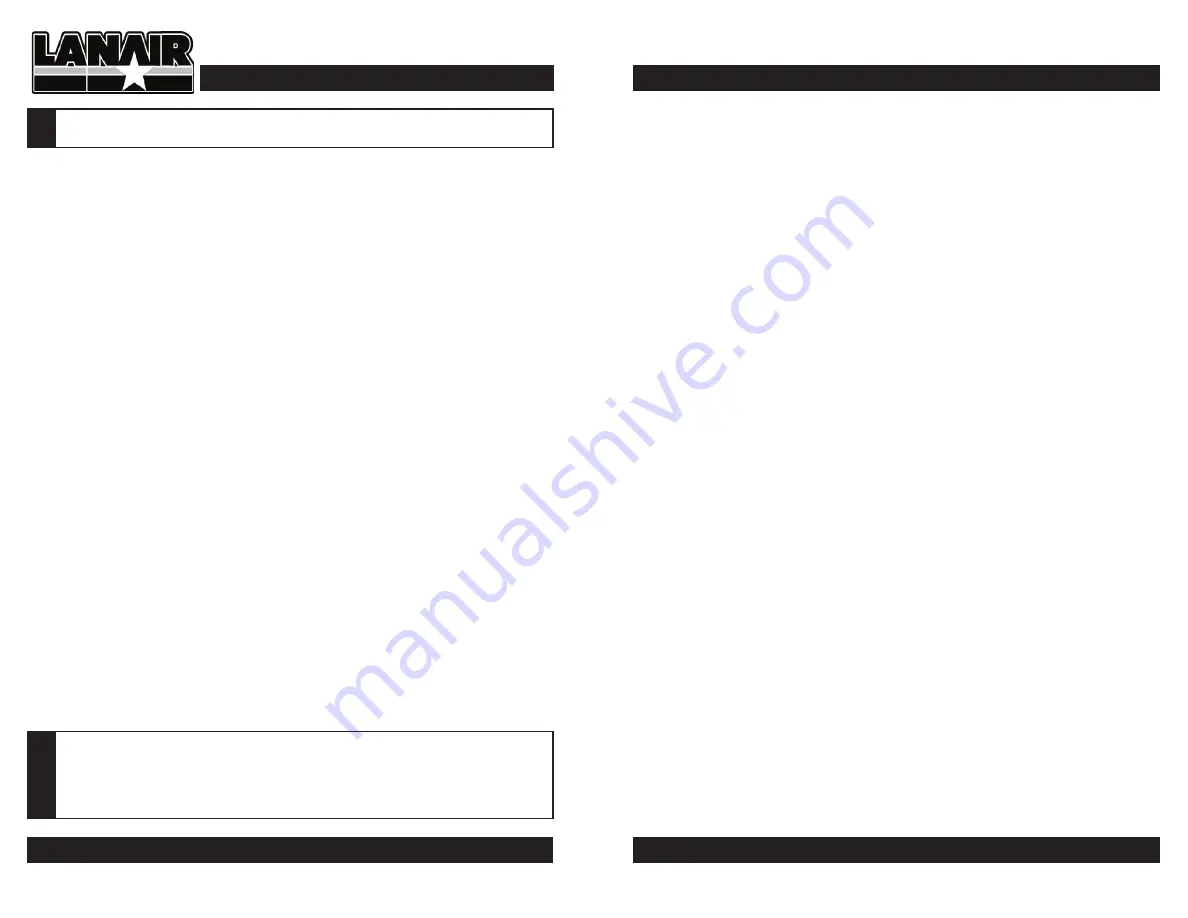
Section 5 - Fuel Supply Tank Installation
QUESTIONS?... Contact Customer Service at 1-800-753-1601 M-F 8:00 am- 4:15 pm CST
16
General Requirements
1.
The fuel supply tank and supply lines must be installed in accordance with the National
Fire Protection Association requirements, as well as State and Local ordinances.
2.
Regulations require oil storage tanks located inside not too exceed 275 gallons individu-
ally, and are not to exceed a total capacity of 550 gallons in one building. Check State
and Local codes.
3.
Locate the fuel supply tank inside the building as close to the heater as possible. It
should be no further than 25 feet from the heater to avoid oil flow problems.
4.
The fuel supply tank must be mounted below the level of the burner and the by-pass
regulator. Mounting the fuel supply tank above the burner will create head pressure and
over-fire the burner voiding the warranty.
5.
Pitch the fuel supply 2º with the drain valve at the lowest end to drain off water and
sludge. Sludge may have to manually be removed.
6.
Some ordinances may require the fuel supply tank to be vented to outside, and above
the roofline. Check State and Local codes. Keep the vent clear.
7.
Install the fuel tank fill pipe at the end of the tank and above the drain.
8.
Label the fuel tank for the recommended fuels.
9.
Strain all fuel with a 50 X 50 mesh strainer before putting fuel into the tank.
10.
When filling the fuel tank with a motorized pump, never leave unattended to prevent
over filling and/or spillage.
11.
Keep cap on the fuel tank when not filling.
If using a Lanair supply tank follow instructions included with the tank.
!
For optimum performance, the waste oil pump manufacturer recom-
mends that multi-weight oils such as 5W-30W be maintained at 32˚ F
minimum and straight weight oils such as 40W and 50W be maintained
at 50˚ F minimum.
!
Section 13 - Service / Maintenance
Visit our website at: www.lanair.com
37
Maintenance - OIl Pre-Heater
(cont.)
3. Clean Oil Pre-Heater Block
• Clean oil pre-heater block using a parts washer and brush.
NOTE:
Make sure all
passages are clean.
• Blow dry the oil pre-heater block. inspect
ALL
passages making sure they are clear and
clean.
4. Reassemble Oil Pre-Heater
• Replace four 13/16" OD o-rings (4) with new.
• Replace cartridge heater.
NOTE:
Do not over-tighten.
• Re-attach face plate (2) using six new hex cap screws (3) provided with tune-up kit
(P/N 7240).
• Apply loc-tite to three block plugs (12) and replace.
• Replace hex cap screw (9) inside oil pre-heater block (5).
• Replace o-ring (10) with new.
5. Attach Air Pre-Heater Assembly
• Align the holes of the ignitor assembly and air pre-heater with those of the oil pre-
heater (see page 34).
• Attach air pre-heater assembly to the oil pre-heater block (5) using two hex cap screws.
Tighten securely.
6. Re-install Pre-Heater Assembly
• Place the air/oil pre-heater assembly into the burner body.
• Align the holes of the pre-heater assembly with those in the burner body.
• Secure the assembly to the body by re-installing the button hex screw (14) and washer
(11).
NOTE
:Do not tighten this screw at this time.
• Replace the o-rings (7) on the PSI gauge and the oil line fittings (6) with new.
NOTE
:Do not tighten these fittings at this time.
• Adjust the pre-heater assembly for proper setting. The end of the turbulator should b
recessed approximately 1/4” into the burner tube (see page 38 for turbulator
adjustment).
• Once adjusted tighten button hex screw (14) and fittings (6)securely.
7. Re-connect Electrical
• Re-connect all wires previously disconnected in the electrical junction box (refer to
wiring diagram, page 21 and the burner reference diagram, page 51).
8. Reconnect PSI Gauge, Fuel Line and Air Line
• Reconnect the PSI gauge (8) to the fitting (6) and tighten securely.
• Reconnect the fuel line to the fitting (6) and tighten securely.
• Reconnect the air line by connecting the one end of the air line to the air solenoid and
the other end to the air fitting (see page 34).
9. Test Operation
• Follow start-up procedure, page 26.