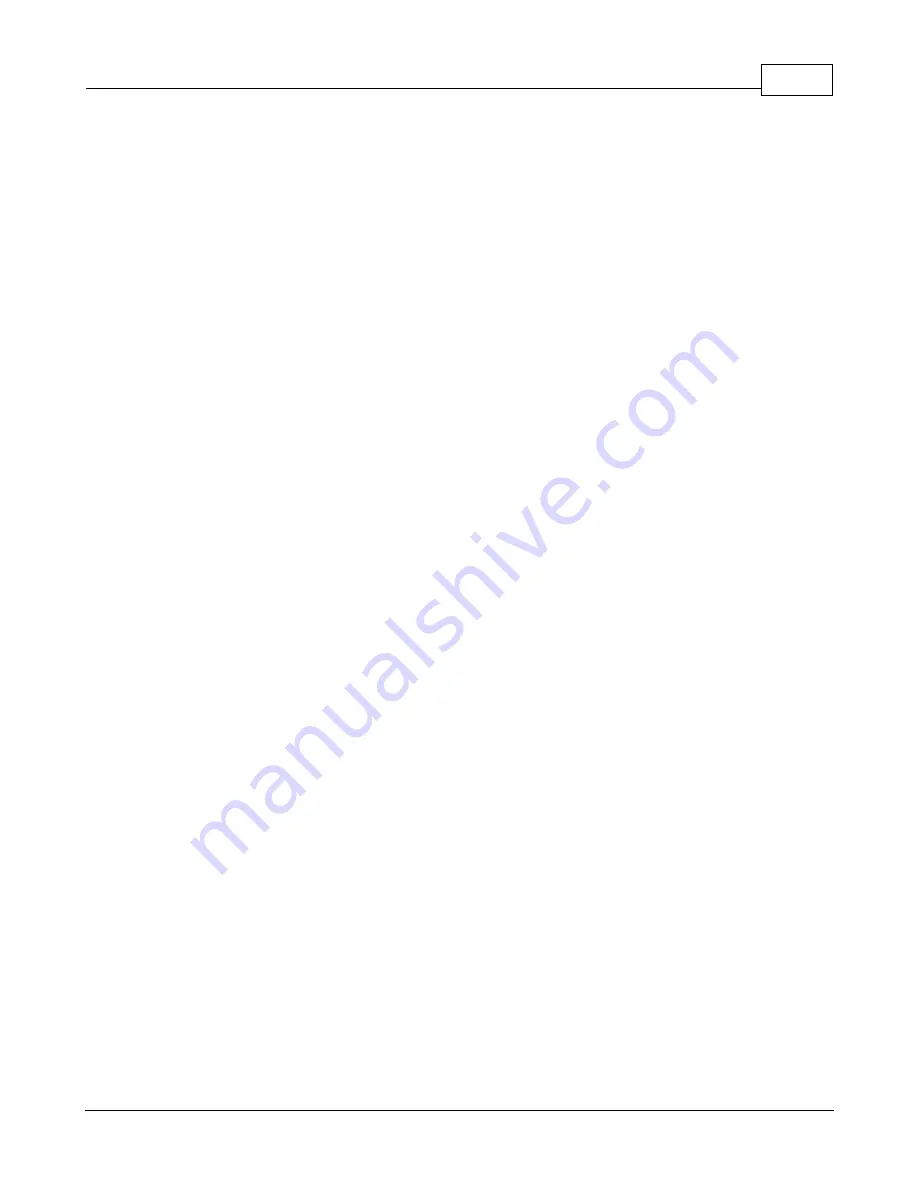
Mainteance
43
Tips for Maximum Performance
The versatility designed into the
SUPERMAX Drum Sander
allows it to be used for a wide-ranging variety of tasks
that will boost the return on your investment. For example, its capabilities range from taking the place of a planer to
thickness rough stock, all the way to speeding up fine sanding work often done with slower, dust-generating hand
sanders.
Learning to use its multiple adjustments and controls will allow you to fine-tune the machine for maximum results,
regardless of the job to be done. The best results come from experimenting with different abrasive combinations and
machine adjustments to fit the job at hand. Following is a listing of useful tips which can help you improve
performance of your sander.
Dust Collection-
When connecting dust collectors, remember that straight pipe will not restrict airflow as much as
flexible tubing. Also, Y’s and elbows will restrict airflow less that T’s. When connecting to the ports of the
SUPERMAX 37 or 37x2
,
SUPERMAX 25 or 25x2
use a larger diameter pipe to the machine, and then split to two
4" hoses connected to the ports. An alternative is to use two separate 4" lines running to the ports;
do not use
only one 4" line
and split it by the machine.
Multiple-Piece Sanding Runs-
When abrasive planing (or thickness sanding) a run of similar pieces that you want
to have the same thickness, it is best to determine the thickness of the thinnest piece and process all pieces to
that same thickness. Be aware that the sander will remove cups and crowns in the work piece; consider this when
measuring and processing stock to the same thickness.
Sanding Multiple Pieces at Once-
When sanding multiple pieces simultaneously, make sure to stagger or (step)
the pieces across the width of the conveyor belt. This provides better contact with the tension rollers. Try to only
process multiple pieces of similar thickness. If there is a significant thickness difference, the thinner pieces can slip
on the conveyor belt if they do not contact the tension rollers. Also note that pieces thicker than 3/4" should be
longer than the minimum normally recommended to prevent tipping of the stock (See Specifications, page XX).
Going to longer pieces is especially important when sanding boxes or other tall, short, or light stock.
Edge Sanding-
When edge sanding, the sander will mimic the opposite edge of the stock which is laying on the
conveyor belt. Because of this, it is important for the stock edge to have been ripped at the proper angle to the face
before the sanding process. When edge sanding stock that is less than 3/4" wide, or more than 2" high, it is good
procedure to stack and clamp several pieces together to prevent them from slipping or tipping on the conveyor belt.
Sanding Imperfect Stock-
When sanding stock with a cup or crown, place the crown up. This will stabilize the
stock to help prevent tipping or rocking during sanding. (After the crown has been removed and the top is flat, turn
the stock over and sand the opposite side.) To avoid personal injury, take special care when sanding stock that is
twisted, bowed, or otherwise varies in thickness from end to end. If possible, support such stock as it is being
sanded to keep it from slipping or tipping. Use extra roller stands, help from another person, or hand pressure on
the stock, to minimize potentially hazardous situations.
Face Frames & Raised Panel Doors-
It is very important to have the proper abrasive contact when doing this type
of sanding. If the machine is set to take an excessive depth of cut, the result can be a gouge or dip as the drum
goes from sanding the rails at full width to sanding just a few inches of width on the stiles. To prevent this problem,
for example, make sure that when using abrasives finer than 80 grit the drum is in contact with the wood but can
still be spun by hand. If there is room, angling the stock on the conveyor belt can also help. Slowing the conveyor
feed when coming to a rail in the stock can help prevent a dip or gouge. This allows the abrasive to work the
wider
width with less effort, and to achieve better consistency of the finished surface.
Stock Feeding Angle-
Some pieces, because of their dimensions, will need to be fed into the machine at a 90°
Summary of Contents for 37 x 2
Page 2: ......
Page 17: ...General Information 17 Castings...
Page 18: ...Double Drum Sander 37 x 2 18 Supermax Specifications...
Page 19: ...General Information 19 Supermax Accessory Supply Check List...
Page 47: ...Mainteance 47...
Page 54: ...Double Drum Sander 37 x 2 54...
Page 56: ...Double Drum Sander 37 x 2 56 Drumhead Assembly Exploded View...
Page 57: ...Drumhead Parts List 57 Drumhead Parts List...
Page 58: ...Double Drum Sander 37 x 2 58...
Page 59: ...Conveyor Exploded View 59 Conveyor Exploded View...
Page 60: ...Double Drum Sander 37 x 2 60 Conveyor Parts List...
Page 61: ...Conveyor Parts List 61...
Page 62: ...Double Drum Sander 37 x 2 62 Exploded Diagrams...
Page 63: ...Parts Lists 63 Parts Lists...
Page 77: ...Disassembly Procedure 77...
Page 79: ...Warranties 79 Warranties Laguna Tools Warranty...
Page 80: ...Double Drum Sander 37 x 2 80 Modifications RMA Policy Laguna Tools Packaging RMA Procedure...
Page 81: ...Warranties 81...