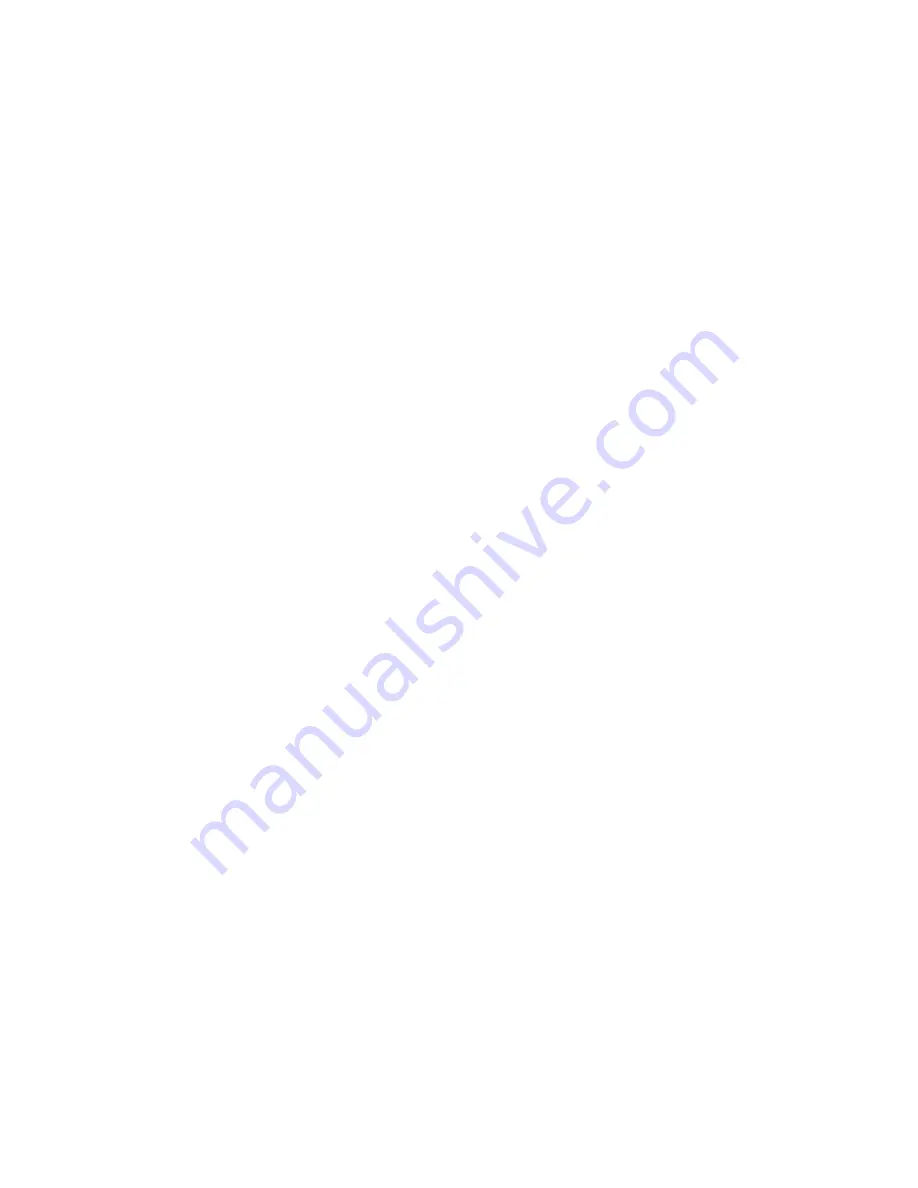
Original instructions
System Reset Switch
23
Information Center
24
Alarm Screens
25
Operating the Sliding Sash
26
Starting
the
Biosafety
Cabinet
26
The
Logic+
Touchpad
27
Navigating
the
Logic+
Menu
Screens
28
Navigating
the
MyLogic
TM
Menu
Screens
29-31
Setting the Clock
29
Configuring
the
Logic+
30-31
Navigating
the
Settings
Screens
31-34
Display
Options
31-32
Units of Measure
31
Startup Tone
32
Security Lock
32
RS-232
Output
Rate
32
UV Settings
33-34
UV Lamp Hourmeter
33
Reset UV Lamp Hourmeter
33
Change UV Lamp Life
34
Service Menu Screens
34
Timer Operation
35
Interval Timer Operation
35
Stopwatch
Timer
Operation 35
If
An
Airflow
Alert
Activates
35
Resetting
the
Airflow
Alert
System
35
Working
in
the
Biosafety
Cabinet
36-38
CHAPTER 6: MAINTAINING THE CABINET
39
Routine
Maintenance
Schedule
39-40
Service
Operations
40-44
Work Surface Removal
40
Front
Grille
Removal
40-41
Towel
Catch
Removal
41-42
Front
Panel
Removal
&
Installation
42-43
Changing
the
Fluorescent
Lamps
43
Changing
the
Optional
UV
Lamp
43-44
Resetting
a
Circuit
Breaker 44
Storage
44
CHAPTER 7: TROUBLESHOOTING
45-47
APPENDIX A: COMPONENTS
48-49
APPENDIX B: DIMENSIONS
50